A three-pipe problem
Evan Zabawski | TLT Lessons Learned June 2010
As Sherlock Holmes observed, when seeking an answer, look for more than is readily apparent.
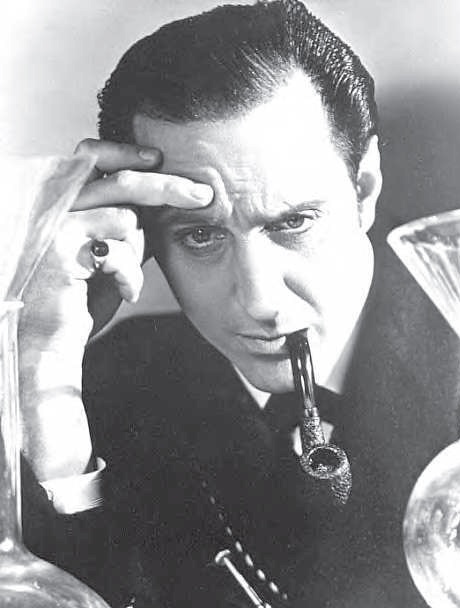
One day while working for a filter manufacturer, I received a phone call from a coal-fired power plant technician asking if I could help figure out a filtration problem. The problem affected an electro-hydraulic control (EHC) system on a power turbine, which just so happened to be our niche. The issue he described seemed so simple at first but turned into something requiring so much digging that Sherlock Holmes would refer to it as “a three-pipe problem.”
The details of the case were: a recent and known water leak into the hydraulic fluid was causing the duplex filtration system to plug-off filters at the rate of one set per day; normally these filters last around a year in service. Seeming so “elementary,” I quickly asked if the filters were cellulose or synthetic, as the cellulose, or paper, would soften in the presence of water and potentially collapse. He said they were synthetic; the answer was not that simple.
Figuring there was an excess of used filters, I asked him to submit a set to me for analysis. What I received was a ß1 1,000 filter and ß5 1,000 filter. As shown in Figures 1 and 2, each was covered in granular debris. I backwashed each filter using a solvent and filtered the wash onto membrane filters, which were submitted to a geological lab for X-Ray diffraction(XRD) analysis.
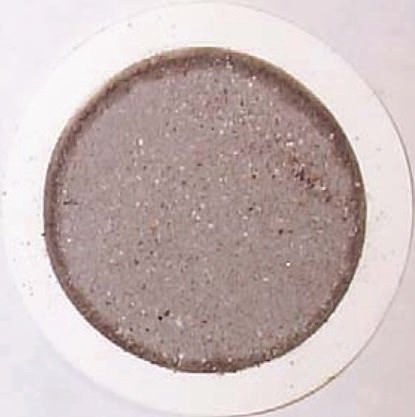
Figure 1. Debris from ß1 1,000 filter.
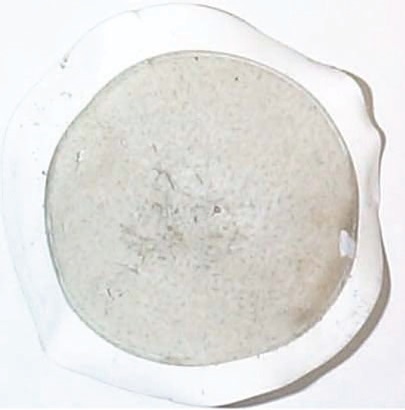
Figure 2. Debris from ß5 1,000 filter
XRD uses known wavelengths of x-rays, which are diffracted by the lattices of the crystals in the sample to give unique patterns of peaks of reflections. Consequently, only materials with a crystalline structure can be identified, namely minerals.
The results of the ß1 1,000 filter analysis suggested that the sample consisted of zinc compounds (zinc chlorate hydroxide and zinc hydrogen phosphate) with lesser amounts of silt/clay (quartz, plagioclase and kaolinite) and iron compounds (siderite and pyrite). Having no firm idea how this mixture came to be, I used my copy of The Merck Index and issued a report stating, “The two zinc compounds are not naturally occurring and are, therefore, products of some unknown interaction or reaction. Kaolinite is important to the production of ceramics and porcelain. Siderite is a form of iron and can be found in coal and shale. Pyrite (Fool’s Gold) is quite common and may be found in coal. Quartz is one of the most abundant minerals on earth, but one of its many uses is also in ceramics. Plagioclase is also used in the production of ceramics.”
The results of the ß5 1,000 filter analysis suggested that the sample consisted of iron compounds (metavoltine, magnetite and siderite) with lesser amounts of silt/clay (quartz and kaolinite), calcium sulfate (gypsum) and sulfur. These results were equally puzzling; the report was issued stating, “Metavoltine is found all over the world and has no specific use. Quartz is one of the most abundant minerals on earth, but one of its many uses is also in ceramics. Kaolinite is important to the production of ceramics and porcelain. Sulfur is commonly found in coal and other hydrocarbons. Gypsum is not only found in wallboards, it is used in some cements. Magnetite is used in coal-washing applications. Siderite is a form of iron and can be found in coal and shale.”
I struggled to find a correlation between the findings and a likely source; hence my emphasis on coal, but the ceramics link could not be avoided. When the customer received the report, he called me to discuss the findings. I quickly launched into an apology for not arriving at a definitive answer and reiterated the odd connection to ceramics, citing Holmes’ statement, “When you have eliminated the impossible, whatever remains, however improbable, must be the truth.” He then asked me if these compounds could come from Gunnite.
I said I did not know, since I didn’t even know what Gunnite was and it is not listed in The Merck Index. He offered his best explanation, which was to compare applying Gunnite on the inside of a boiler to applying cement on the walls of a swimming pool. The American Concrete Institute defines Gunnite as “mortar conveyed through a hose and pneumatically projected at high velocity onto a surface.”
A little research confirmed that many of the findings could indeed be attributed to Gunnite, but I still wasn’t sure how it came to be in the EHC system 50 feet away from the boiler. The customer explained that the boiler had been relined two years earlier and that the high velocity application of the product, using compressed air, did produce a lot of dust, which could have settled in the poorly protected EHC tank.
The real “a-ha” moment came when we concluded that this dust had sat dormant in the tank until it was disturbed by the presence of water from the cooler leak, forming cement-like deposits. So the water really did cause the filter plugging but only indirectly, due to events two years earlier. I felt just like Sherlock Holmes when he said, “Chance has put in our way a most singular and whimsical problem, and its solution is its own reward.”
The lesson learned is that thorough investigation usually involves expanding the scope to include more than is readily apparent. I was so intent on solving a problem with the EHC system that I did consider the rest of the plant’s effect. Now I have learned to keep my mind and eyes open. In fact, like Holmes, now, “I see no more than you, but I have trained myself to notice what I see.”
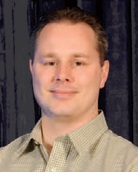
Evan Zabawski, CLS, is manager of training and education services for The Fluid Life Corp. in Edmonton, Alberta, Canada. You can reach him at evan@fluidlife.com.