Real-world oil analysis
Jack Poley | TLT On Condition Monitoring January 2010
Forget about getting all the facts—in the field you have to work with the information at hand.
Let’s continue our discussion on concepts in oil analysis data evaluation by looking at a worm gear drive in an industrial manufacturing plant. There are 17 reports available for this component, all revealing interesting problems and anomalies regarding the analytical evidence.
We’re faced with a problem in the very first sample, as shown in Figure 1, in the P (phosphorous) series. It’s flagged at Severity Two (abnormal) with the auto-evaluation system in use.
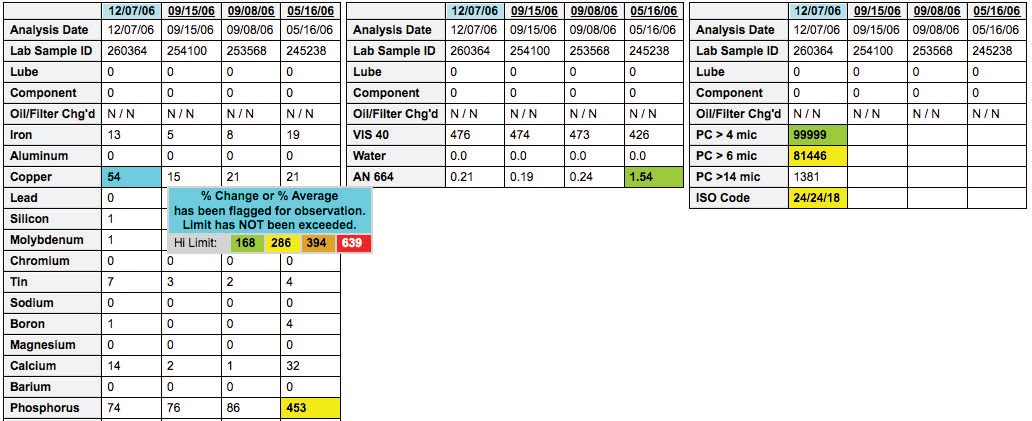
Figure 1.
One might ask, “How does the system know where to rate the P value?” Answer: Because there are 900-plus samples taken from a dozen of these same worm gear types, which are manufactured from the same plants available for statistical analysis. This P level doesn’t occur often and, thus, is obviously not from the lubricant’s additive package. (Note: Without a lube manufacturer/brand and without a new lube reference, additive metals flagging levels are determined from the used lubes directly, normally close enough for oil analysis additive metals profiling, given no supplier changes.)
Meanwhile, the expert system had to receive expertise from the field (i.e., it is possible for process water to enter the gearset, and this process water contains P). All I can recommend is to check for this possibility and correct it.
Draining the oil, in this case, is not really necessary, although it would reset the P level, as there is no water present. The sample provided indicates such but, if you’ve read this column regularly, you know I don’t have a lot of faith in water concentration reporting.
Regardless, the oil appears to have been changed since the P level dropped dramatically. What? You want to know the amount of hours on the lube? Get in line. We don’t even know the manufacturer/brand of the lube. (Field Note: If labs rejected all samples with missing or obviously wrong information regarding lube manufacturer/brand and target viscosity grade or lube and component time, they’d likely forfeit half their business!)
The fourth sample includes two important results:
1. A particle count was performed for the first (and last) time, indicating some but not severe deviation from the contamination goal. Why was the particle count interrupted? Management probably should have replaced with particle quantifier (PQ) or direct-reading ferrography (DRF) inasmuch as this gearset is unfiltered and large particles might reveal something.
2. A trend flag (blue) is assigned to Cu (copper) as it has moved significantly, although not enough to flag it for a range violation. Something to note and, for the most part, do nothing about, unless there is supporting evidence elsewhere, either in the analysis or at the component site, where eyes and ears are available.
Moving further along the sampling timeline (see Figure 2) and noting that the statistically set copper flagging levels are rather high—recall there are 900-plus samples from these types of worm gearsets—following are some thoughts to consider:
1. Why is the copper jumping around? My first response is I don’t know for sure. Copper (bronze) is usually part of the metallurgy of worm gears (the driven gear more so). The gearset is unfiltered, so larger copper particles could be floating around and, although not completely detectable with conventional spectrometric analysis as used in most labs, could nevertheless provide added concentration on a given sample. Then, too, there may have been something unique occurring in the duty-cycle for those samples with higher Cu such that greater-than-usual (for this component) wear occurred. Since we’re not going to recommend any action, because the values are still rather low statistically, we can be content with pure speculation for now.
2. The jump from 54 to 82, also blue, is not nearly as great a percentage movement as from 15 to 54, but it’s still mathematically significant. But let’s not get too excited about any of this—recall we have no time data on the lube service interval. The trending algorithm is recognizing that Cu is beginning to creep and is providing a safety net ahead of range violations. This will eventually get vetted from maintenance action feedback if it’s provided.
3. Why have trending on if we haven’t got lube time? That’s a fair question. Here the customer has at least indicated “N” for “no” as to lube/filter (as applicable) change, so this sequence could be viewed as a continuous development despite our speculation that the lube was changed following the first sample in this sequence, whereupon trending would have some merit. The more practical answer might be: It probably won’t hurt to be apprised of movement like this and one can always temporize (standard policy for this expert system) or ignore at will.
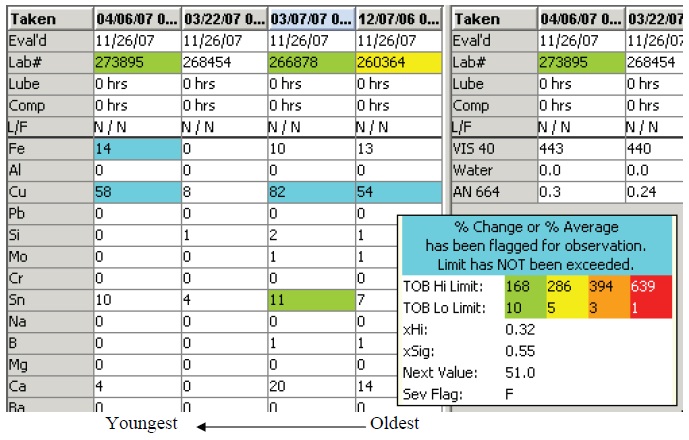
Figure 2.
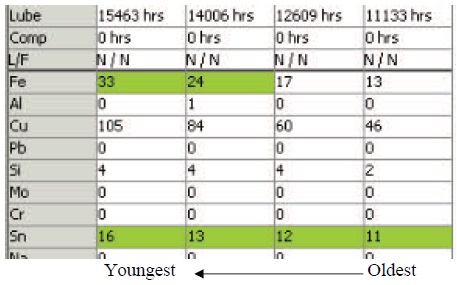
Figure 3.
Looking at Figure 3, another year’s worth of samples downstream, these data look benign at first, but there is some modest Fe (iron) growth along with unflagged Cu. Note that we now have the luxury of lube hours, if not those of the component, so mild wear metals growth seems plausible.
Let’s go back to our sporadic copper in Figure 2 (54, 82 and 8 ppm). Moving chronologically forward, we might say that the 8 ppm value doesn’t make sense, assuming no lube change has occurred. That much Cu cannot simply go away without an oil drain, especially since this is an unfiltered system. A zero ppm Fe does not help the trend’s integrity, either. Could it be a worm gear sample from a different machine?
There’s no way to go back and tell now, so onward we go. At least this grouping shows exemplary progressions with everything seemingly correlated (Fe, Cu, Sn [tin]).
In my next column, we’ll investigate further developments on this component.
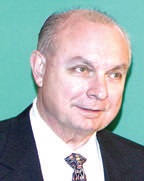
Jack Poley is managing partner of Condition Monitoring International (CMI), Miami, consultants in fluid analysis. You can reach him at jpoley@conditionmonitoringintl.com. For more information about CMI, visit www.conditionmonitoringintl.com.