Efficient hydraulic fluids
R. David Whitby | TLT Worldwide January 2011
Compressibility is still one of the most critically important factors.
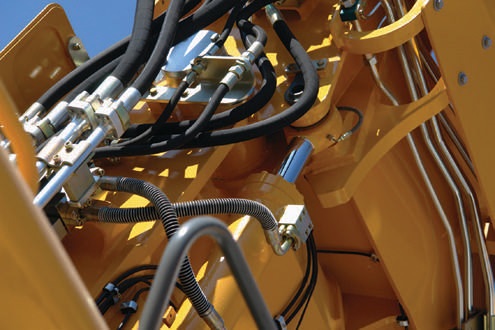
The size and weight of a hydraulic system is critical when the importance of a low bulk modulus becomes greater.
www.canstockphoto.com
Hydraulic fluids transmit power as a hydraulic system converts mechanical energy into fluid energy and subsequently to mechanical work. To achieve this conversion efficiently, hydraulic fluids need to be relatively incompressible. Hydraulic fluids must also minimize wear, reduce friction, provide cooling and prevent rust and corrosion, be compatible with system components and help keep the system free of deposits.
Compressibility measures the relative change in volume of a fluid or solid as a response to a change in pressure and is the reciprocal of the volume-elastic modulus or bulk modulus of elasticity. Bulk modulus defines the pressure increase needed to cause a given relative decrease in volume.
The bulk modulus of a fluid is nonlinear. When the change in volume against pressure is plotted on a graph, the result is a curve rather than a straight line. Tangent bulk modulus relates to the slope of the curve at any specific point and is, therefore, the true rate of change in volume at that specific pressure.
Bulk modulus is further defined as isothermal, where the heat associated with compression is dissipated (constant temperature) or isentropic. When the heat associated with compression is not dissipated, both pressure and thermal expansion are considered. Isentropic can be viewed as dynamic bulk modulus and isothermal as static bulk modulus. The former is typically appropriate to modern, high-response hydraulic systems.
Hydraulic fluids need to have a very low compressibility. A low compressibility translates into a fast response time, resulting in a high-transmission velocity of pressure and low power loss. Hydraulic fluids with a high compressibility or low bulk modulus act as dampening fluids. As a result, hydraulic fluids that contain entrained air, due either to poor air release or excessive foaming, are much less effective in transmitting power.
The size and weight of a hydraulic system is critical when the importance of a low bulk modulus becomes greater. Poor compressibility requires increased line sizes and actuator cross-sectional areas to compensate for the lower stiffness of the fluid. These increases also mean a larger volume of hydraulic fluid and greater hydraulic system weight.
Different hydraulic fluids have different compressibilities. For example, naphthenic oils have a higher bulk modulus than paraffinic oils. Water is slightly less compressible than mineral oil, while phosphate and vegetable-oil esters have compressibilities similar to that of water. Polyalphaolefins are more compressible than mineral oils. Water-glycol fluids are intermediate between mineral oils and water.
Mineral oils are relatively incompressible, but volume reductions can be approximately 0.5% for pressures ranging from 6,900 kPa (1,000 psi) up to 27,600 kPa (4,000 psi). Compressibility increases with pressure and temperature and has significant effects on high-pressure fluid systems. Hydraulic oils typically contain 6% to 10% of dissolved air, which has no measurable effect on bulk modulus provided it stays in solution.
Bulk modulus is an inherent property of the hydraulic fluid and, therefore, is an inherent inefficiency of the hydraulic system. Because compression of the fluid requires energy at the input, which cannot be converted to useful work at the output, it is lost energy. The larger the system actuator and the faster the required response time, the higher the energy inefficiency due to bulk modulus.
There are hydraulic system problems caused by low compressibility, including:
•
Servo-valves fail to maintain static rigidity and experience adverse effects in system amplification.
•
Loss in efficiency because volume reduction due to compressibility cannot be recovered.
•
Cavitation, which may cause metal fracture, corrosive fatigue and stress corrosion.
It is normally desirable that compressibility should be as low as possible, although an extremely high resistance to compressibility in a hydraulic fluid could actually be disadvantageous in readily transmitting shock forces. However, the inherent elasticity of the mechanical components comprising hydraulic systems has the effect of increasing the absolute compressibility of the fluid to a rather higher apparent value.
David Whitby is chief executive of Pathmaster Marketing Ltd. in Surrey, England. You can reach him at pathmaster@dial.pipex.com.