The whole package
Peter Drechsler | TLT President's Report September 2010
Today’s additive manufacturers can solve just about any problem—except inventing a fountain of youth.
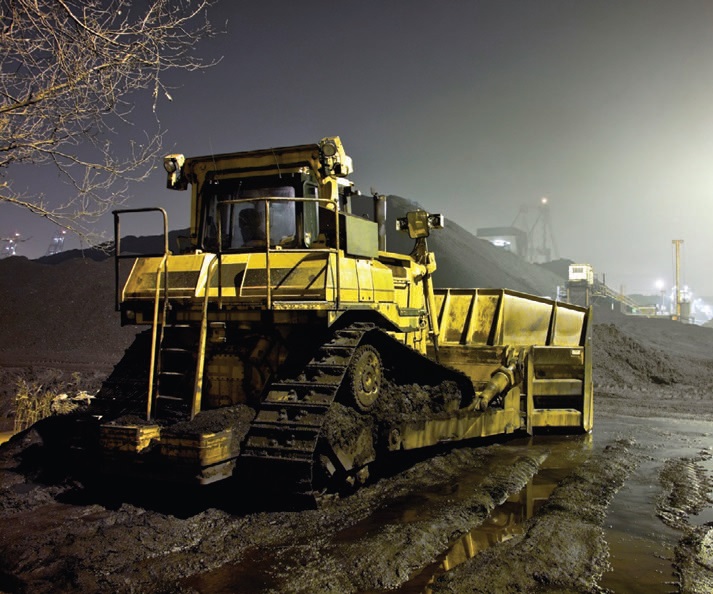
The right additive chemistry and concentration often are the keys to success when dealing with machine lubrication problems.
www.canstockphoto.com
Additive chemistry plays an important role in many of the products we use today, including engine oils, greases, lubricating oils for machinery, bearing and gear lubrication and so forth. Additives can be benign or active constituents in the product formulation. Certain additives are used as fillers or to impart a pleasing color or odor to the end product, but most play an important role in enhancing the performance aspects of the end product. These additives address specific needs such as foam, wear, fretting, corrosion, viscosity modification, detergency and oxidation.
One of the first cases I was involved in reminded me of the importance of additive chemistry. Very early in my career I was called out to the shop floor to investigate an issue on one of the machining operations. Operators had noticed that the rubber gaskets and bellows on their honing machines were deteriorating.
The fluid they were using for the honing operations had been in service for around a year, although they did not see this problem in the past. A large central system supplied the honing oil to these machines. The operators suspected that someone had added the wrong product to the system when make-up oil was needed.
Samples were taken from the central system as well as virgin samples from new stock, and the analysis began. Yes, we did see some differences in the fluid from the central system as compared to the virgin stock material, but they appeared to be minor and more of a shift in chemistry. While I can’t remember all of the details (this happened more than 25 years ago), the base fluid which was comprised of mixed esters was now exhibiting what appeared to be free fatty acid constituents.
The details are still a little fuzzy, but I do recall working with the vendor to determine what was causing the degradation of the rubber components. Through more analysis, we determined that the antioxidant package was being depleted which, in turn, caused the oil to break down, thus forming the free fatty acids and triglycerides that were attacking the rubber components.
Apparently the amount of antioxidant in the make-up oil we were adding to the central system was not enough to replenish the antioxidants that were being depleted. The solution was to boost the level of the antioxidant in the base product to account for the rate of depletion.
This was a successful remedy, and when the system was dumped and recharged with the new formulation containing the enhanced antioxidant package, we never saw the return of this problem. Using the right additive chemistry and the proper concentration was the key to success in solving this problem.
Moral? While additive packages are something that might avoid the notice of machine operators, we in the lubricants industry must never overlook these chemistries when searching for answers to shop floor problems.
In this issue TLT contributing editor Neil Canter shows how STLE-member additive manufacturers are dealing with problems relating to the new GF-5 standard in the auto industry. Increasing fuel economy while maintaining engine cleanliness poses unique challenges from an additive formulator’s point of view, but I have no doubt our industry will rise to the technical occasion, as it always does.
Now if we could only create an antioxidant to keep us from aging and our memories intact.
Peter Drechsler is a senior tribology specialist with The Timken Co. In Canton, Ohio. You can reach him at peter.drechsler@timken.com.