Oil analysis in the real world: Part VII
Jack Poley | TLT On Condition Monitoring January 2011
Clean oil thoroughly to prevent hydraulic system failures.
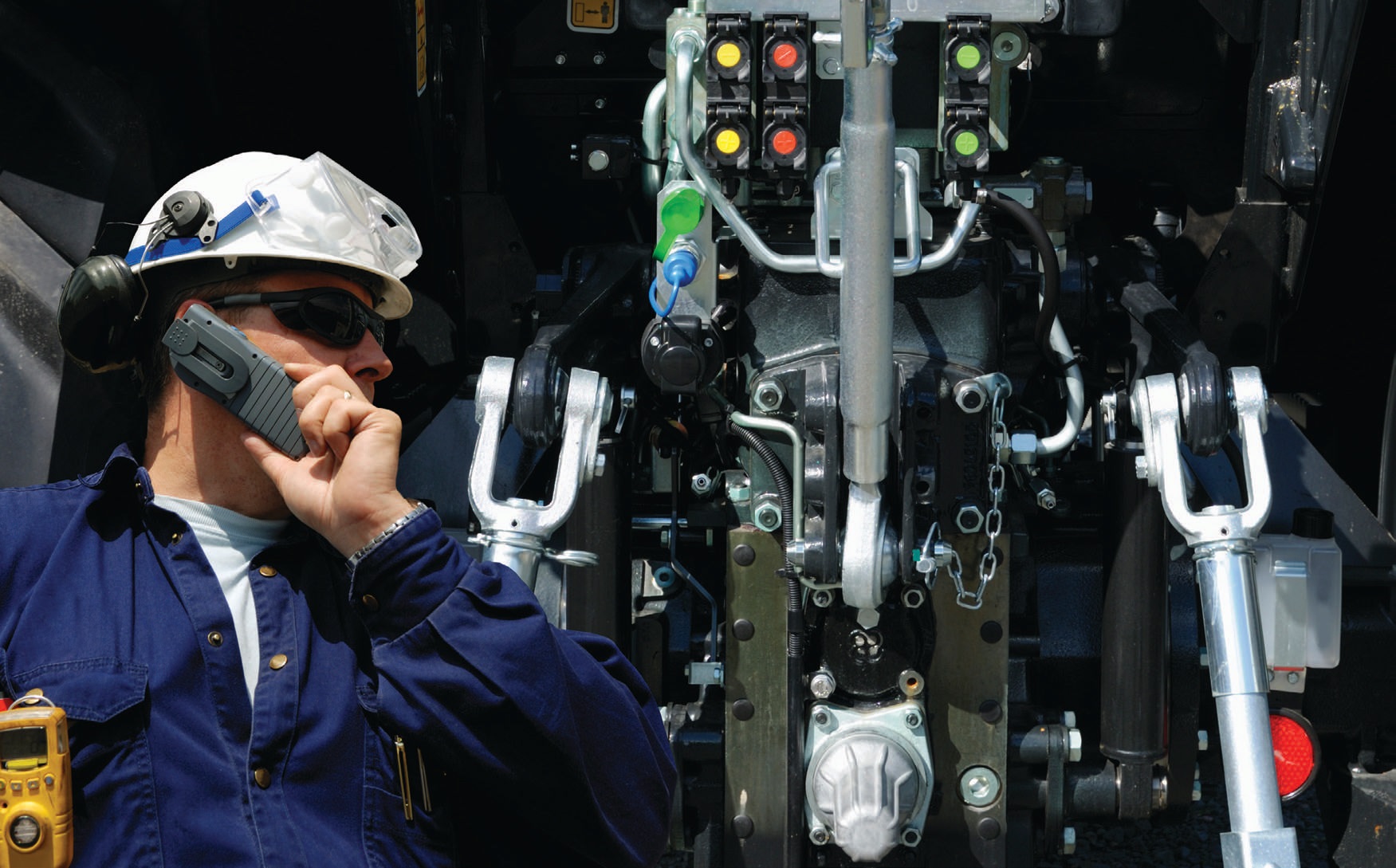
www.canstockphoto.com
Hydraulic systems are arguably the most sensitive of all oil-wetted systems in terms of the necessity for good contamination control. Unlike gearsets, which frequently operate without benefit of online filtration, hydraulic systems virtually depend on sufficiently clean lubricants to perform properly.
CLEANLINESS OF HYDRAULIC SYSTEMS
The reason cleanliness is so important is because clearances for moving parts (spools, cylinder rods, axial pistons, etc.) are at ten-thousandths of an inch tolerances. Particles entering such clearances can wreak havoc and quickly render a system unable to function properly, posing both production loss and safety hazard possibilities.
In contrast to most gearsets, hydraulic systems feature the most sophisticated filtration found on a multicomponent machine such as an earth-moving machine. In a plant, the component might be a stamping or molding machine.
The cleanliness of a hydraulic or similar system, in oil analysis terms, is measured via the lube’s particle count (PC). The de facto PC analysis features results at six particle diameter size ranges: 4μ, 6μ, 14μ, 21μ, 38μ and 70μ. Figure 1 is a typical table covering industry-standard cleanliness ranges and terminology based on ISO 4406 (1999). This table applies to all six ranges but is referenced primarily for the three smaller particle chord (diameter) sizes of 4μ, 6μ and 14μ, respectively. The ISO Cleanliness Code consists of three numbers corresponding to the particles concentrations for those three sizes, as shown below:
Figure 1. ISO Cleanliness Code Table
Following are some recommended test considerations:
Particle Counting. In a previous column, we covered PC to a reasonable extent, but it bears special mention and emphasis with reference to hydraulics. While I’m usually quick to recommend spectrometric metals analysis (SP) as the primary or key test in a suite of tests for most component types, I would choose PC over SP when a sophisticated hydraulic system (i.e., axial-piston pump or radial-piston pump) is being monitored. This is because I would expect contamination to
precede abnormal wear more often than not in such systems and thus would want as much early warning as possible. In a simple gear hydraulic system, I would consider SP and PC equals as first-call tests, but I would defer to anyone having more specific information in a given situation. Of course, this debate should stay at the hypothetical level because one should be employing both tests routinely for all hydraulic systems.
Summing up the efficacy of PC testing for hydraulic systems, dirty oil is considered to be the primary cause of hydraulic system failures, whether the failure is valve malfunction/sticking or excessive abrasive wear and subsequent fatigue or loss of function. PC testing is, therefore, imperative for maximum life and value of the machine.
Metals analysis, particular for wear elements, is obviously a means of assessing damage more specifically (PC does not identify the compositional aspect of particles, only that they exist in progressive size ranges). If the wear level or rate is sufficiently low (acceptable), it may be that flushing the system or using offline filtration (sometimes called portable or kidney filtration) can rid the lube of excessive particles, mitigating the abnormal amounts of metal, thereafter.
If one is able to achieve that effect, the essential parallel piece of maintenance to perform is to determine the mechanism by which the particles got into the system and make necessary repairs or adjustments to prevent recurrence. In assessing contamination scenarios, SP and PC at times can work together:
•
If high Si is shown in SP results, the preponderance of excessive particles should probably be suspected to be abrasives, dirt, sand, etc. Oil handling and storage should be on the list of considerations as to cause along with compromised filters and breathers and, where applicable, sealing gaskets. Be thorough.
•
If low Si is shown in SP, this unfortunately does not rule out abrasives, as 3ì-5ì particles and greater are not readily detected by SP with consistency. Such particles can cause untold wear damage as they are able to pass into critical clearances. While being wary of abrasives, one must also consider the possibility of Si-based gaskets and o-rings contributing particles as they are compromised and crumble.
Finally when reviewing a PC result, there is no standard for the three larger particle sizes routinely determined in a PC. It is important to treat excessive amounts (as statistically determined) with some degree of importance. Most of the time, particularly when the ISO Cleanliness Level is reasonable, larger particles represent contamination induced by carelessness, e.g., unclean transfer vessels and piping, open drums of fresh oil and similar events.
It is also good practice to inspect newly delivered oils for excessive particulates, as there is no guarantee (unless it’s by contract with the vendor) that a specific cleanliness level exists at delivery. For this reason, many operations routinely test stored oils for particulates prior to placing them into service.
I hope one has enough input herein to fully appreciate the necessity of employing particle counting for hydraulic systems and the oil placed therein. Hydraulics are the exceptions that justify PC as the key test, even over SP. To reiterate, however, both tests are truly essential.
FDMPLUS, PQ or DRF Analysis (Ferrous Debris Inspection). Some would contend this is overkill if one is monitoring PC, backed by SP. That argument is sustainable in a number of situations, but it must be recalled that because PC is able to inspect for particle sizes beyond that of SP there is a gap in vetting such particles effectively—that is, one cannot be sure if the particles are predominantly wear or simply contamination, which is an important differentiation.
Such ferrous debris inspection instruments cover the gap left by SP and, while only addressing Fe (iron) particles they are addressing the primary wear metal in virtually any system, including a hydraulic circuit.
I offer a compromise position on considering ferrous debris inspection routinely, not only for hydraulic systems but any system of value. If the component is situated in a remote venue that cannot be readily visited at will (e.g., unattended pipeline stations, offshore drilling units, wind turbines remotely sited, etc.), this type of scenario justifies the added testing support in order to be able to make a decision quickly.
Now if sensors are employed as well, such instruments are sufficiently small and inexpensive enough to be placed on site for exceptional insight immediately after a sample has been secured out of turn based on a sensor warning. In some instances, this will result in failure prevention. Final assessment or justification can be made by performing a proper reliability Centered Maintenance (RCM) study.
Water. In my opinion, the obsession with determining water concentration is unjustified, particularly when it comes to significant figures in the reported values. If water content needs to be precisely known, I would recommend utilizing an online sensor.
Regardless it is surely useful to assess that water is or isn’t in the system and, if so, to deal with it since hydraulic systems do not operate well in an aqueous-infested environment. Karl Fischer is the standard for water monitoring of hydraulic systems. I admonish, per usual: Be clever and consistent about securing the sample and be diligent about securing reasonably valid aliquots for testing in the laboratory. Following those two advisories, one should know if water is present or not and, if so, whether the concentration is small, medium or large. If the amount is relatively small (<500 ppm), there may be some technical fix to perform. If it’s 1,000 ppm, there may be both technical and human error issues. If it’s >5,000 ppm, the sample may be unrepresentative or oil handling and care-taking is wanting. (All of this with the assumption that the laboratory has taken its proper precautions to get as representative a test sample as possible).
Fourier Transform Infrared Spectroscopy. FTIR has value in terms of its practical application involving gearsets. However, FTIR is probably not as great a player in hydraulic system lubes as it is in gearsets or engines, mostly because one rarely sees abnormal oxidation values (against reference).
Acid number (TAN). As with gearsets, the recommendation is much the same. If one finds little or no movement in the test data over time, it may well be unnecessary. Probably the best approach is to extract the AN from FTIR, if available, rather than incur the expense of an added test setup. Not withstanding FTIR, ASTM D664 is the recommended formal method.
Viscosity. Automatic.
We have enough tests to propose the following test suite for a hydraulic system:
•
Particle Count: The key test for hydraulics, hopefully identifying contamination before it can cause wear or other trauma.
•
Spectrometric metals: Mandatory and to assist in vetting the PC results.
•
Ferrous Debris Monitoring (fdMplus, PQ, DRF): Consider the remoteness of the machine and its RCM importance (rating) to one’s operation.
•
Viscosity (usually 40 C): Mandatory.
•
Water (Karl Fischer preferred vs. Crackle, FTIR, etc.): One should always know if water’s there, so do something. Choose the method and testing sequence, if any, based on asset criticality and sensitivity to water.
•
Oxidation (FTIR): Usually via FTIR for mineral lubes. If AN is achievable, as well, it is a welcome addition. Water screening can also be satisfied properly.
•
AN (ASTM D664 or FTIR): May be optional. If available free from FTIR, that’s plenty good enough.
•
Micropatch or Analytical Ferrography: Invoked as appropriate for decision-making as to a teardown for wear or other trauma inspection, when above tests, local diagnostics and observation indicate accordingly.
Jack Poley is managing partner of Condition Monitoring International (CMI), Miami, consultants in fluid analysis. You can reach him at jpoley@conditionmonitoringintl.com.
For more information about CMI, visit www.conditionmonitoringintl.com.