Operator-based lubrication practices
Mike Johnson | TLT Best Practices March 2010
You’ll need well-stated goals, practices, accountability—and a commitment from management to make it work.
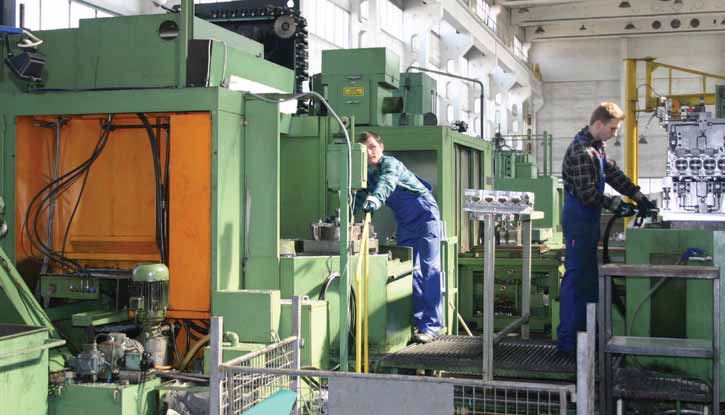
KEY CONCEPTS
•
A well-conceived plan, coupled with a firm commitment to consistently fulfill scheduled practices, can deliver quality results.
•
Selecting the right task type and clearly defining the task steps are essential in assuring that operators can complete the work that is scheduled.
•
Investing in clean-handling tools and machine-specific practices can help your program achieve its full potential.
Organizations improve manpower productivity and effectiveness in a variety of ways. The largest labor category is the production department. Where feasible, managers have incorporated operators in routine, orderly and sometimes sophisticated preshift machine checks to determine if the machine is ready for production. This concept is well established in some production environments because of the nature of the way that the operator interfaces with the machinery.
Production of incremental parts lends itself well to this approach. Examples of this include the use of machines to assemble tires before they are cured, the machining of gears or stamping of metal frames for assembly into parts for finished goods.
Continuous process industries such as petroleum refining, cement and paper manufacturing and chemical production operate continuously, with, it is hoped, no definite start and stop point over the course of a shift, day or month for that matter. These manufacturing processes have limited success with operator-based care.
It seems likely that as management continues to hunt for ways to improve productivity, more interest will be placed on operator-based care and operator-based lubrication tasks.
Following are a few reasons it makes good sense to include operators in machine care:
1.
Economic pressures forcing manufacturers to run lean to an exaggerated degree.
2.
Loss of skilled labor to retirements (the front edge of the boomer generation hits in 2012).
3.
An inadequate number of experienced, motivated and talented skilled labor replacements for the current retirees.
4.
Common sense allocation of labor.
OPERATOR-BASED CARE
Whether piece or continuous production processes, operator-based care, including the simple but essential machine lubrication checks, should be fully explored.
This is not a new idea. Working as a supplier service technician in the mid-1980s, I observed several customers giving operator-based lubrication care a try. In most instances, the program was hastily launched, the operators fumbled around with oil cans and grease guns, machine dependability degraded, and the effort was abandoned. In several instances, I asked departmental managers the magic question: Why didn’t this work for your site? A repeated theme between organizations was a lack of definition of responsibilities and work accountability. The expectations weren’t well defined and therefore accountability was weak.
The same challenge exists today. Without definition and accountability, the quality of the lubrication practice is left to the ready knowledge of machine requirements and good intentions of the machine operators. Where motivation and worker skills are sharp, one could expect dependable results. Where this isn’t the case, results are poor.
Key success factors to operator-based care include:
•
Well-defined program expectations.
•
Well-defined operator appropriate tasks.
•
Simple, dependable, automated scheduling plan.
•
Clear commitment to maintaining accountability for work completion.
There are tasks that can and should be completed by operators but certainly not everything under the machine-lubrication umbrella. This article explores the possibilities of operator-based lubrication practices.
PROTECTING THE GAP
The oil-film for element bearings and all components with rolling interaction ranges from between one-half and one and one-half millionths of a meter. The oil-film for journal bearings and all components with sliding interaction is somewhat more substantial at three to ten-millionths of a meter. In both instances, these films are subject to numerous forms of disruption. The disruptions are called failure modes. Engineers and tribologists have identified multiple failure modes and have discovered that these repeat relentlessly. The key offenders are:
•
Contaminated sumps (dust, water, machine wear debris, air, heat, other lubricants).
•
The incorrect lubricant (too high or low viscosity, wrong additive type).
•
The incorrect sump volume (too much in greased bearings, too little in oil sumps).
These all are critical threats to operating machine sumps that could or should be eliminated. This begs a question about the day-in, day-out, year-in, year-out defined requirements: Have we unintentionally engineered failure into our practices? If maintenance and engineering managers are aware of the highly repeated threats to the microscopic film and are aware of a variety of ways that routinely scheduled activities create these threats and agree that it is best to eliminate these defects, why haven’t the practices been devised to preclude the threats?
Following are a few simple but vital daily requirements at the heart of successful operator involvement in lubrication practices:
1.
Verify and/or supply the needed amount of oil or grease to the machine sump.
2.
Verify the correct type of product for the application.
3.
Keep contaminants out.
4.
Observe and report on anything out of the ordinary.
These needs are clear, simple and easily documentable. Theoretically, if these conditions are fulfilled, critical components can last decades rather than months or years. However, the destructive effect of failing any of these requirements is equally well documented.
Creating a reliability-centered and operator-based lubrication practice is not complicated, but it is detailed. Program design should enable attention to the maximum number of details with the minimum amount of human involvement. This requires:
1.
Purposeful planning.
2.
Clearly defined machine care and program practice objectives.
3.
Equipping operators with the proper training and tools for the tasks.
4.
Using available technological (hardware, software) tools for implementation and management.
5.
Management support demonstrated by consistently maintaining worker accountability.
6.
Quality brand selection and local supplier service support.
DEFINING THE PROGRAM
A quality operator-based lubrication plan can be recognized by the following characteristics:
1.
Clearly defined program goals and objectives—and a plan for accountability. Program goals should align seamlessly with standing reliability improvement goals, and objectives should support the defined goals.
Suggested goals include:
•
Improve machine availability and productivity through improved machine reliability.
•
Reduce direct costs associated with direct maintenance labor.
•
Reduce direct costs associated with machine component replacement.
•
Implement lubrication practices that support plant reliability objectives.
It is better not to start a program than to start one with a half-hearted commitment. Without full production management acceptance and commitment to the short- and long-term requirements, the operator-based care initiative will fail from neglect. A suggested plan for accountability to support the goals should be unambiguous. Production and shift operator management must be fully committed to assuring operator compliance, regardless of encountered resistance.
2.
Clearly defined machine care and program practice objectives. Objectives should help focus attention on the tasks and details that need to be fulfilled for both the broad program and narrow individual machine requirements. Strategic program level management objectives could include:
•
Lubrication tasks and frequencies optimized, according to machine reliability needs (based on standardized engineering practices).
•
100% first-time completion of all scheduled runtime activities.
•
Maximum 10% repeat of notices for corrective action requests.
•
Completion of training and testing-based verification each six months.
•
Fully automated record management.
Once provided with the strategic direction (as outlined by the proposed objectives), the reliability engineer and/or development team will then construct the tactical steps necessary to achieve the plan.
The tactical requirements supporting program objectives include:
Lubrication tasks and frequencies optimized, according to machine reliability needs.
A.
Provide or develop a machine importance hierarchy.
B.
Based on the criticality assessment, a matrix of lubrication, inspection and condition-control requirements and frequencies is to be constructed that assures coverage of each machine, according to each machine’s importance.
C.
Based on the criticality assessment and the matrix of required activities, standard operating procedures (SOPs) are developed for each type of task and set into the required frequencies. There should be no ambiguity for what is expected to be accomplished for each machine.
D.
The complete set of tasks and frequencies should be compiled and scheduled using a route-based program.
100% first-time completion of all scheduled activities.
A.
Each route should carry a low enough workload that assures enough time to complete the route each time it’s scheduled.
B.
Production management should reinforce the importance of route completion promptly following issuance.
Maximum 10% repeat of notices for corrective action requests.
A.
Operators provide notices to management of a change in machine operating state.
B.
Notices are reviewed by planning and acknowledged as either received and scheduled for action or rejected with justification.
C.
The inspection should be completed expeditiously.
100% successful completion of training and testing-based verification each six months.
A.
Instruction should be provided to operators commensurate with the level of expected responsibility.
B.
Training should be task-specific, thoroughly addressing each type of task to be performed.
C.
Training should be completed initially before tasks are assigned and repeated each six months.
D.
Training should be hands-on everywhere possible.
3.
Equipping operators with the proper training and tools for the tasks.
The required material tools are simple and inexpensive:
•
Cleanable, sealable oil-handling containers.
•
Grease guns equipped with volume meters.
•
Clean, well-lighted, dry oil-storage facilities.
•
Tools for loading/transferring oil from one vessel to another.
•
Clear tagging for each machine identifying the required lubricant.
•
Waste oil disposal vessels (if oil changes are added to the task list).
4.
Using available technological (hardware, software) tools for implementation and management. Operators should not be saddled with extraneous, time-consuming manual documentation requirements for demonstrating completion of the scheduled tasks. A fully automated record management system can be selected from reputable vendors, including quality assessment modules on a few existing CMMS packages.
The records management system should provide:
•
Efficient management of a large number of repetitive tasks.
•
Sequential tasks structure (lists, routes) showing all required tasks, timetables and procedures.
•
Ability to attach supporting documents (pictures, drawings, diagrams, etc.) for detailed illustration of each task would be welcome.
•
A means for operator communication about each task, including capability for:
A.
Denoting completion by time, date and operator.
B.
Denoting reasons for lack of completion.
C.
Denoting capture and reuse of operator observations.
D.
Denoting operator-recommended maintenance activities.
E.
Tracking each task against required completion intervals.
F.
Tracking each recommended maintenance activity for completion.
Management should expect at least three years of attention from a dedicated technical resource to ensure a complete culture change and should not accept scribbled notes from poorly defined routes.
Figure 1. Typical operator lubrication route. (Courtesy of Design Maintenance Systems, Inc.)
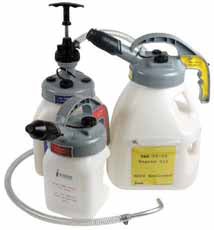
Figure 2. Clean-handling tools are very important to maintain lubricant effectiveness. (Courtesy of ProActive Lube Manager, Inc.)
5.
Management support demonstrated by consistently maintaining worker accountability. Human behaviors will not change in an implementation and leadership vacuum. Perhaps the greatest risk to the long-term successful completion of this transfer of responsibilities, and ultimately a long-term improvement in plant productivity and machine reliability, is
shift management involvement in reinforcing discipline to complete all scheduled activities.
Shift operators will adopt a sense of responsibility with the program that mirrors middle and senior management behavior. If senior management does not take a visible interest in the daily and weekly completion of the assignments, and verify that those are done according to the defined quality plan, eventually the assignments will not be completed.
There are instances of programs receiving ceremonial launch through plant and/or senior production management actually adopting machines to physically clean, inspect and lubricate (i.e., leadership by example). If the ceremonial approach fits the plant culture, it can be beneficial. If this approach doesn’t fit the culture, then it may be counterproductive.
6.
Quality brand selection and local supplier service support.
Lubricant vendor selection is not more or less important for an operator-based plan than it would be for a mechanic or lubrication technician-based plan. Clean, dry, chemically correct lubricant supply is important and is likely the least difficult portion of the plan to complete.
It is a common shortcoming to characterize the success of a plant lubrication program based upon the reputation of the quality of the brand or supplier rather than on the actual results of the program. Vendor and product quality is certainly important, but even the best possible quality products will not deliver acceptable results if they are abused during the application practice.
SUMMARY
Operation-based machine care, specifically lubrication care, has been a point of interest by senior management for many years but is still not a widely adopted practice for continuous process plants. A well-conceived plan, coupled with a firm commitment to consistently fulfill scheduled practices, can deliver the quality that is expected.
A well-conceived plan will be inherently reliability-centered, machine-specific and will include stated goals and objectives that are both achievable and measureable. The plan begins with a machine review for detailed task development, review of material resources needed for the tasks in the plan and an appropriate allocation of time for completion.
A planning and tracking system is designed around the tasks to enable routine tracking of multiple instances of multiple tasks/events with the minimum dependence on manual record keeping.
Operator training is developed around the machine-specific tasks, routes and the tools for delivery. In addition to the obvious support from management’s dedication of resources to the development of the practices, visible and vocal management support should be demonstrated through holding employees accountable for work completion.
Mike Johnson, CLS, CMRP, MLT, is the principal consultant for Advanced Machine Reliability Resources, in Franklin, Tenn. You can reach him at mike.johnson@precisionlubrication.com.