What was the stupidest thing you ever heard anyone say about lubrication?
TLT Sounding Board January 2011
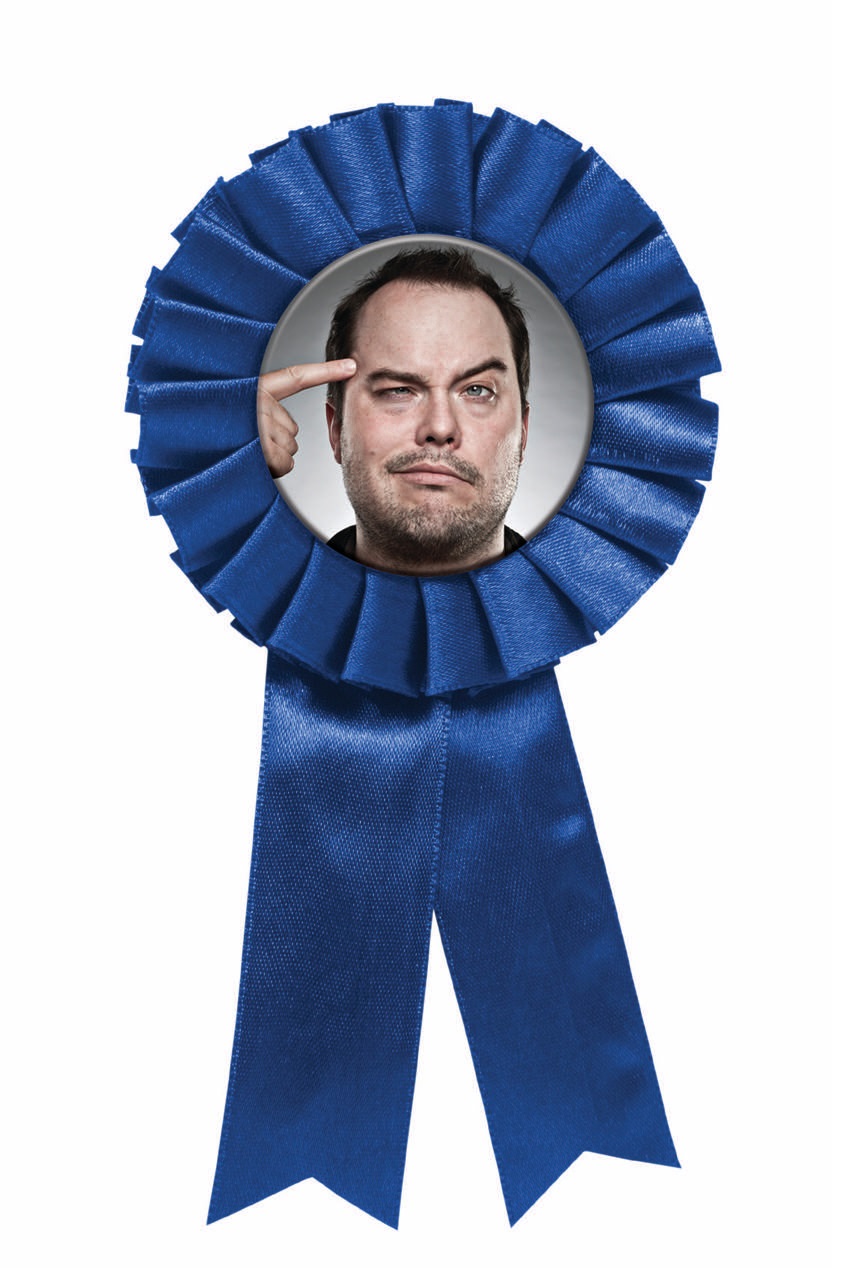
www.canstockphoto.com
Trying to judge which of our reader-submitted comments wins the blue ribbon for foolishness is a daunting task. Is it the mildly amusing “I know how good the oil is by feeling it” or the truly frightening “Changing oil is unnecessary and was devised by oil companies to get rich?” While STLE members have spent lifetimes advocating for safe, effective and environmentally protective lubrication practices, a frightening lack of knowledge is still far too prevalent in many plants and facilities. The comments that follow are a lubrication engineer’s nightmare and a literal recipe for disaster—and it gets worse. Next month our readers reveal the most uninformed and potentially dangerous lubrication practices they’ve observed in workplaces around the world.
“Oil is oil, it doesn’t matter what I put in, as long as there is enough.” Said by the head mechanic at a large metropolitan bus fleet after there were six engine failures in a month.
“The only oil analysis test that one needs is viscosity, because that will tell you whether or not the oil is good or bad.”
“I never liked this newfangled synthetic oil to begin with. I’d much rather stay with my old, reliable mineral oil-based product!”
“Every night I extract part of my MWF from sump and add water to replenish sump volume.”
“Oil’s cheap,” meaning they assumed that changing oil upon learning of an abnormal finding in an oil analysis would help or completely resolve the problem, regardless of its nature.
“There is no real difference in product technology.”
“The heavier the oil, the better lubricant it is.”
“We have been using the cheap stuff (AW 32) and we were having problems, so we moved to the premium oil (AW 68).”
“The more grease the better.”
“We can’t shut the line down to fix that right now” or “it can wait.” Result: Breakdown that caused the lines to be down anyway.
“You mean water-contaminated oil is bad for machinery lubrication?”
“It is impossible to improve maintenance costs without spending a lot of money we don’t have.”
“You don’t need a filter!”
“Lubrication is not necessary in machining operations.” True but only in limited applications and the HSE risks of atomizing machined metal is dangerous.
“Oil? You never have to change it.”
“All lubricants are the same and they can be mixed in the machine as long as they are of the same viscosity.”
“I change my motor oil when the oil pressure light goes on.”
Hearing someone refer to an oil by the micron rating of the filter when it was filtered: “I need a 25-micron oil.”
“They wouldn’t sell it if it wasn’t good enough.”
“If properly maintained, a coolant system never needs to be recharged.” This was the claim of one of our customers when tooling problems started in a line that had been using the same charge of coolant for more than nine years.
“We don’t service them until they break. If it ain’t broke, don’t fix it.”
“Oil is oil, grease is grease. If you change it often enough or grease it often enough, you will never have a lubrication failure.”
“As long as a machine has some oil, it will carry on working.”
“Oil never goes bad, that’s just a myth. Change the filter every now and then and it will last forever.” (Spoken by a decision-making person speaking of our rolling stock and diesel pumps.)
“It’ll be OK, the filters will catch it.” I hear that statement all the time and I cringe.
“Why buy a more expensive one? All lubricants are the same.”
“The viscosity of engine oil is a measure of its effectiveness. The more viscous the better.”
I was speaking to a maintenance supervisor about using one of our fire-resistant hydraulic fluids in a die-casting operation. His comment was that Fr fluids are too costly and a waste of money, because using them didn’t matter since the surface temperatures were so hot that anything would combust! The unbelievable part is that he was horribly disfigured facially and on his hands, including missing fingers, due to a plant fire!
“How dangerous is this stuff? Will we have to do any special air quality monitoring?”
While lubricating bearings in a 250-hp, overhung 2,000-rpm blower with a 72-inch wheel, a tech was asked how much and what kind of grease was being administered. His answer: “Does it matter?” Yes, he was serious.
“Never change the lubricant, just keep adding product or mix product.”
“Bearing clearance is 6 mil, so why are you worried about filters?” From a maintenance manager.
“All lubricants are interchangeable and contain the same stuff-the only difference is price.”
“As long as the bearings have oil in them, the compressor should run!”
The stupidest thing I have ever seen was the two-finger grease test. I was presenting a grease to use in electric motor bearings. The customer put a dab between his index fingers and pulled them apart. He then exclaimed that this “Grease was too thin, it’s not as thick as the red stuff we use.” They are still losing motor bearings to this day.
“I won’t use anything but red grease.”
“It’s more reliable to lubricate manually than by installing an automatic lubrication system.”
“It’s easy, anyone can do it and use anything.”
It amuses me to see people put their fingers into oil, rub their fingers together and say, “It doesn’t feel dirty.”
“One type of lubricant for all types of application.”
“If I can’t see the grease, it wasn’t done.”
“I’ll save money by using the cheapest oil I can find.”
Salesman quote: “Just dilute it further. It will be fine.” In reference to using a highly sulfurized coolant on brass.
“I change the oil often enough, so I don’t care much about the quality.”
“As long as it is running, don’t worry about it.”
General attitude I have observed in 30 years: “We’ll change lubricants, practices or maintenance procedures when it breaks.”
“We don’t worry about preventive maintenance.”
“In the choice of oil viscosity, environmental conditions plays no part.”
Editor’s Note: Sounding Board is based on an e-mail survey of 13,000 TLT readers. Views expressed are those of the respondents and do not reflect the opinions of the Society of Tribologists and Lubrication Engineers. STLE does not vouch for the technical accuracy of opinions expressed in Sounding Board, nor does inclusion of a comment represent an endorsement of the technology by STLE.