Rolling resistance of tires
R. David Whitby | TLT Worldwide September 2010
Manufacturers are looking to develop products that are more fuel efficient, higher performing and eco-friendly.
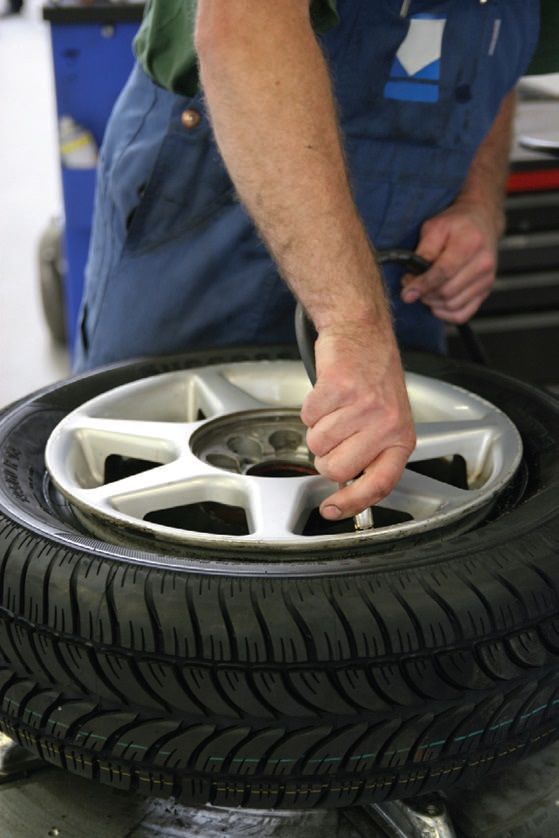
Process oils are used in manufacturing tires to give them good stiffness and processability.
www.canstockphoto.com
In May I wrote about static, kinetic and rolling friction and the problems that exist with driving on snow and ice. Now let’s discuss the rolling resistance of tires.
When a body rolls on a surface, the force resisting the motion is called rolling resistance or rolling friction. Less force is required to roll an object than to slide or drag it, but a small amount of friction must be involved because force is required to maintain rolling motion.
A rolling cylinder ideally will make contact with a flat surface along a line. In reality, the area of contact is slightly larger than a point or line due to elastic deformation of either the rolling object or the flat surface or both. Much of the friction is attributed to elastic hysteresis, a characteristic of a deformable material in which the energy of deformation is greater than the energy of recovery.
The rubber in a tire exhibits hysteresis due to its viscoelastic characteristics. A rotating tire experiences repeated cycles of deformation and recovery as it grips the road. It dissipates the hysteresis energy loss as heat. Hysteresis is the main cause of energy loss associated with rolling resistance.
The rolling resistance of tires may differ greatly. A 40% difference in rolling resistance is equal to a 6% difference in fuel consumption. Tire manufacturer Michelin has found that 20% of the energy in gasoline goes into overcoming rolling resistance. The amount of energy caused by deformation can be regulated with structural and material choices in tire design. Factors that increase energy consumption include tire temperature, pressure, load index and wear, as well as air resistance and turbulence, depending on the driving speed.
Vehicle manufacturers are emphasizing the development of more fuel-efficient, higher-performing, eco-friendly tires. Getting the best fuel efficiency while ensuring that tire traction keeps the vehicle on the road is important, particularly when going around corners. Better brakes mean larger diameter rims for tires, so the traction demand on tires is greater. As the power and torque of engines increase, the demands on tire handling also increase.
A German chemical manufacturer suggests many tires are underinflated, which wastes energy and increases the risk of tire failure. Only a properly inflated tire offers advances in tread and sidewall materials through control of hysteresis while driving. Tire pressure monitoring systems are already enforced by law in the U.S. These devices warn the driver when tire pressure falls below a defined threshold.
A first line of defense, now standard in all modern tires, is a layer of halo-butyl rubber that coats the inside of the tire and helps prevent air leakage. Researchers are looking for ways to make this layer even less permeable.
Tire manufacturers also are experimenting with built-in electronic chips to measure air pressure, temperature, traction and footprint deformation. This data is fed into the car’s driving control system to adjust speed, brake and steering response. These chips also can be used to obtain the tire’s track record to support their maintenance.
Process oils are used in manufacturing tires to give them good stiffness and processability. Rubber and tire manufacturers are now evaluating various alternative process oils, including mild extraction solvates and non-labelled aromatic extracts, to identify those that provide the best combinations of rolling resistance, low wear, good dry and wet grip and fuel economy for tires.
There is more to rolling resistance of tires than simply measuring coefficients of rolling friction.
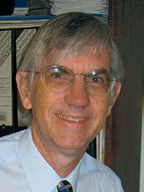
David Whitby is chief executive of Pathmaster Marketing Ltd. in Surrey, England. You can reach him at
pathmaster@dial.pipex.com.