Riding the wind
Peter A. Oglevie | TLT Shop Floor October 2010
Sailboats and wind turbines have a lot in common when it comes to condition monitoring practices.
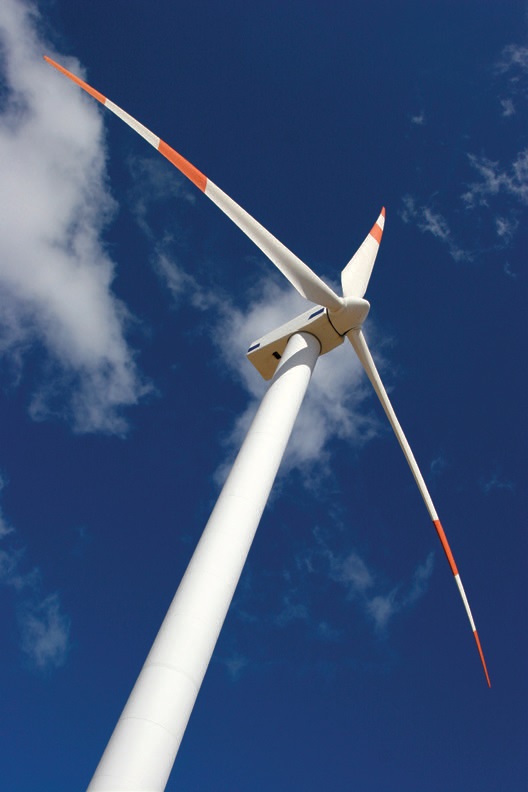
A good condition monitoring program can reduce the projected $100,000 lifetime expense of a wind turbine.
www.canstockphoto.com
My sailing schedule is winding down. We recently ran our last big race series of the year and finished back in the fleet.
Our problem was equipment failure. We snapped both of our Kevlar jib halyards. The first halyard snapped a minute into the first race, and the second failed at the midway point of the second race. These failures point out the power of Mother Nature and the need to monitor her effects on equipment.
The world is in a big race of its own—to develop more renewable energy sources. That means the shop floor is moving onto fields, seas and oceans in the form of wind turbines. Like our sailboat, these turbines rely on wind. The wind, however, presents a problem—it is highly variable. One day it blows at 10 knots, the next day 25 knots. The loads created are not equal, and the strain on the equipment varies.
On a sailboat, we adjust the sails. On a wind turbine, wind produces lift to drive the blades and turn the shaft that drives the turbine. As wind speed increases, so does the torque in the gearbox. Onboard sensors rotate the blades to reduce the lift and torque. A governor holds rotation to a maximum speed and shuts down the turbine in excessive winds. The major wear points are the gearbox and the governor.
The shop floor for this gearbox and governor is up to 300 feet off the ground, most likely out in the middle of a field or even on the high seas. It is out in the elements exposed to temperature and precipitation. How do we take care of it?
The answer is condition monitoring. We cannot change Mother Nature and magically make the wind steady. We might slow down the infiltration of dirt and moisture into the gearbox reservoirs, but we can’t stop it, and we certainly cannot control the temperature. Therefore, we have to monitor the gearbox fluid to determine change intervals or filtration needs. Since we cannot control the wind, the best we can do is adjust our sails or blade to minimize its effect on our equipment.
Considering the points above, we have to climb the towers. At 200 to 300 feet high, this will be a young technician’s job. An old guy like me would most likely have a heart attack. In the future, onboard lifts will make repair and replacement less strenuous.
Once we have our shop floor monitored and the fluid conditions known, we can work on our key goals—reducing wear, predicting failures before they occur and eliminating unscheduled downtime. Unscheduled downtime is exacerbated by the remoteness of the wind turbine and the need for cranes to make the repairs. I’ve read it can take up to three months to schedule the crane, during which time the wind turbine produces no power, adding to a lifetime expense that can exceed $100,000. A well thought out condition monitoring program can eliminate much of this expense and add to the bottom line of the wind generator.
We cannot control Mother Nature. During our last series of sailboat races we snapped two Kevlar halyards at the top of the mast. Root cause—the sun degraded the halyards over their seven-year life. As the lightest member of the crew, I see a trip to the top of the mast in my future to replace the lines. We will either shield the line from the sun or replace them on a six-year interval.
We were disappointed to lose our race, but no one got hurt and we finished the races with our spinnaker halyards. Now is a good time for people involved in the wind industry to think about how they can use better condition monitoring practices to finish their big race.
Pete Oglevie is president of International Production Technologies in Port Washington, Wis. You can reach him at poglevie@wi.rr.com.