20 Minutes With John M. Burke
Thomas T. Astrene, Publisher | TLT 20 Minutes June 2010
Leading an interdisciplinary team of scientists, this STLE and ILMA member helped develop a groundbreaking test method for measuring VOCs in metalworking fluids.
JOHN M. BURKE PROFILE
PROFESSIONAL EXPERIENCE
• Houghton International, Valley Forge, Pa., Director of Engineering Services, Worldwide, 2001-Present.
• Eaton Corp., Willoughby Hills, Ohio, Manager of Environmental Services, Worldwide, 1996-2001.
• Eaton Corp., Willoughby Hills, Ohio, Manager of Environmental Engineering, Worldwide, 1985-1986.
• Eaton Corp., Willoughby Hills, Ohio, Principal Engineer-Corporate Environmental Engineering, 1972-1985.
EDUCATION
• University of Dayton, Dayton, Ohio, Bachelor of Science in Engineering.
AWARDS AND HONORS
• STLE P.M. KU Award, 2006.
• Presidential Award for Waste Minimization, Received at the White House by then-President George W. Bush, 1991.
• Governors’ Award for Waste Minimization—Ohio.
• Governors’ Award for Waste Minimization—Tennessee.
PROFESSIONAL AFFILIATIONS
• STLE
• ILMA
PATENTS
• Five U.S. patents—Process type
• Three Canadian patents
• Two European patents
• Several process patents pending
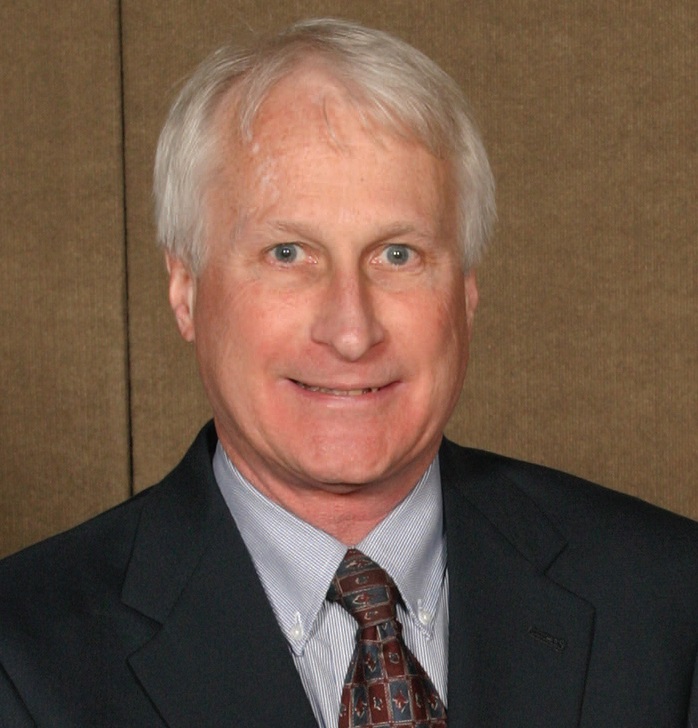
John M. Burke
TLT: How did you first become aware that the Southern California Air Quality Management District was looking into volatile organic compound content for MWFs and lubricants?
Burke: It all started in March of 2008. I received a call from Mike Pearce of the W.S. Dodge Oil Co. In Maywood, Calif. Mike called me directly because at that time I was the chairman of ILMA’s Safety Health Environmental and Regulatory Affairs committee. He started the conversion by saying, “Do you know what is going on out here with the South Coast Air Quality Management District (SCAQMD)?”
I admitted to Mike that I had no knowledge of their recent activities. He indicated that SCAQMD was attempting to use a complex analytical procedure using gas chromatography (GC) to quantify the volatile organic compounds (VOCs) in vanishing oils and rust inhibitors. Mike was worried that SCAQMD could regulate certain vanishing oils (which later in the regulatory process would include metalworking fluids) out of use in this area. He wanted support from ILMA in this rule-making activity.
For reference, a VOC is defined, per Wikipedia, as “organic chemical compounds that have high enough vapor pressures under normal conditions to significantly vaporize and enter the earth’s atmosphere.”
TLT: What is the concern regarding VOCs?
Burke: The issue on the table is that SCAQMD is under federal EPA order to reduce VOCs in the four-county area in the Los Angeles basin. VOCs are a contributory factor in the formation of photochemical smog. SCAQMD has moved through various industry segments with regulations, and now it is time for the regulation of the industry segment that uses vanishing oils, rust and corrosion inhibitors and MWFs.
TLT: How did you become involved?
Burke: Since I had worked on several rule-making activities before, and I had specific knowledge on MWFs, I volunteered to take the lead on behalf of ILMA when Mike made me aware of the situation.
TLT: What was the problem with measuring VOC content in MWFs?
Burke: There is no industry-wide accepted method for measurement of VOCs in lubricants or rust and corrosion inhibitors. Since MWFs are a subset of lubricants, no real measurement method applies to this group of chemicals. Some regulators have attempted to use EPA Method 24 to determine VOCs in lubricants. However, extensive testing by SCAQMD proved that Method 24 provides for too much variability to be used as a reliable enforcement tool for VOC measurement in MWFs.
Coincidently, EPA’s own Web site states that Method 24 should only be applied to coating and printing type sources. So here is the basic problem: We did not have a method to measure VOCs for lubricants and MWFs. SCAQMD had developed Method 313 and was in the process of adapting this method to measure VOCs in lubricants. They called this new Method 313L. When we first met with SCAQMD scientists and regulators, 313L was in the very early stages of development and not yet finalized. So we waited many months hoping that this method would work itself out. Mike Grippi at Quaker Chemical was very instrumental in pointing out concerns with Method 313L.
There is no industry-wide accepted method for measurement of VOCs in lubricants or rust and corrosion inhibitors.
www.canstockphoto.com
TLT: Why was another new method proposed?
Burke: Industry and SCAQMD were both running out of time. It was now the third quarter of 2009, and 313L was still not sorted out. Since MWFs would ultimately have a VOC regulatory limit, compound blenders of MWF and end-users of MWF had no idea what products would be allowed and which products would be restricted. This is simply because we had no way to determine the VOC content of these fluids.
TLT: How did you go about devising a new method?
Burke: We were fortunate that a senior research scientist at Houghton International, Robert Blithe, had extensive experience with an analytical technique referred to as thermogravimetric analysis (TGA). TGA is used in many areas of the chemical industry. One such area is to determine the volatility of oils in sensitive hydraulic systems such as military aircraft. Right away we seemed to have an analytical tool that could be adapted for use in our MWF area.
We proposed TGA as an analytical technique to the scientists at SCAQMD and initially received resistance because this method appeared similar to EPA 24. After much discussion, ILMA and SCAQMD agreed to further investigate TGA.
The first thing ILMA did was form a team of people with experience in TGA who also had the necessary instruments available. The next challenge, and possibly the biggest hurdle, was picking a time and temperature combination that would replicate real-world VOC conditions. Oddly enough, the determination of that time/temperature combination did not initially involve TGA but a more basic test.
Figure 1. Loss on drying 180-day study in progress for 4.4 cSt @ 40 C, 9.63 cSt @ 40 C and 20.5 cSt @ 40 C naphthenic oils.
TLT: So how did you go about creating a time/temperature combination?
Burke: After many meetings between ILMA and SCAQMD, we agreed that 40 C was the most likely highest average sump temperature for a MWF over a 24-hour, seven-day period. We chose three naphthenic base oils from a California refinery. They were a 4.4 cSt @ 40 C naphthenic oil, a 9.63 cSt @ 40 C naphthenic oil and a 20.5 cSt @ 40 C naphthenic oil.
We agreed to hold them in a lab oven for weeks, or even as long as months, until the weight loss stabilized. The weight loss stabilized at six months for the 9.63 and 20.5 cSt oils, so we stopped the test at that time. However, 4.4 cSt oil sample did not stabilize during that same period. From this six-month experiment, we could calculate a VOC weight loss expressed in grams/liter. We called this test the “gold standard” since this was our base line going forward. We also believed that this met a second real-world condition that a straight oil would be replaced twice a year or two turns per year.
Obviously we could not live with a six-month test for determination of VOCs in MWFs. So we measured the three base oils for 120 minutes at 71, 81, 91, 101 and 111 degrees C. We captured data every minute and plotted the data on a spreadsheet. Using a simple simulation program, 81 C at 110 minutes replicated the six-month study within +/-1%. We now had a time temperature combination we could live with.
TLT: So how did you arrive at the final method?
Burke: The ILMA team went back to SCAQMD and collectively agreed to follow ASTM E691 protocol for robustness and validation of this new method. STLE-member Dr. John Howell of Primagy Consultants was very instrumental in guiding us through the ASTM process. For robustness testing, we chose six ILMA-member laboratories and sent blind samples of the three base oils for weight loss by drying at 81 C at 110 minutes. Before the robustness tests were conducted, we mutually agreed on pass/fail criteria. In summary, the robustness testing indicated that we had a method that could be replicated by other laboratories with a high degree of accuracy. We were now ready to move toward a full ASTM Method.
Figure 2. 180-day study before and after comparative results for loss on drying 20.5 cSt @ 40 C naphthenic oil.
Working through the ASTM process, we started with ASTM Method 1868-09. From the information we gained from the previous tests, we were now ready to move toward validation following ASTM protocols.
For the ASTM validation process, we chose five MWF products: solvent cut-back straight rust preventative, ISO 22 hydraulic oil, ISO 22 sulfur chlorinated fatty straight oil, semisynthetic MWF diluted for use and an ISO 4 fatty straight oil. The validation test process via an inter-laboratory study proved successful. Now we are just working out the final details with the ASTM committee. The new method will be referred to as ASTM 1868-10. Water in straight oil samples and concentrate MWFs will be determined by Karl Fischer titration. The water content will then be subtracted from calculations.
Figure 3. A thermogravimetric analysis (TGA) instrument is used in many areas of the chemistry industry. One such area is to determine the volatility of oils in sensitive hydraulic systems such as military aircraft.
TLT: What is the current status of the project? What is the next step?
Burke: We have completed all robustness and validation testing. We expect an approval vote from ASTM at any moment—it might have come by the time you read this. SCAQMD has planned to formally adopt this method into Rule 1144 after their board approval this month. If the board does approve this method into the rule, then ASTM 1868-10 will be the test method used for enforcement for their Rule 1144 that regulates VOCs in MWFs, vanishing oils and rust inhibitors.
The next big step will be to get word of this test method out to industry and regulators outside the California area. We believe this method likely will be adopted by other cities or non-attainment counties as a method to regulate VOCs from MWFs. Working with STLE will be a key aspect in communicating this new test method and describing how it is applied.
Figure 4. Close-up of a TGA instrument weighing hook in a pan.
TLT: What are other challenges looking forward?
Burke: We are now entering into a new era of MWFs. For years we had focused on microbial controls, fluid optimization with chemical management programs, wastewater treatment issues and mist reduction. We now also will be looking at low-vapor-pressure MWFs as an extra parameter for fluid selection. This will involve such variables such as naphthenic vs. paraffinic basestocks, synthetic basestocks, vegetable lubricants, viscosity selection and low-vapor-pressure additives inclusive of antimicrobial compounds.
TLT: What does this mean for those who work with or manage MWFs and other lubricants affected by the new standard?
Burke: I believe there will be a lot of questions and concerns regarding VOCs in MWFs. We never really had in-depth discussions on VOCs in MWFs since we did not have a test method to identify and quantify VOCs—now we do. The test method is relatively easy to explain, but the TGA instruments are not in use at all at compound blenders. At first few end-users will have access to these TGA instruments. Gathering meaningful data will be slow until the instruments become more readily available.
Education will be the key, as it is with any change. STLE’s education program will have to add new course content for compound blenders, end-users and regulators on how each group will be impacted. Local STLE chapters also are a good resource to disseminate this information.
TLT: What did working on this project mean for you personally?
Burke: The key takeaway for me was the privilege of working with highly skilled individuals in a team environment and seeing the teams work through the various issues. We had challenges on many fronts, including legal, technical, administrative and even a small amount of lobbying to push our efforts forward. This team approach really paid off because we could not have done this as a group of individuals in this short period of time.
www.canstockphoto.com
I certainly cannot take credit for all this since the work was spread out to a wide group of teams and talented, dedicated individuals. I want to acknowledge the excellent contributions from the team members: Mike Pearce, Bob Blithe, Dr. John Howell, Mike Grippi, Quaker Chemical Corp.; Jeff Leiter, Leiter and Cramer LLC; and Chuck Timms, Broiles and Timms LLP. We made tremendous progress in two years, and we are not done yet, but we are very close to completion. I learned that leading teams and individuals requires patience and listening skills to understand why people say things when they do. I feel good that we offered a workable solution to SCAQMD for VOC measurement in a way that both parties could live with. This effort will ultimately be part of something that is much bigger than their district’s immediate concerns.
You can reach John Burke at jburke@houghtonintl.com.