Tier 4 engines: Setting a new standard
Jean Van Rensselar, Contributing Editor | TLT Cover Story February 2011
A small adjustment for end-users is yielding a big impact on the environment.
KEY CONCEPTS
• Once fully implemented, Tier 4 engines will significantly reduce diesel pollution.
• Although some specialized skills and equipment are needed to service Tier 4-compliant engines, most end-users will not need major service adjustments.
• API’s CJ-4 oils are critical for the durability and performance of Tier 4 engines running on the required ULSD fuel.
The U.S. Environmental Protection Agency is adopting requirements to reduce emissions of particulate matter, nitrogen oxides and air toxics from off-road diesel engines. The Tier 4 rule includes emission standards for new off-road diesel engines, now in effect for many of these engines.
The rule also reduces the level of sulfur for diesel fuels used in off-road, locomotive and marine engines, with the reduction phasing in from 2007-2014. The requirement for reduction in sulfur for off-road diesel fuel will help enable equipment to make use of advanced emission-control technology in meeting the Tier 4 standards.
This Tier 4 program is expected to yield significant public health and welfare benefits by reducing emissions of particulate matter (PM) and nitrogen oxides (NOx) from off-road, locomotive and marine diesel engines.
In 1996, before any standards were in effect, emissions from land-based off-road engines, locomotive engines and marine diesel engines were estimated to contribute about 40% of the mobile source emissions of particulate matter (less than 2.5 microns in diameter) and 25% of the NOx. Of this, land-based off-road diesel engines contributed about 47%.
Experts believe that, without regulation, the percentage would grow to about 70% by 2020.
The tiered series of emissions regulations has been in effect in the U.S. since 1996 and regulates new off-road engines and equipment. These Tier 1-3 standards have established progressively lower emissions standards of NOx and PM. Compliance dates are based on factors such as engine size (in hp) and engine application.
The latest Tier 4 standards provide manufacturers with a flexibility provision and include a Tier 4 interim step that, while requiring substantial reduction in Pm emissions, allows flexibility in lowering hydrocarbons (HC) and NOx. The Tier 4 final step includes additional reductions in NOx and HC emissions.
By contrast an unregulated, mechanically controlled pre-Tier 1 engine has no advanced emissions controls.
The tiered standards apply to machines operated in the U.S. and not to machines exported outside the country. The U.S. off-road emission standards are largely harmonized with European off-road emission standards (1, 2).
PROJECTED HEALTH IMPACT
Diesel exhaust is a particular concern because, when inhaled, it is likely carcinogenic to humans. It also poses a hazard from non-cancerous respiratory effects. Ozone, NOx and PM have other negative effects such as crop contamination and damage, atmospheric haze and building soot.
EPA estimates that so far the Tier regulations have reduced NOx emissions by about a million tons per year, the equivalent of taking 35 million passenger cars off the road. EPA studies also show that when the full inventory of older off-road engines are replaced by Tier 4 engines, annual emission reductions will reach an estimated 738,000 tons of NOx and 129,000 tons of PM. By 2030, EPA says the Tier standards would prevent 12,000 premature deaths, 8,900 hospitalizations and 1 million lost work days annually.
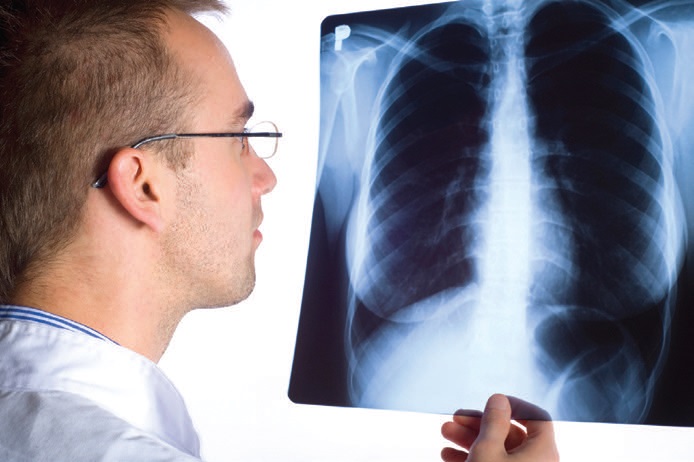
www.canstockphoto.com
PROJECTED COSTS
EPA expects the costs of adding the advanced emission controls and modifying the equipment to accommodate the redesigned engine will add somewhere between less than 1% to 3% to the purchase price of typical new off-road diesel equipment.
EPA estimates that the average cost increase for the required 15 ppm s fuel will be seven cents a gallon. That amount could be reduced by lower maintenance costs of using low sulfur diesel fuel.
In all, the Tier 4 program is expected to cost about $600 per ton of NOx reduced (or about $2 billion per year). On the other hand, EPA estimates an overall quantifiable benefit of over $83 billion annually by 2030.
EPA says the Tier standards would prevent 12,000 premature deaths, 8,900 hospitalizations and 1 million lost work days annually by 2030.
FORERUNNERS: TIERS 1-3
The first federal standards for new off-road diesel engines were adopted in 1994 for engines over 37 kW (50 hp). The standards cover mobile off-road diesel engines used in a wide range of construction, agricultural and industrial equipment.
The EPA definition of an off-road engine is based on mobility/ portability and includes engines installed on:
1. Equipment that is self-propelled.
2. Equipment that is propelled while performing its function.
3. Equipment that is portable or transportable as indicated by the presence of wheels, skids, carrying handles, a dolly, a trailer or a platform.
Essentially, off-road engines are all diesel engines except highway engines, engines in one location for more than 12 months, engines used solely for competition or aircraft engines.
Given this, off-road diesel emission regulations are not applicable to all off-road diesel engines. Exempted are the following off-road categories:
• Engines used in railway locomotives (subject to separate EPA regulations).
• Some engines used in marine vessels (subject to separate EPA regulations).
• Engines used in underground mining equipment. Diesel emissions and air quality in mines are regulated by the mine safety and health administration.
• Hobby engines (below 50 cm3 per cylinder).
Each Tier involves a phase-in (by horsepower rating) over several years. Tier-1 standards were phased in from 1996 to 2000. Tighter Tier-2 standards took effect from 2001 to 2006, and more stringent Tier-3 standards were phased in from 2006 to 2008.
In 1998 a Statement of Principles (SOP) pertaining to off-road diesel engines was finalized between the EPA, the California Air Resources Board and engine manufacturers that included Caterpillar, Cummins, Deere, Detroit Diesel, Deutz, Isuzu, Komatsu, Kubota, Mitsubishi, Navistar, New Holland, Wis-Con and Yanmar. The SOP, with a phase-in from 2000-2008, added Tier-1 standards for equipment under 37 kW (50 hp) and increasingly more stringent Tier-2 and Tier-3 standards for all equipment.
Tier 1-3 standards were satisfied through advanced engine design with little or no use of exhaust gas after-treatment (oxidation catalysts). Tier 4 compliance will be much different.
TIER 4 CHANGES
First of all, it’s important to note that Tier 4 emissions requirements apply to new machines and equipment only and do not apply retroactively to existing machines or equipment.
The primary focus of the Tier 4 program is the transfer of catalyst-based emission control technologies developed for on-highway diesel engines to off-road diesel engines.
The Tier 4 emission standards—phasing in between 2008-2015—introduce substantial reduction requirements of NOx (for engines above 19 kW) and PM, as well as more stringent HC limits. CO emission limits remain unchanged from the Tier 2-3 stages.
Using the similarly strict 2007-2010 compliance protocol for highway engines, these emission reductions can be achieved through the use of control technologies such as advanced exhaust gas after-treatment.
OFF-ROAD DIESEL FUEL
At the Tier 1-3 stages, the sulfur content in off-road diesel fuels was not limited by environmental regulations. Because the required Tier 4 emission-control devices can be damaged by sulfur, EPA adopted a limit to decrease the allowable level of sulfur in off-road diesel fuel by more than 99%.
Sulfur significantly inhibits or impairs the function of the diesel exhaust emission control devices, which will generally be necessary for off-road diesel engines to meet the emission standards in this final rule.
Before Tier regulations began to take effect, the oil industry specification for sulfur in diesel fuel was 0.5% (wt., max), with the average in-use sulfur level of about 0.3% = 3,000 ppm. To comply with Tier 1 through Tier 3 standards and then enable sulfur-sensitive control technologies in Tier 4 engines—such as catalytic particulate filters and NOx adsorbers—EPA mandated the following sulfur content reductions in off-road diesel fuels:
• 500 ppm effective June 2007 for non-road, locomotive and marine (NRLM) diesel fuels.
• 15 ppm (ultra-low sulfur diesel) effective June 2010 for off-road fuel, June 2012 for locomotive and marine fuels.
Estimated costs of an additional seven cents a gallon (related to changing to ultralow- sulfur fuel) take into account all of the necessary changes in both refining and distribution practices. The required ultra-low sulfur diesel fuel (ULSD) must have no more than 15 ppm sulfur. This fuel has been used since 2006 in highway vehicles. Older off-road machines without Tier 4 modifications can continue to use the higher sulfur fuels which will be available in diminishing quantities nationwide.
OTHER PROVISIONS
Existing Tier 2-3 smoke opacity standards and procedures continue to apply in some engines. Exempted from smoke emission standards are inherently low smoke emission engines certified to Pm emission standards at or below 0.07 g/kWh. Like earlier standards, Tier 4 includes such provisions as limited emission averaging, banking and trading of emission credits.
While Tier 4 does not require closed crankcase ventilation in off-road engines, in engines with open crankcases, crankcase emissions must be measured and added to exhaust emissions in assessing compliance.
TEST CYCLES AND FUELS
Off-road engine emissions are measured on a steady-state test cycle that is nominally the same as the ISO 8178 C1, 8-mode steady-state test cycle. Other ISO 8178 test cycles are allowed for selected applications such as constant-speed engines (D2 5-mode cycle), variable-speed engines rated under 19 kW (G2 cycle) and marine engines (E3 cycle).
Tier 4 standards must be met over both the steady-state test and the non-road transient cycle (NRTC). The transient testing requirements begin in 2011 for 130 kW-560 kW engines, 2012 for 56 kW-130 kW engine and 2013 for engines below 56 kW (4).
The NRTC protocol includes a cold-start test. Cold-start emissions are weighted at 5%, and hot-start emissions are weighted at 95% in calculating the final result.
Tier 4 off-road engines also must meet not-to-exceed standards (NTE), which are measured without reference to any specific test schedule. The NTE standards become effective in 2011 for engines above 130 kW, 2012 for 56 kW-130 kW and 2013 for engines below 56 kW. In most engines, the NTE limits are set at 1.25 times the regular standard for each pollutant (in engines certified to NOx standards below 2. 5 g/kWh or Pm standards below 0.07 g/ kWh, the NTE multiplier is 1.5).
The NTE standards apply to engines at the time of certification, as well as in use throughout the useful life of the engine. The purpose of the added testing requirements is to prevent the possibility of defeating the test cycle with electronic engine controls and by producing off-cycle emissions (5).
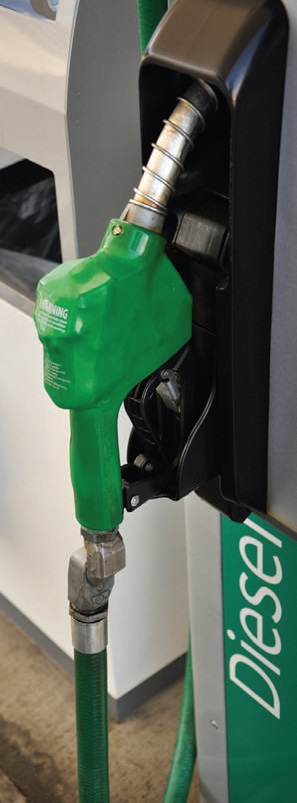
www.canstockphoto.com
CERTIFICATION FUELS
Fuels with sulfur levels no greater than 0.2 wt% (2,000 ppm) are already used for certification testing of Tier 1-3 engines. From 2011, all Tier 4 engines will be tested using fuels of 7-15 ppm sulfur content. A transition from the 2,000 ppm s specification to the 7-15 ppm specification occurred in the 2006-2010 period.
A change from measuring total hydrocarbons to non-methane hydrocarbons was introduced in the 1998 rule. Since there is no standardized EPA method for measuring methane in diesel engine exhaust, manufacturers can either use their own procedures to analyze nonmethane hydrocarbons or measure total hydrocarbons and subtract 2% from the measured hydrocarbon mass to correct for methane (6).
ENGINE USEFUL LIFE
Specified emission standards must be met over the entire useful life of the engine. EPA requires the application of deterioration factors to all engines covered by Tier 4. The DF represents emission levels at the end of the engine’s useful life.
Depending on the machine, according to EPA regulations, manufacturers will only be able to produce the Tier 4 engines after established deadlines, although equipment dealers can sell inventories of Tier 3 engines and equipment until their inventories are depleted.
TIER 4 LUBRICANTS
Tier 4 requirements apply only to new engines. There is no federal mandate to upgrade any existing engine to the new Tier 4 standards.
Historically, emission-control development for gasoline vehicles and engines was concentrated on after-treatment technologies (i.e., exhaust system catalyst technologies) that currently can provide more than 95% of the emission control of a gas-powered vehicle. In contrast, the emission-control development for highway and non-road diesel engines has concentrated on emission-limiting improvements to the engine itself.
More recently, R&D dollars have been going into catalytic exhaust emission-control devices for diesel engines, particularly Pm control. Those developments and recent developments in diesel NOx exhaust emission-control devices allow the commercial use of highly efficient diesel exhaust emission controls. The feasibility and availability of this new technology is primarily why the EPA began setting tier standards for highway diesel engines in the first place.
Although the primary focus of the Tier 4 emissions program is directed at the application of catalytic emission control technologies enabled by ULSD fuel, there are also important elements of the program based on continuing improvements in engine-incorporated emission controls.
Like advanced catalytic-based technologies, these engine- incorporated emission solutions for off-road diesel engines rely on technologies already deployed in highway diesel engines. These technologies also form the basis for the Tier 3 emission standards for some off-road diesel engines in other size categories.
ENGINE & EQUIPMENT CHANGES
There are a number of new technologies that will be incorporated into Tier 4 engines and equipment. For the equipment, the changes likely to be most noticeable are in packaging and placement of the after-treatment system and the increased size of the air intake system to accommodate the needs for increased airflow and cooling.
New changes to the engine likely will mean that engine compartments must be reworked to accommodate the new systems. Some OEMs will package any new exhaust system configuration inside reworked sheet metal skin, while others will place the systems in existing configurations that include extra shielding and mounting hardware to support the heavier exhaust system components.
Most Tier 4 engines will be electronically controlled, meaning that a computer monitors and adjusts the fuel and air mixture to optimize real-time engine emissions and performance.
Additional changes in the engine will include new and different systems to allow for the increased heat rejection of the new engines.
For the first time, most off-road equipment will incorporate emissions control technology in the exhaust system such as a catalytic converter and/or particulate filter, typically in place of the existing muffler and exhaust system. Some of these new exhaust after-treatment systems mean that the configuration and placement of the muffler and exhaust may be different (potentially larger) than that in existing equipment.
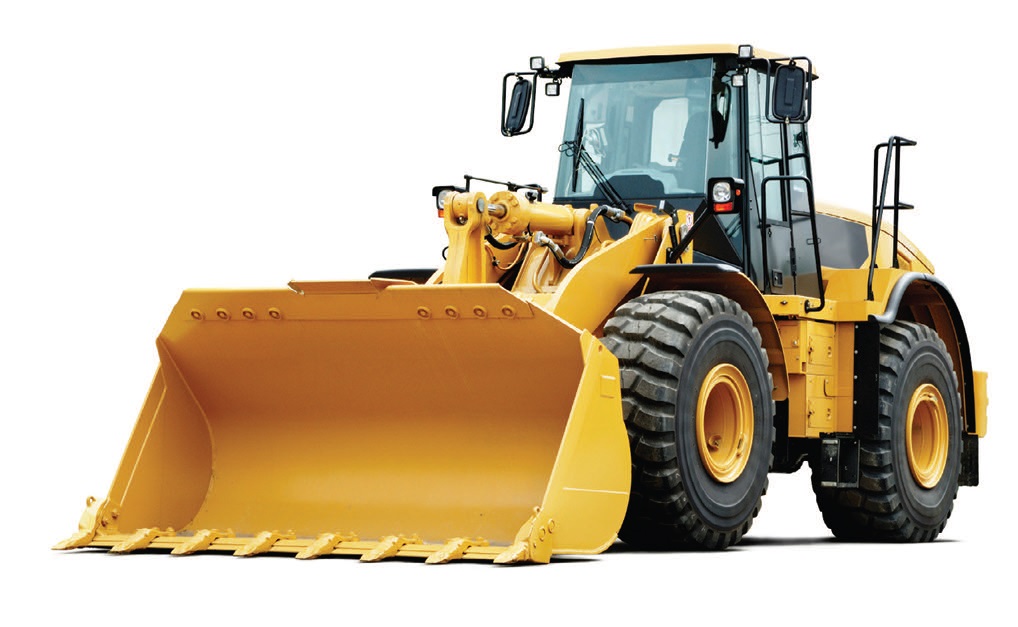
www.canstockphoto.com
MEETING THE REQUIREMENTS
There are three primary technologies for complying with Tier 4 requirements:
1. Exhaust Gas Recirculation (EGR).
2. Diesel Particulate Filters (DPF).
3. Selective Catalytic Reduction (SCR).
EGR. EGR involves the recirculation of a portion of the exhaust gases back into the combustion chamber. This has the effect of lowering the combustion temperature and reducing NOx formation. Although this system adds additional manifolds and plumbing around the engine, it is much less disruptive than SCR.
“EGR will allow the NOx requirements to be met but also, with the use of SCR, this will lower the exhaust gas regeneration rate allowing better engine performance,” says STLE-member Ray Thibault, principal of Lubrication Training and Consulting in Cypress, Texas, who also has 31 years of experience with ExxonMobil.
“Use of EGR could reduce the exhaust gas regeneration rate down to 15%,” Thibault adds. Another advantage of SCR is that it helps regenerate the oxidation catalyst by allowing more NOx from the engine, which helps regenerate the catalyst. The SCR reacts with the NOx to keep the amount in the exhaust low.”
DPF. A DPF removes diesel particulate from diesel engine exhaust gas. The filters can remove more than 85% of the waste particulate. Diesel machinery with an adequate DPF should emit no visible exhaust.
There are a variety of diesel particulate filter types on the market. Each fulfills similar requirements. Some dPFs are disposable, and others are designed to burn off the particulate, most commonly through a catalyst or a fuel burner.
SCR. One of the biggest changes for engine and equipment dealers is that, as NOx requirements become more stringent, some engines/machines will utilize the new SCR emissions control technology—not widely used in the U.S. yet.
SCR involves a special catalyst positioned in the exhaust stream/muffler system downstream from an active spray dosing system that sprays a chemical reagent mist called diesel exhaust fluid (DEF)commonly known as aqueous ureaat regular intervals. This reacts with the exhaust nitrogen oxides and lowers emissions. The DEF dosing system, supply and return tubing and control and monitoring functions are all integrated into the electronic engine controls.
The DEF consumption is dependent on such factors as equipment utilization and load. Depending on its size, a machine’s storage tank might need to hold as much as 15 gallons of liquid DEF.
Manufacturers are optimizing SCR technology and DEF tank sizes so that DEF tanks can be replenished at regular maintenance intervals. Dash indicator lights warn the operator when the DEF supply is running low and needs to be replenished.
OTHER TIER 4 DIFFERENCES
Tier 4 engines and machines may have other differences depending on the manufacturer. These could include changes in areas such as:
• Horsepower ratings
• Smaller engine displacements
• Power performance differentials
• Torque performance differentials
• Higher fuel economy.
OEMs are producing products that are both lower in emissions and either maintain or increase previous engine performance. Because most manufacturers are building Tier 4 technology off of proven Tier 3 platforms, they can maintain or improve performance in areas such as:
• Cold-weather starting
• Transient response time
• Power bulge
• Peak torque
• Low-speed torque.
ULTRA-LOW SULFUR DIESEL
Under typical operating conditions, there should be no noticeable impact on overall power using ULSD fuel. Maximum power-sensitive applications may experience a slight reduction in power. Also, fuel economy of all applications may be reduced slightly because the process that removes sulfur also can reduce the energy content of the fuel. However, from a maintenance perspective, ULSD requires no additional considerations.
API’s CJ-4 OIL
Since engines meeting new tier standards will be equipped with advanced emission control systems, including diesel particulate filters and EGR, the American Petroleum Institute (API) developed the CJ-4 oil performance category to address both the unique needs of tier engines and protection of older engines. At the same time, to comply with the new regulations, CJ-4 oils will extend the life of the emission control system.
CJ-4 oils, used in engines running on ULSD fuel, are critical for the durability and performance of engines that employ advanced emission-control technologies. These oils have additives designed to improve the protection of both the engine power system and advanced emissions control systems.
“The base number for CJ-4 oils is lower than for CI-4 Plus (an earlier API classification) because of the lower ash requirement and ASTM 2896 ranges from 8.5-10.0,” Thibault says. “Because of the sulfur requirement, which didn’t exist for CI-4 Plus oils, CJ-4 oils need to be formulated with a Group II basestock. Also, because of the enhanced oxidation and dispersant package and the Group II basestock requirement, CJ-4 oils cost more than CI-4 Plus oils.”
When compared to previous API performance categories, CJ-4 oils are formulated for:
• Improved wear protection
• Improved deposit and oil consumption control
• Improved soot-related viscosity control
• Improvement of the used oil’s ability to pump at low temperatures
• Prevention of viscosity loss from shearing
• Protection from thermal and oxidative breakdown.
These oils have been subjected to stringent testing requirements and are designed to meet engine manufacturer and end-user requirements in terms of both engine performance and maintenance intervals.
Thibault says that Komatsu has the additional requirement for CJ-4 oils that they must pass the hot tube test and the deposit test for turbochargers and pistons. Caterpillar ECF3 requires passing an oil consumption rate test as the oil ages and passing a piston deposit test.
According to Corey Taylor, BP’s senior heavy-duty technical support technologist, BP offers three HD engine oils that are suitable for use in Tier 4 engines.
SAPS
Low SAPS lubricants are formulated to reduce the presence of sulfated ash, phosphorus and sulfur. Tier 4 compliant engines may be fitted with a diesel particulate filter designed to trap exhaust particulates before they reach the environment. The problem is that over time ash produced from lubricant additives can clog the DPF. Low SAPS lubricants produce far fewer ash-forming deposits than other lubricants and have far less tendency to clog the DPF. In addition, because they allow engines to run more efficiently and reduce fuel consumption, low-SAPS lubricants:
• Reduce CO2 emissions
• Provide better protection against viscosity breakdown
• Provide fast lubrication at extremely low temperatures
Low SAPS lubricants meet both ACEA (European Automobile Manufacturer’s Association) rating C1 to C3 and API SM and ACEA A3/B3. However, the ACEA warns that these lubricants shouldn’t be used in engines with catalytic converters (7).
OIL ANALYSIS
Tier 4 reduces allowable emissions to very low levels. In order to accommodate the necessary technologies, there must be a number of changes in engine and equipment design. While each OEM will develop and follow its own strategy, existing exhaust and muffler systems could undergo changes that include particulate filters, oxidation catalysts, lean-NOx traps and/or SCR.
CONDITION MONITORING
Technicians will need to be comfortable with electronically controlled engines, exhaust after-treatment control, measuring Back pressure and, of course, general exhaust equipment maintenance and operation. In addition, they should be familiar with the relevant material safety data sheets and be well-versed in the safe handling, storage, disposal and dispensing of diesel exhaust fluid.
For equipment with SCR technology, technicians will need to be specifically trained in aspects of SCR technology, including fluid flows, fluid pressures, basic troubleshooting and SCR components like the catalyst, storage tank, spray nozzle and plumbing systems.
Some manufacturers likely will include new dash warning lights and gauges to indicate levels and conditions of new diesel exhaust fluid or the condition of particulate filters.
Despite this, core condition monitoring tasks will remain the same.
“We are not expecting any changes to condition monitoring,” BP’s Taylor says. “Customers will still want to monitor wear metals, soot, oxidation, viscometrics, nitration, fuel, water, glycol and TAN/TBN to ensure proper lubricant performance.”
European Emission Standards (8)
The European emission standards for new off-road diesel engines have been structured as gradually more stringent tiers known as Stage I-Stage IV standards. Additionally, emission standards have been adopted for small, gasoline fueled off-road engines.
Stages I and II. The first European legislation to regulate emissions from off-road mobile equipment was instituted on Dec. 16, 1997. The regulations for off-road diesels were introduced in two stages: Stage I implemented in 1999 and Stage II from 2001 to 2004, depending on the engine power output.
Stages III and IV. Stage III and IV standards, in addition to the engine categories regulated at Stage I and II, also cover railroad locomotive engines and marine engines used for inland waterway vessels.
These emission standards were adopted by the European Parliament for off-road engines on April 21, 2004, and for agricultural and forestry tractors on Feb. 21, 2005. Stage III standards—which are further divided into Stages IIIA and IIIB—are being phased-in from 2006 to 2013. Stage IV will be enforced in 2014.
To represent emissions during real conditions, a new transient test procedure—the Non-Road Transient Cycle (NRTC)—was developed in cooperation with the EPA. The NRTC is run twice with a cold and a hot start. The final emission results are weighted-averages of 10% for the cold start and 90% for the hot start run. The new test is used in parallel with the prior steady-state schedule, ISO 8178 C1, referred to as the Non- Road Steady Cycle (NRSC).
ADDITIONAL DIAGNOSTIC EQUIPMENT
Because some Tier 4 engines may use particulate filter technology that requires periodic maintenance and/or removal, repair and maintenance facilities may need additional equipment to fully service filters such as ovens and cleaning cabinets. SCR emissions-control technology requires that service facilities maintain supplies and dispensing equipment to fulfill DEF service requirements. Other than that, there is no additional diagnostic equipment needed for Tier 4 maintenance and diagnostics.
ADDITIONAL MAINTENANCE
Some Tier 4 engines may have additional or different maintenance requirements. These new requirements could include changes in the types of engine oil, the frequency of recommended oil changes, changes in air filters and fuel filters and changes in routine maintenance on the exhaust particulate filter systems.
SCR technology-equipped engines will have to be periodically filled with DEF (at a maintenance interval or on the job site depending on manufacturer design). Equipment that uses diesel particulate filters will require exhaust filter maintenance at intervals typically of 3,000 to 4,500 hours.
Because there are maximum limits on the phosphorus, sulfur and sulfated ash content of oils, CJ-4 oils may have a different fresh oil chemical profile than previous oils. Technicians should ask their oil supplier and/or OEM about changes to used-oil analysis programs for CJ-4 oils.
“Simply stated, engines designed to meet EPA Tier 4 requirements are similar to on-road EPA 2007 engines in their use of EGR and exhaust after-treatment, which would be diesel particulate filters,” Taylor says. “Accordingly, Tier 4 engines employ very similar technology and do not require a new lubricant. Lubricants which meet API CJ-4/OEM requirements are suitable for use in Tier 4 engines.”
Taylor adds that in addition to SAPS lubricants and API CJ-4, some OEM specs carry other requirements. For example, Komatsu has its own specification for lubricant performance in its Tier 4 engine that is unlike CJ-4 or that of any other OEM.
BOTTOM LINE
For complying with tier 4 standards applicable to off-road diesel fuel in 2010 and to locomotive and marine diesel fuel In 2012, OEMs and refiners can capitalize on the experience gained from complying with similar standards already in place for highway equipment. An added advantage is that refiners now can take advantage of recently commercialized reduced-cost desulfurization technologies. Some of the hurdles overcome in complying with highway equipment standards, such as limiting sulfur contamination during distribution, also will smooth the way for Tier 4 compliance.
As new ozone and Pm standards are adopted over the next five years, state and regional officials will look for timely, cost-effective ways to reduce emissions through regulations and incentives that encourage retrofitting existing engines and equipment reduce emission levels.
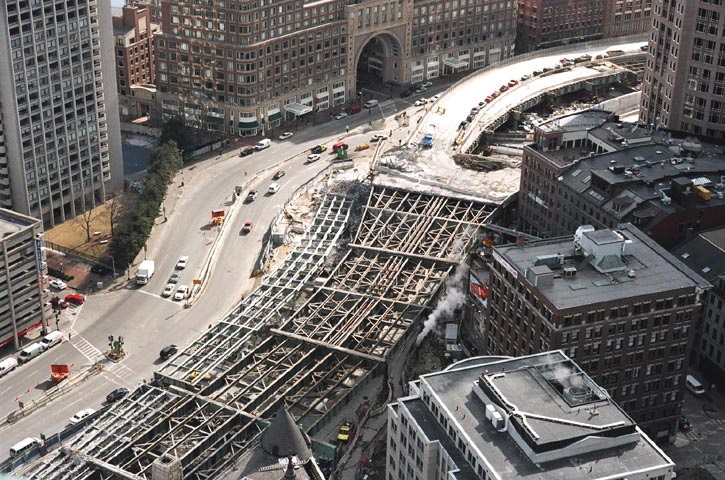
Boston’s Big Dig
Right now no one really knows if Tier 4 emissions technology will have direct impact on the value of older equipment and engines. It’s worth considering, however, that equipment owners will increasingly encounter contract specifications, job bids, project riders and contingencies that take into consideration the emissions profile of their equipment in the project bidding and award process.
One of the first and most visible national projects to have such a requirement was Boston’s Big Dig—the construction of a central artery and tunnel through the city. Another fairly recent example is the green construction specifications stipulated by Illinois’s Cook County, which includes Chicago.
REFERENCES
1. EPA document available here.
2. Because of the historical longevity of diesel engines, this is expected to take some time. The EPA estimates that some of the oldest engines and machines will have 20-40 times the emissions levels of a new Tier 4 engine.
3. Certain marine engines that are exempted from marine standards may be subject to off-road regulations.
4. Engines above 560 kW are not tested on the transient test; nor are constant-speed, variable-load engines of any power category.
5. Source: here.
6. Ibid
7. Click here.
8. For specifics, visit here.
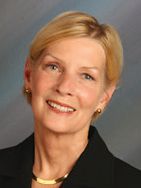
Jean Van Rensselar heads her own communication/public relations firm, Smart PR Communications, in Naperville, Ill. You can reach her at jean@smartprcommunications.com.