Real-world oil analysis: Part III
Jack Poley | TLT On Condition Monitoring May 2010
When opining on oil analysis data, it is not always possible to have a correct opinion.
Continuing our exploration of real-world oil analysis, here is a collection of four sets of data from a final drive (planetary gearset) on an earth mover that really presents no evaluation mystery at the macro level. Get rid of the dirt and water, flush out the sump best one can, resolve the reason (seal compromise, lube-handling practices or one-off extra-hostile environmental or usage conditions) and have a fairly healthy gear system—assuming it hasn’t failed from neglect since the problem was detected two samples earlier.
The lube was changed one sample ago; that’s drained, as in the entirety of the work that was done. This customer evidently believes or hopes that changing the oil makes the problem go away, as no maintenance effort beyond the change was undertaken, nor was a system flush attempted. Well, at least the numbers got smaller.
There are, however, some interesting (assuming you enjoy dealing with oil analysis-data theories and puzzles) things to notice within the detail and to file in the reasoning section of your mind for application elsewhere.
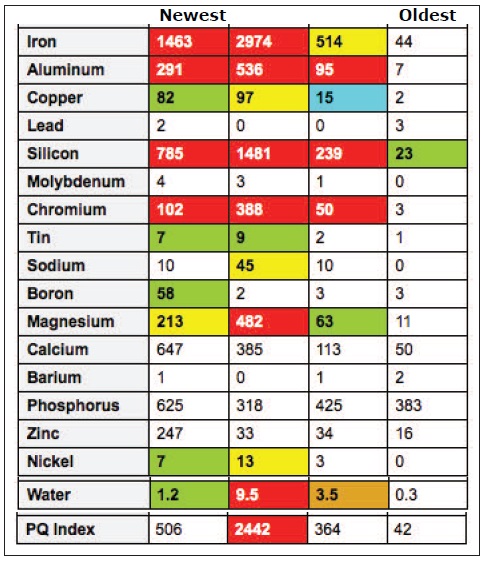
Figure 1.
Assume for practical purposes that the sampling intervals are reasonably close (and they are).
1. Although dirt (silicon) and water are the problems, the dirt is perhaps of more of concern than the water with respect to causing wear. What evidence suggests this?
2. Where are the elements sodium and magnesium coming from?
3. Are there “big” wear particles occurring or little ones?
4. What’s nickel’s role?
5. Chromium’s?
6. Copper’s?
Here are my answers to the above questions:
1. The dirt (silicon) is seemingly much more detrimental or is at least the driver of increased wear metals. Note the presence of higher water two samples ago and much lower iron with correspondingly lower silicon, although they are still enormously high, even for off-highway quarry applications. The silicon is in lock step with iron, whereas the water is not. Then again, you by now know my view on water and its inherent lack of dependability in terms of determining a precise value.
2. Sodium and, more evidently, magnesium seem connected to silicon. It is not unusual to see magnesium in second or third position as an abrasives corroborator. Sodium is less common but might be more so when silicon levels are at the concentrations shown. Frankly, I’ve never seen such a spike in sodium before, but it tends to make some possible sense. In any event there is a reasonable possibility that the silicon abrasive source is more related to airborne contaminants than to such possibilities as poor lube handling, because it is unlikely that lube handling would result in repeated similar contamination. This speculation may be resolved over time.
3. It appears all detectable size ranges of particles are present in this group of samples. We see plenty of spectrometric iron, and the PQ result moves nicely, as well. So we seem to have a machine being ground to death at a rapid pace, with a catastrophic failure as a possibility, too.
4. Nickel is likely an alloy with Fe in the various steel types in the component’s parts. With such high levels of iron, nickel is making its proportional appearance, adding to the situation’s urgency. (My guess is this machine is done, and one may as well consider running it to failure in case it lasts a few more rounds of testing without any serious attention).
5. Chromium is much the same as nickel but suggests chrome-hardened steel shafts or rolling elements and the like. Chrome is more indicative of imminent failure than is nickel here, including the concentration levels.
6. I’ve often speculated about copper’s tolerance for abrasives. Abrasives can be embedded within copper bearing/ bushing surfaces without chipping out much copper while holding abrasive shards in place to act as a chisel-on-lathe effect against the shaft. Regardless, copper is not a significant player in this wear scenario, though bushings, thrusts and the like are probably taking a relative beating, too.
At this point in time, the problem yet remains getting the big picture cleared up, if there’s still time. And the proper steps remain the same as they would always be:
1. Drain and flush the system as thoroughly as possible, which
(a) Minimizes further abrasives influence and
(b) Restarts the data progression from a more neutral position.
2. Diagnose all the possible reasons as to why this compartment is so besieged with dirt, water and wear until you are confident you’ve identified at least one reason (so that you can do something potentially constructive to mitigate the problem’s return).
(a) If the issue is related to usage conditions, e.g., the machine operated in a mud hole, or was dusted from a storm, then this is a one-off event and the likely issue is plainly visible when one looks around.
(b) If poor lube-handling practices are the cause, ask
i. Is this type of problem extant in a number of compartments of like type?
• Could it be a seal flaw in this planetary?
• Could it be maintenance practices on this particular compartment type?
• Is the problem isolated in a particular operating location among several others?
ii. Could a service person be handling lubes carelessly during fills or top-ups?
• Could the problem be careless delivery or storage?
• Could it be the location’s particularly hostile environment?
Perhaps the macro view is not as trivial as was initially implied. As I try to convey, when opining on data in the oil analysis world it is not always possible to have a correct opinion, but it is almost always possible to have a reasonably valid opinion, i.e., one that can be supported by citing evidence or lack thereof.
The responsibility of an evaluator is to present as many reasonable possibilities as the data and evidence suggest, preferably in order of likelihood, based on experience. Evaluators are responsible for leading the horse to water. The horse needs to take over from there.
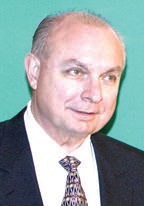
Jack Poley is managing partner of Condition Monitoring International (CMI), Miami, consultants in fluid analysis. You can reach him at jpoley@conditionmonitoringintl.com. For more information about CMI, visit www.conditionmonitoringintl.com.