What is the worst and most potentially dangerous lubricant practice you ever saw?
TLT Sounding Board February 2011
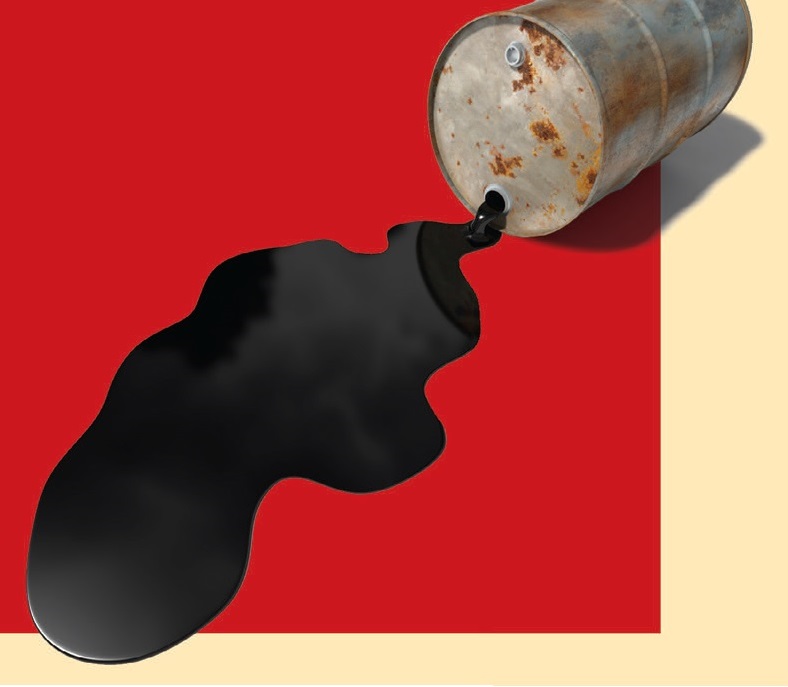
www.canstockphoto.com
Last month we asked our readers about the stupidest comments they’d ever heard about lubrication engineering. This month we go a step further and ask about the worst lubrication practices they’ve ever witnessed in facilities around the globe, and here all levity must end. Many of the practices cited here have resulted in serious injury to operators and maintenance personnel. They’ve also caused costly shutdowns, expensive and unnecessary repairs and the loss of millions of dollars in machinery. In the comments that follow, many survey respondents explain how they eliminated the poor practice and replaced it with safe and effective procedures.
A guy filled a tank, left the line in from a mini-bulk and walked away.
An oiler taking an oil sample from the drain pan.
Lubricating machinery while it was running. After a few slight injuries, safety guidelines were developed that required machine shutdown before work could begin.
I have seen people leaning precariously over a running machine in order to top off the oil tank, sometimes balancing on one foot while juggling a 10-lb. Transfer container and a funnel to accomplish the top-off.
In Russia I saw field equipment lubricated with crude oil straight from the well and only strained to remove solid matter.
Sending waste oil offsite using unlicensed waste handlers and/or haulers.
I watched a plastic injector molding company use a shop vac to suck up leaking hydraulic oil off the floor and put it right back into the bulk tank with no filtration. Then they wondered why valves were failing to open and close properly.
Had a plant that used its electric motor grease as the multipurpose, high-temp grease throughout the plant. They used their multipurpose high-temp grease only on electric motors.
Adding fluid concentrate as makeup for water-miscible metalworking fluid. I educated a potential customer as to the drawbacks of this practice and how to properly mix fluids for makeup use.
The general lack of understanding about the impact of low ambient temperatures on proper lubrication to a bearing or bearings.
Lubricating zerks on press feed equipment while the machine was running. Changed the practice by piping out fittings to manifolds located in safe areas.
A laboratory technician who knew nothing about lubrication out in the field changing the oil in a high percentage of the pumps onsite during a shutdown.
Installing an EP gear oil in compressors with soft metal. The oil caused corrosion of and failure of same component in three compressors in the production facility.
I heard of an airman who was assigned to lubricate the gear of a squadron of F-15s. He held a rag in one hand, a grease gun in the other. He’d stop at an aircraft, act like he had greased the gear, then put a daub of grease from his rag onto the fittings when things began to fall apart.
Having people climb to the top of a very high tower to lubricate a grease-lubricated bearing daily. One day in icy conditions the worker slipped and was severely injured.
Heat tracing a hydrocarbon lubricant in a day tank with superheated steam 600 F plus.
Mixing oil- and water-based lubes.
It’s not something I saw firsthand, but I did see a video of some Asian workers who were sitting in a die mold applying lube because the equipment was so antiquated.
I was at a place where the greaser greased the applications every morning at the same time, whether it needed it or not. The company could not figure out why it was having bearing failure. Replaced the bearings and then I had them go on a monitoring system to apply grease based on usage. No more bearing failure.
Using a lighter grease recommended only because it flowed faster and the oiler could get his job done quicker. Equipment looked messy as there was grease running everywhere.
An overseas mining concern was skimping on parts and lubrication for air compressors used to operate underground mines where several hundred workers were known to be dependent on the equipment at any given time.
In a large automotive plant, the foreman thought he was doing a MWF system dump, clean and recharge by opening the drain at one end of the system while adding clean, fresh fluid at the other.
A customer that saw only the price of the coolant going into the system, causing them to restrict the coolant makeup until the systems soured and could not be recovered.
A company used regular industrial hydraulic oil in a food processing cooking system. Resulted in fire in which people were hurt.
Dumping aftermarket additives into a finished, branded product with the expectation and promise of “improved performance.” In at least one instance, a customer ruined his screw compressor when the entire system varnished up from such a product. This $10 bottle of magic cost the customer $1,000 in repairs on his equipment.
Customer makes decision to purchase new oil based on the oil brand name without exploring the ingredients and quality base oil inside.
A mechanic had a habit of using a finger to locate the grease fittings on machinery and to guide a high pressure grease gun nozzle. One day, this individual succeeded in injecting his finger with grease. Gangrene set in. He can only count to nine now.
www.canstockphoto.com
The misuse and lack of cleanliness of oil cans. I have seen million-dollar haul trucks maintained with filthy lube trucks and oil containers, used for top off, that had dirt and rocks in them.
During an infomercial for a crankcase oil additive, the salesman demonstrated his product with a running engine, adding his additive to the oil. He then drained the crankcase (while the engine was running) to demonstrate how well the product worked. To top it off, he poured sand on top of the valve springs to demonstrate how the product kept the engine running. Of course, the infomercial wasn’t long enough to show how his removal of the crank oil or addition of sand shortened the life of the engine.
A maintenance worker attempting to extract an oil sample from a heat transfer system at a powered metal plant into a plastic container, no less. A more experienced worker saw the potentially dangerous situation and stopped the work.
Adding water to lubricant oil to increase the level.
Adding bleach to a water-based coolant sump to make the smell go away. The result was that the coolant split, the machine and parts rusted, and half the machinists had eye and throat irritation.
Oil analysis never really helps them because they just get the reports and store them in binders for audit purposes- that one’s for real!
Which statement best describes senior management’s perspective on the value of proper lubrication practices?
No problem—they get it right off the bat.
9%
If you can make your case plainly in dollars and cents, they eventually come around.
49%
It’s a real struggle to get them to understand—and too often they don’t.
37%
It’s almost hopeless—they just don’t get it.
5%
Based on results from some 7,000 TLT readers.
To save money on lubes in the compressor house of a tire manufacturing plant in Indonesia, the maintenance foreman used waste EP gear oil to lubricate the valves of the plant reciprocal compressors. When I asked how often they had to rebuild the valves and if they had any compressor fires, his comment was that labor was pretty cheap and that although fires occurred, they didn’t happen on a regular basis!
The use of a non-fire-resistant hydraulic oil when a fire-resistant hydraulic oil was needed. Putting out small fires was the norm for this facility.
Adding oil to a belt-driven blower without shutting it down. I had to write a proper procedure.
A sample came into the laboratory from a uranium mine in South Africa. Half was solid metallic uranium and the other half a bottle of oil-and they wanted to know why the transmission failed! I told them to move the breather above the operator’s head.
www.canstockphoto.com
I was a condition monitoring analyst, and we were having a lot of lubrication issues on the plant. The maintenance technicians were responsible for oil change-outs, oil sampling and topping up. One day I went down to the plant to see the maintenance technician topping up using a bleach bottle! I don’t think anyone would believe me, but it’s true—a bleach bottle. To make matters worse, they were topping up different grades of oil with the same bleach bottle. A total lubrication rationalization plan was developed that addressed all major lubrication issues from storage to handling to sampling. The plan was developed and presented to the maintenance team. Audits were then conducted to ensure that all the practices outlined in the plan were being practiced in the field. That was a tough one to pull off, but in the end all the issues were addressed and resolved accordingly.
Using a cheap grease in a low-temperature bearing used in aircraft.
I saw a soluble cutting oil used as a way lubricant. Since I only visited that account once, I can’t say what the outcome was.
Using contaminated containers to put new oil in the machine. Pump failed due to solids in the container.
www.canstockphoto.com
ATF is frequently substituted for HF. It may not be dangerous, but it is an inappropriate fluid for hydraulic circuit operations.
Allowing workers to eat in a work area and feel free to discard their food into the vat containing fluids.
Holes drilled in the top of the main press hydraulic reservoir to capture oil that leaked on top of the reservoir. ISO cleanliness levels ended up off the chart. Valves were sticking.
Running the lubricant too lean in concentration for the application.
The machinists responsible for monitoring lubrication did not monitor. They would not lube their machines until pumps cavitated, coolants developed bacteria, etc.
A maintenance supervisor combined two different oil sumps/tanks on a 50-ton forging machine into one, resulting in failure of one of the systems.
Use of base oil as lubricant without a single additive.
Blending different types/brands of car engine lubricants. The engine became noisy and consumed more fuel.
Mixing diesel engine oil into an air compressor during an oil change due to short supply of original compressor oil.
Use of manual transmission oil to replace engine, producing sludge.
At a quarry the manager said everything was lubricated with 30-weight oil. The quarry closed a short time later.
Poor storage and contamination, leading to degradation of the lubricant life.
Use lower-grade lube in the air conditioning compressor. After 3-4 years, the equipment broke down.
Applying open gear grease by hand. The very lucky guy had his disposable overalls caught by the gears and not his arm.
Two departments were working out of a central shop. Both used R&O 68 from a purple five-gallon drum that you could not see through to top off their pumps. Only problem was one side was putting waste oil in the five-gallon drum, and the other side was using it to top off their pumps. They could not understand why they had so many pump failures since they were both using the same synthetic oil. Moral: Only put used oil in clearly marked containers and always use clean top off containers that you can see through and are clearly marked.
Selling grease for a miniature ball bearing application that was clearly the wrong material for the application. Luckily it failed in testing.
An operator drawing from a drum of used oil to top up a system simply to make a point (on not labeling the drum) to the oiler.
In a steel mill, after an oil spillage from main tanks of the central lubrication system of a rolling stand, the oil was collected from the floor and put back directly in the tank without even a filtration process.
Not controlling external contaminants.
One shot per horsepower as a regreasing quantity for electric motors. The use of zinc oils in locomotives requiring zinc-free oil.
Operators who would take oils off the shelf without regard for the application and start mixing products. For example, mixing polyglycols with mineral oils.
Editor’s Note: Sounding Board is based on an e-mail survey of 13,000 TLT readers. Views expressed are those of the respondents and do not reflect the opinions of the Society of Tribologists and Lubrication Engineers. STLE does not vouch for the technical accuracy of opinions expressed in Sounding Board, nor does inclusion of a comment represent an endorsement of the technology by STLE.