Please describe your greatest challenge working with surface engineering techniques, including coatings, surface treatments and surface texturing. What was your solution?
TLT Sounding Board June 2010
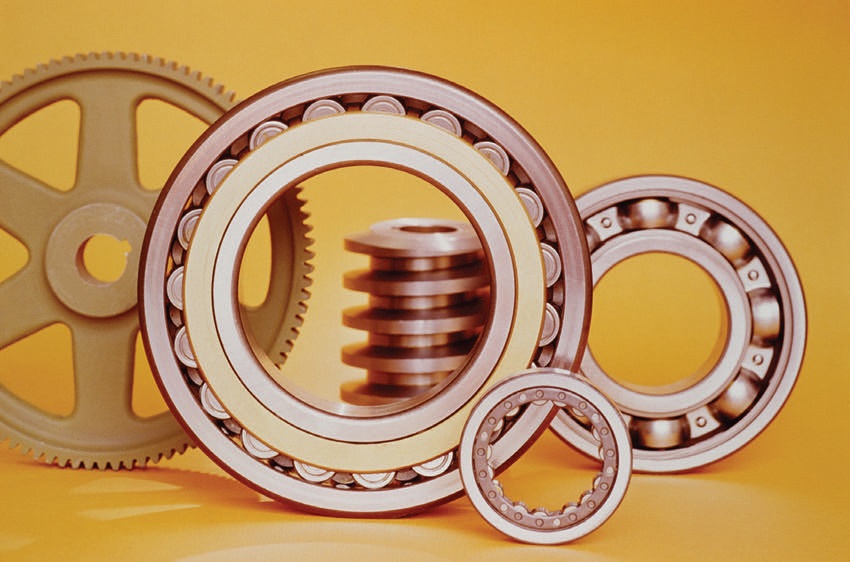
www.canstockphoto.com
While surface engineering techniques is one of the narrower areas of lubrication engineering, it nevertheless engages those who must deal with them on a regular basis. Readers were eager to share their most vexing problems. Some of them devised solutions while others are still searching. Asked about the most prevalent failure mechanism of coatings in their applications, wear was the No. 1 rated answer, earning 59% of survey responses.
Determining the optimum surface microgeometry for different machine elements. It would seem that a “smooth is best” syndrome prevails for most applications. I have not found a solution except for internal combustion engine cylinder liners, but I have a feeling that the plateau type surface would offer a wider range.
Getting the coatings to adhere to the surface. One thing that has helped is double checking to make sure that the surface is clean.
My challenge was to leave a protective film that still protects but is easy to clean off. I have yet to fix this.
A new technology for heavy-loaded machine components like gears employing PVD coatings.
The greatest challenge of my surface engineering research is surface treatment by plasma deposition. I use filtered cathodic vacuum arc deposition. The plasma is not always stable. The fluctuation of plasma intensity makes it difficult to control the uniformity and thickness of films. My solution is to apply certain magnetic coils around substrate to regulate the plasma flow.
Bond strength of thermal spray is a limiting factor. Replace by diffusion bonded or fused coatings.
New coatings or surface treatments would always raise doubts whether they are compatible with lubricating oils. This would be especially troublesome when water-based lubricants are used. The bench test results would often be marginal, and the real answer would only be given during the usage of the coating.
The greatest challenge was surface textures. Solution was improving treatment and polishing, getting CVD films to stay on.
Getting the coatings to adhere to the surface. One thing that has helped is double checking to make sure that the surface is clean.
Hardening and finishing.
Identifying simple processes that perform two functions in one step; that is, cleans a surface while simultaneously generating a texture that is most favorable for paint adhesion. Existing solution that is universally used is standard grit blast process. Optional method was recently developed using rotary wire blast tool (more widely known as bristle blaster).
Obtaining consistent results from batch to batch is vital, but a practical challenge is the cost and narrowing of options as laws and environmental regulations expand.
Consistent, repeatable quantification of benefits. Each application in tribology is unique, so it can be difficult to generalize the value of specific surface engineering technologies.
We are in the sealing business, so we want to reduce friction. We managed this by increasing the lubrication due to structuring of the surface.
Finding a proper laser technique for laser surface texturing.
Prevention of sliding wear in air/gas film bearings prior to lift off. Finish surface such that rms roughness < 10% minimum film thickness at operating condition. Use nitridable Nitroloy, hardened by heat treatment carefully controlled to avoid surface distortion.
For coating it is to get uniform thickness in one application at wall and floor. An application at wall will get thickness 150 micron whereas an application at floor will give 250 micron. So solution is to apply two times for wall coatings. For surface texturing it is to ensure recoat at coating surface already cured will bond cohesively. Solution is to blast but control the nozzle distance and angle so as not to peel off coating while still giving coating surface sufficient roughness.
Defining the correct microstructure for a coating that gives a “quality” final product. Solution is to run a number of design experiments to determine the optimum solution.
Rust prevention. Rust inhibitors.
Surface profilometry.
Compatibility with the neighboring elements in the system.
Making coatings stretch.
Among coatings, surface treatments and surface texturing techniques, which one is used the most in your application?
Coatings
43%
Surface treatments
21%
Surface texturing techniques
31%
Based on responses sent to some 7,000 TLT readers. Total exceeds 100% because many readers chose more than one answer.
Please describe a “perfect” bearing surface for your application.
8-12 micro inches.
One that has been properly honed for the particular application.
One that is very elastic.
There is nothing perfect. My imaginary perfect bearing surface is a surface of infinite rigidity (never deform), zero-friction with any other solid surface, atomic smooth surface and zero-transmission of heat and electricity.
The surface of proper material and strict roughness quality and proper surface free energy.
The perfect bearing surface is the one showing zero wear during the startup as well as under the normal operation regime. It must be strongly bound to the substrate, i.e. should not flake off, crack or experience any surface fatigue. It must not corrode or rust. It should be tolerant to dust, contaminants, water, heat, stress.
Good texture and perfect handling.
Smooth, hard, flake-off resistant.
There are so many variables in our food manufacturing plant that no one surface would be perfect for every application.
Smooth and flat.
We need a “coating-ready” surface; i.e., corrosion/contamination-free surface with non-biased, uniform coarse/granular texture.
Conformable yet extremely durable, resistant to abrasion by contaminants, corrosion resistant and compatible with inexpensive lubricants.
PTFE sealing for meters.
Hard yet elastic to accommodate surface deformation. Dissimilar to counter face for low friction and wear resistance. Excellent lubricant wet ability.
Ceramic diffusion skin with dry film lube and lube pockets.
Similar to an orange skin. Smooth with a plateau but with lots of small cavities to give a lubrication depot.
Partially textured surface as described in
Tribology Transactions, Vol. 43 (2003) pp. 397-403 and
Tribology Letters, Vol. 17 (2004) pp. 295-300.
Perfectly smooth.
Surface roughness minimum 75 micron and cleanliness minimum grey metal. This can give coating shear strength up to 4,000 psi.
What is the major failure mechanism of coatings in your application?
Wear
59%
Cracking
21%
Delamination
31%
Based on responses sent to some 7,000 TLT readers. Total exceeds 100% because many readers chose more than one answer.
Editor’s Note: Sounding Board is based on an e-mail survey of 13,000 TLT readers. Views expressed are those of the respondents and do not reflect the opinions of the Society of Tribologists and Lubrication Engineers. STLE does not vouch for the technical accuracy of opinions expressed in Sounding Board, nor does inclusion of a comment represent an endorsement of the technology by STLE.