What are the biggest challenges to using wind energy?
TLT Sounding Board April 2010
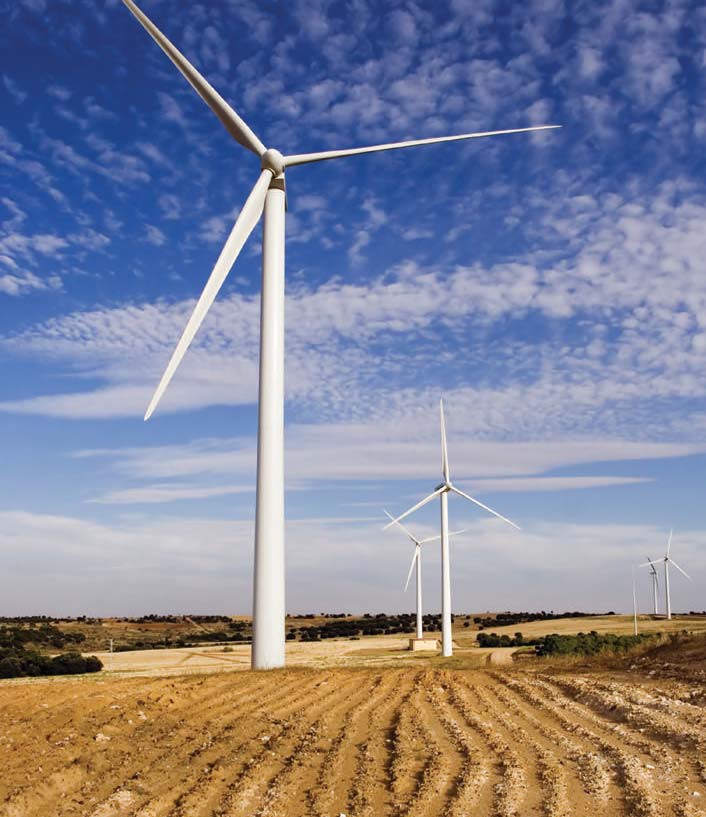
www.canstockphoto.com
Wind farms continue to spring up on land and sea, and the mainstream media is touting their great promise for energy generation. However, TLT readers note there are many technical issues that need to be solved before wind energy reaches its full potential. Among the technical issues cited are energy distribution, inconsistent wind, proper lubrication, gearbox maintenance and finding functional locations. Asked for solutions to solve problems relating to gearboxes, readers suggested specialized lubricants, offsite condition monitoring through sensors, improved metallurgy and direct drives. As one member stated, “Direct drive offers simplicity. Simple is beautiful.”
Distribution is probably the biggest issue. There’s plenty of wind, but the population centers are not necessarily near the best turbine locations.
Providing continuous reliable power.
The inability to generate and store energy for peak periods. People don’t want to see them in their backyards. Gearbox design is still a problem.
Continuous output.
(1.) Making this energy source profitable and (2.) making the towers and their operation non-intrusive.
The nationwide distribution system is reportedly a mess.
False brinelling problems on rolling bearings.
Return on investment.
Wind energy will damage the aesthetics of the environment. It is also grossly inefficient and requires massive subsidies.
Insufficient wind speed at the affected location, governmental support for the project, availability of a proven wind generator supplier.
Environmental impact (noise, landscape).
To convince the public that a wind turbine at sea is not a horizon pollutant.
Noise and other public acceptance issues.
Downtime due to worn bearings causing metal labyrinth seals to touch down. This leads to costly repairs.
Maintenance of the turbines and getting them on the grid since they are typically set up in remote areas.
Severe weather damage.
Finding a place to put them without public opposition, then getting power transmission from them.
NIMBY syndrome—people want cheap energy but not if it inconveniences them.
Uncertainty of financial payback.
Real estate costs.
Building sufficient infrastructure quickly enough.
Find the right location with steady-state winds. Get an agreement from local landowners. Get the right financing to build, run and maintain the farms.
Incorporating it into an overall energy supply strategy.
Infrastructure costs. I’m OK when private firms invest. I’m not OK when regulated firms invest and then pass the investment costs to the users.
Convincing towns to use their own money to build these expensive rigs.
Developing a smart power grid that can store electricity during lulls in wind speed.
Maintenance as the fleet ages.
Long lead times and the second highest cost of capital for all types of power generation.
Preventing gearbox failures.
Finding places where people are willing to have the windmills that also have the power grids close to them.
Coordinating power grid energy demand between wind power (or any weather-dependent energy source) and other fossil or nuclear power sources.
In Latin America the problem is the cost of this energy.
Finding a lubricant robust enough to withstand oxidation.
It’s costly to store excess energy on a windy day, and you need conventional energy when the wind doesn’t blow. A cost-effective workaround is to use a smart grid linked between nations, but that would require the concerted effort and investment of multiple governments.
It’s difficult for new suppliers or those with innovative and higher performance (problem solving) products to enter the supply chain without years of meetings and field testing.
Achieving reliable lubrication for many years with minimum maintenance.
Maintenance of offshore wind turbines.
Killing of birds/bats in the propellers.
Confidence in the technology and funding. Would it be the private sector, public sector or both?
Equipment reliability and efficiency.
Costs of production are higher than conventional alternatives such as hydro, nuclear and coal.
No consistent wind in the Midwest.
Finding enough locations for wind turbines.
Unfortunately in New England, all of the best wind sites are the most visible.
Noise pollution.
The design and inaccessibility of the gearboxes cause high maintenance costs. These costs discourage its growth as an energy source.
Installation costs.
Between grid access and social concerns, there are few sites that are ideal.
The delivery system. The electrical infrastructure has been neglected for years, and we will have to upgrade the grid. Wind farms are/will be in remote areas, and the grid must be expanded to reach them as well as carry the juice effectively.
Cost-effectiveness, especially for small islands. Availability of land for a site where you can get the right wind speeds, grid access, road access.
Durability of wind turbines.
Maintenance on lubricating oil system, specifically the gearbox filtration.
Wind turbines are not area-efficient! What is needed are more efficient turbines, possibly larger blades and higher speeds and improved gearboxes with less friction loss, resulting in higher electrical outputs per turbine. Lower towers also might improve efficiency.
Just the fact that you have to have so many gigantic fixtures on the landscape.
Building a smart energy management to overcome the problem of non-consistent wind.
Do you think it is possible for the U.S. to achieve its goal of 20% of its energy needs through wind energy by the year 2030?
Yes
43%
No
57%
Based on responses from 155 TLT readers.
Please describe any techniques that can improve the reliability of wind turbine gearboxes.
Maybe we need to sacrifice some efficiency and use hydrostatic systems to transmit the power?
Improved specialized lubricants and gear materials.
These are not low tech, so you need improved user understanding and networking as to what is working. Need an independent group doing a root cause for all failures with the information being made available.
Adding a torque converter between the blades and the gearbox. The idea here is to maintain constant speeds and loads. This would aid in designing gears and bearings, predicting life of gearbox and lubricant recommendation. (This may have already been tried.)
Screening extreme pressure and antiwear lubricant additives via FZG device.
Application of boundary lubricant additives.
Tight control of magnetic-slip clutches for overspeed protection and automatic re-engagement.
Instead of using the conventional metal labyrinth seals, use non-contact PTFE seals. If the bearings wear causing seal touchdown, the slick PTFE will not cause costly repairs.
Unfortunately you might have to break a few of these machines to see if new techniques work. With the load factor on the gearbox and difficult accessibility for service, I think the direct drive wind turbines might be the future for larger units.
Better boundary layer lubrication.
Lube oil cleanliness.
Gear manufacturing and controlled surface quality to reduce friction.
Engineered thin film coatings to protect wear surfaces.
Select the best lubricant available. Keep the oil clean using a high-performance filtration system. Perform continuous oil monitoring through detailed used oil analysis.
Online condition monitoring.
Detailed work on high-stress, low-velocity gears. High-quality maintenance.
Using a simpler (no more than a three-gear drive) system using mercury-encased bearings.
Do not use in climates below 40 F or above 100 F.
Desiccant breathers, heat removal, lubricant product selection, gearbox installation.
Online lubrication analysis for viscosity and metals for each wind turbine.
Use the vertical spiral blade design. Puts the gearbox on ground where you can maintain it.
Use thermally stable extreme pressure additives like polysulfides.
Use of nanotechnology friction modifiers in concert with extreme pressure additives.
Easier ways to access the gearboxes for preventive maintenance.
Making them as simple as possible. Having the most qualified people service them. Proper installation and preventive maintenance schedules.
I have enjoyed reading about controls that attempt to reduce wind shock loads.
Eliminate the gearboxes by using direct drive systems. Reduce complexity of gearboxes. Better design to manage operating transients.
Using the correct lubricant and conducting regular preventive maintenance including oil analysis.
Improved testing of the oil. As these are often only serviced once per year, standard tests are not sufficient to provide adequate information to make informed decisions.
Remote oil monitoring. Built-in, thermostatically controlled air/oil heat exchangers.
Metallurgy, material science, friction modifiers and extreme pressure agents. The use of smart sensors and microprocessors to automatically detect overly strong wind and disengage the gear train. The use of electromagnetic braking to slow the blades to within tolerable speeds.
A more scientific approach to gearbox design and use of properly formulated gear oils.
Higher-performance synthetic gear lubricants with very high performance and long-life additives. In many cases these can also achieve energy savings for the gearbox.
Power densification, thin-fi lm and tribo-coatings.
Realistic sealed-for-life gearboxes.
Reducing the weight of blades and other components. Improvements in gear manufacturing technology. Improvements in sealing technology.
Seals, sensors to warn of failure, long-term lubrication.
Remote condition monitoring and on-board lube oil conditioning (filtration, condition monitoring).
Rigorous preventive and condition monitoring programs.
Increased vibration dampening in design.
Better manufacturing/workmanship.
Utilizing proper lubricants designed for wind turbine gearboxes and hydraulics as well as using the correct ASTM lab tests that give the best data.
Pressurized dry sump lubrication.
Design upgrades to limit the ingress of dirt.
Special hydrodynamic bearings.
This issue may require the development of new materials of construction, new gear manufacturing techniques, new lubricant formulations, etc.
Use of the highest quality grease to carry the load and keep maintenance to a minimum.
Proper selection of gear configuration and the use of synthetic lubricants.
Gear inspections and oil maintenance.
Run them like industrial gearboxes. Very clean oil, stable operating temperatures.
Better hardening and synthetic lubes.
Use of more predictive technologies to monitor the condition of the gearboxes.
Varying wind forces causing unintended or unmanageable stresses on the gearbox leads to unsatisfactory uptime percentage. Significant gearbox filtration upgrades and strengthening the gearbox or eliminating it altogether. Unless this equipment can be moved to ground level, it’s not practical.
Testing of lubricant and gear reducers in simulated working conditions to identify weaknesses before building wind farms.
Use of lubricants specifically designed for the extreme conditions that a wind turbine may experience.
Great strides have been made in wind turbine reliability.
Better metallurgy.
Use of microfiltration and online monitoring of the gearbox oil condition.
Gearboxes must have lower friction loss to improve efficiency. They may need gear oils with better/more friction modifiers.
Eliminate them!
Synthetic gear oils with a high-performance additive system to minimize micropitting.
It’s the engineers’ lack of climate knowledge, not techniques, which needs to be improved. A stiff breeze here in Minnesota couldn’t turn the gearbox when the temperature plunged to -30 F. It’s still not turning!
Move from industry-approved GO/lubes to PAO-based products.
Which of the following designs has more promise?
Wind turbines with gearboxes
57%
Wind turbines with direct drives
43%
Based on responses from 155 TLT readers.
Editor’s Note: Sounding Board is based on an e-mail survey of 13,000 TLT readers. Views expressed are those of the respondents and do not reflect the opinions of the Society of Tribologists and Lubrication Engineers. STLE does not vouch for the technical accuracy of opinions expressed in Sounding Board, nor does inclusion of a comment represent an endorsement of the technology by STLE.