Strategic oil analysis: Estimating remaining lubricant life
Mike Johnson & Matt Spurlock | TLT Best Practices January 2010
Once you understand how oxidation works, you can choose from several methods to postpone or stop it.
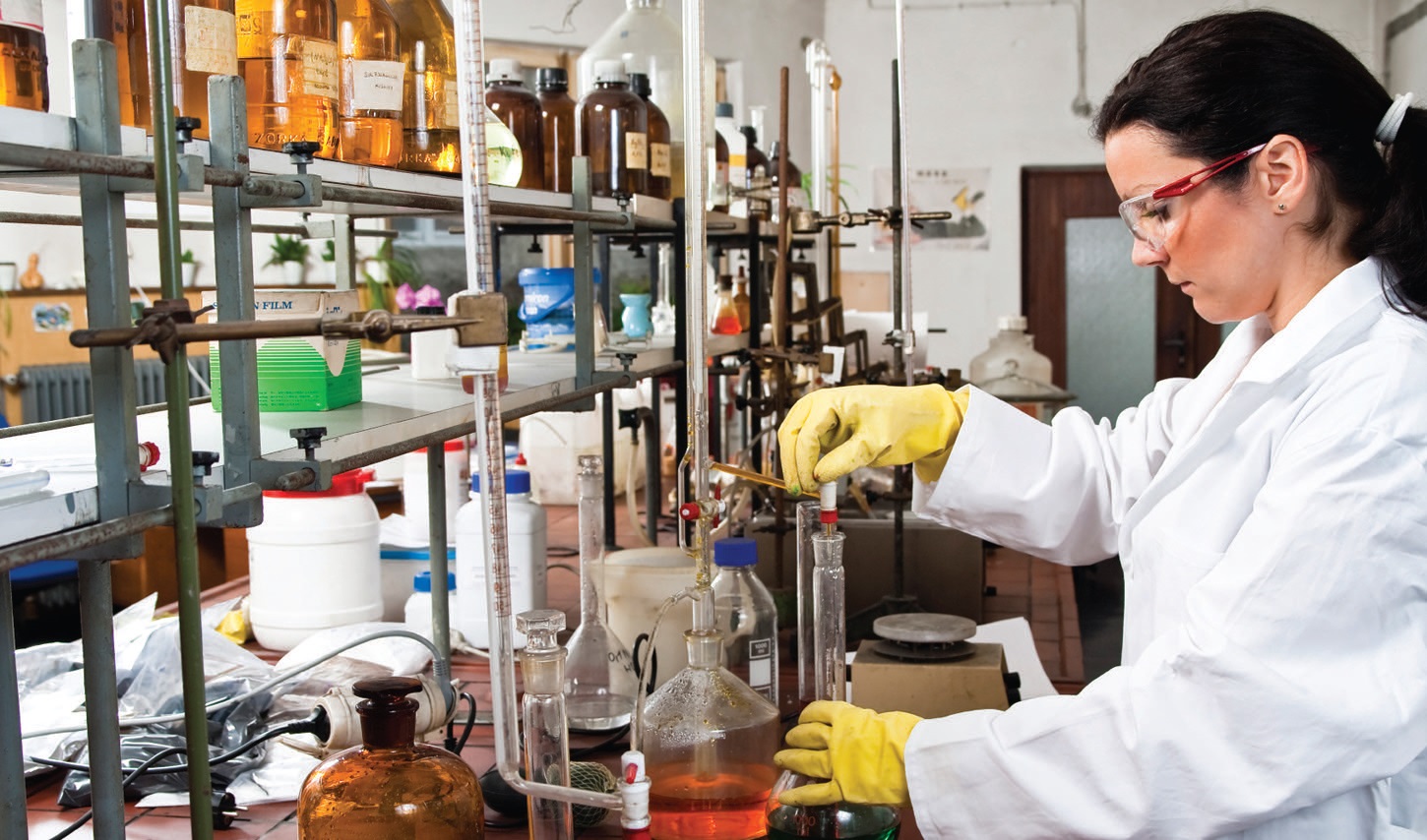
www.canstockphoto.com
KEY CONCEPTS
•
Oxidation is a common name for a complex chemical reaction process that ages the lubricant, eventually requiring replacement.
•
Base oil quality is a key factor in resisting oxidation and preserving lubricant life.
•
Oil analysis is the key to measuring and managing oxidation and lubricant degradation.
This is the first of five 2010 oil analysis articles addressing a practical challenge for reliability managers: measuring and managing lubricant vitality. This article sets the pace for the remaining articles, which will provide rock solid lubrication program management insight for reliability and lubrication program managers.
Articles Two and Three address on-site oil analysis with and without instruments, respectively. Article Four explores rate-of-change alarms for machine and lubricant condition. Article Five provides a roadmap that program managers can use to qualify the analytical methods and practices for use in selecting an oil analysis supplier.
It is the hope of the authors and TLT editors that the information provided will have a substantial positive impact on the vital work of machine reliability management through the routine lubrication program practices.
This article begins with a simple question: Why do we replace lubricants?
Generally practitioners arrive at one of two reasons: either the lubricant is dirty or it’s worn out.
Dirty is easy to define and measure. Worn out is more difficult, but this, too, can be defined and measured.
Lubricants are a chemical stew of base oils and additives. Immediately upon placement in a machine, the stew begins to change. At any point during its use, if the lubricant is no longer capable of protecting the machine from wear, it must be changed. The aging process is dominated by chemical changes, generally involving oxygen, which we call oxidation.
This article:
•
Reviews the oxidative process
•
Looks at the influence of a lubricant’s two key ingredients (basestocks and oxidation inhibitors)
•
Examines measurement methods useful to measure remaining lubricant usefulness
•
Considers techniques that can help extend lubricant usefulness.
THE OXIDATION PROCESS
As lubricants age they become less capable of delivering their expected performance and progressively dump increasing amounts of garbage (sludge and insoluble compounds) into the oil sump. The primary driver for these problems is oxidation. Oxidation is a general term used to describe a complex series of chemical reactions, chemical changes and formulation of new unwelcome molecular species within a lubricant sump. Initially, oxidation was characterized as a chemical reaction involving oxygen. The definition has been expanded to include any reactions involving electron transfer (
1). Lubricant oxidation is a three-stage process:
Stage 1. Initiation
Stage 2. Propagation
Stage 3. Termination.
Stage 1. Initiation involves the formation of a free radical, an atom or molecule fragment with one or more unpaired electrons. The biggest contributor of free radicals is oxygen itself. Contaminants that are rich with oxygen (air, water) feed oxygen to the system.
Other common radical initiators include sunlight (UV radiation), wear metals, extreme temperatures induced by adiabatic compression of trapped air, extreme temperatures induced by metallic contact, existing varnish and sludge within the system and flow electrification (electrical arc-discharge) in high flow circulation systems. Flow electrification is particularly problematic in that hydrocarbons are fractured, producing multiples of alkyl radicals.
Free radicals are highly reactive and short-lived, quickly combining with hydrocarbon components to form alkyl radicals and hydroperoxi-radicals.
Stage 2. The propagation step occurs when hydroperoxi (peroxide) radicals react with the base oil or additives to regenerate an alkyl-radical (or generate an alcohol and water) and restart the cycle. When high temperatures exist, the peroxide radicals split and sustain the chemical reaction. When wear metals are present, peroxides may catalytically split to sustain the reaction, even when temperatures are low.
The propagation step becomes autocatalytic, with the chemical reactions themselves providing the feedstock to start the next cycle.
Stage 3. The termination step occurs when the designated oxidation inhibitor (antioxidant) performs its function. There are several types of oxidation inhibitors used in lubricants. They may be classified as:
•
UV Absorber
•
Peroxide decomposer
•
Chain breaking-electron donor
•
Chain breaking-electron acceptor.
Slowing the lubricant aging process is largely dependent upon the quality of the lubricant raw materials selected, beginning with the basestock—the predominant raw material.
ANTI-AGING COMPONENT ONE
In 1993 API began categorizing base oils according to their production techniques in order to differentiate the higher quality materials lubricant manufacturers were starting to produce. There are five API Group Categories. Mineral oil-based products are identified as Group I, II or II, and the remaining two groups are reserved for man-made synthetic base oil types (
2).
API Group I base oils are manufactured by the solvent extraction refining technique. This technique, pioneered in the 1930s, separates oil molecules by size and removes some of the harmful constituents (heavy metals, wax, aromatics) found in raw crude petroleum.
GI (Group I) base oils are comprised of three molecule types (paraffinic, naphthenic, and aromatic) as well as a variety of sulfur- and nitrogen-based compounds. Additionally, GI oils are characterized as those oils that have < 90% saturated (= >10% aromatics) molecules and more than 300 ppm sulfur (
3).
Sulfur compounds and aromatic molecule structures are highly reactive and tend to react rapidly with oxygen to form various soluble and insoluble degradation byproducts. The high percentage of aromatics generally means a higher risk of oxidation within the lubricant sump and short lubricant lifecycles.
A hydrotreating process was added as a final stage in solvent refining in the 1950s. Hydrotreating is a process where hydrogen is added to the basestock at high temperatures and in the presence of a catalyst to stabilize the reactive components, improve the color and extend the useful life of the finished lubricant product. This step helped but was not severe enough to fully neutralize the aromatic component in the finished products. Nonetheless, approximately two-thirds of the base oil in North America is produced using this technique.
GII (Group II) base oils follow a processing path similar to the GI products, except that instead of using solvents to extract the problematic compounds, GII oils are hydrocracked. This process uses extremely high temperatures and pressures to catalytically react hydrogen with the basestock to the extent that the aromatic molecules, sulfur and nitrogen components are nearly eliminated from the stock through a series of molecular rearrangements (formation of paraffin isomers, breaking of long-chain and naphthenic molecules, opening and reshaping aromatic ring formations).
The consequence of the hydrocracking process is that species of molecules in GII stocks are more uniform, and the majority of the reactive components from the solvent refining method are removed.
GII (Group II) base oils follow the same hydrogen processing path as the GIIs, except that these are more severely treated (higher pressure, higher temperature, longer process times). GII oils perform on par with some synthetic Group IV types.
When comparing GI and GII/GII finished lubricants, the GII/GII-based products are inherently more stable, more resistant to oxidation, experience less temperature-induced viscosity change and produce less sludge than their GI counterparts.
GII/GII stocks can be formulated to create low sludge tendency, highly oxidation-resistant finished products that can appreciably exceed GI formulated products. Viscometric (VI, pour point) properties also are expected to be superior with GII/GII formulations.
One drawback that may exist with regard to GII/GII oils (vs. Gis) pertains to their reduced ability to dissolve or suspend polar additives and/or the polar byproducts of lubricant degradation. The property in question is referred to as solvency. Lubricant stocks with high solvency are able to soak up polar additive compounds and lock them into place. Stocks with low solvency are unable or less able to soak up either these additive compounds or the polar byproducts of the oxidation process.
Figure 1. API basestock categories and tendencies (4).
Hydroprocessing and hydrocracking reduces the natural solvency and dispersancy of basestocks by reducing the concentration of aromatic and naphthenic hydrocarbon. This loss of solvency may be offset with the use of dispersants and high-solvency ester basestocks (
5). Lubricant manufacturers are able to overcome this inherent propensity of GII/GIIs to ignore the additive treatment (producing additive dropout) by creating a family of additives designed to blend effectively into the select base oil.
Group IV and Group V basestocks are completely manmade, engineered products. The many types of materials that comprise these groups nearly always have inherently superior oxidation resistance, although there are a few exceptions.
ANTI-AGING COMPONENT TWO
There are a variety of lubricant-based chemicals that can interrupt, slow down or stop the aging process. These chemicals as a class are referred to as antioxidants. There are primary (phenols, aromatic amines) and secondary (sulfur/phosphorous compounds) oxidation inhibitors.
The primary antioxidants, phenols and amines, are characterized as chain-breaking inhibitors because they absorb free (reactive) radicals to form a stable radical. These react more quickly with the radical than the base oil itself can, and the primary antioxidant is able to absorb more than one radical. Hence, the reaction chain is broken (
6).
Phenols and amines may be used either independently or synergistically with predictable results. Additionally, the types of specific phenols and/or amines that are used can also produce family-specific, predictable results.
Secondary antioxidants, primarily phosphorus and sulfur compounds (sulfides, disulfides, polysulfides, phenothiazines, dithiocarbamates, thiadiazoles, thiarams) act to decompose the unstable alkyl hydroperoxides into a more stable alcohol form. Sulfur-based antioxidant behavior is more complex, with potential for eventual formation of sulfuric acid and sulfur dioxides. Sulfuric acid is a powerful catalyst for lubricant polymerization and degradation (
7). Additionally, aromatic and sulfur-containing compounds (peroxide decomposers) tend to create an additional reaction step called Aldol Condensation stage, which encourages formation of deposits. Consequently, while potentially useful, these compounds must be used with discrimination (
8).
Synergies of different types of inhibitors working together in the same mode (homosynergism), in a dissimilar mode (heterosynergism) or both can produce effects greater than the sums of the components for a given lubricant basestock. In as much as there are differences in basestock performance, these additive strategies must be tailored to the particular select stock.
There are also types of antioxidants that enable the lubricant to produce incredibly high oxidation resistance values under bench-top test methods such as RPVOT (Rotary Pressure Vessel Oxidation Test) that also produce disastrous levels of sediment, sludge and residue. Phenyl-alpha-naphthylamine (PANA) is one such type compound that, due to its inherently low solubility, produces derivatives that have poor solubility, which produces copious amounts of deposits over time (9). PANA is still widely used due to its low cost and ability to create high RPVOT values.
The point of this last example is that it is most helpful to understand the type of antioxidant present and have a sense of its predictable behavior as part of the ongoing lifecycle-tracking plan.
MEASURING OXIDATION AND ITS BYPRODUCTS
One may choose two different directions to measure for the presence of/evidence of oxidation. One may measure for the cause or the effect.
Measuring for the cause: Antioxidants depletion. Antioxidants are widely used to limit oxidation. As long as the antioxidant is healthy and present at the appropriate level, the lubricant is generally considered OK for continued use. Antioxidants are consumed (degraded or tied up) with use and eventually reach a point where they are unable to protect the basestock. Each antioxidant has a chemical fingerprint that may be traced with commonly used oil analysis techniques, including Fourier Transform Infra-Red (FTIR) spectroscopy and Linear Sweep Voltametry (LSV, AKA – RULER).
FTIR analysis (ASTM E2412-04) is a routine and useful tool that offers a snapshot of the molecular species (fingerprints) present in the lubricant—both the wanted and unwanted varieties. Notably, FTIR can be used to measure for the presence of degradation from processes involving nitrogen (nitration), sulphur (sulfation), oxygen (oxidation) and antioxidant compounds. FTIR also is useful to measure for carboxylate oxidation products produced through traditional free-radical oxidation sequences. Thermal oxidation byproducts caused by either micro-dieseling, severe hot spots or electrostatic discharge conditions also may be tracked at specific IR wavenumber regions.
With the FTIR technique, the analyst compares the fingerprints of various chemical products with the fingerprints of the compounds from an unused sample. High concentrations of oxidation/degradation byproducts and/or low concentrations of oxidation inhibitors indicate a looming threat to the lubricant and the machine. Sulfur- and nitrogen-based compounds that aren’t supposed to be present also can be identified as byproducts of chemical change and will point to progressing stages of the aging process. Figure 2 shows the differential between used and healthy new engine oil samples, with pronounced peaks at various IR wavenumbers/frequencies. The location of the peaks and their amplitude (height) tells the analyst about the presence of a known byproduct of oxidation and/or chemical degradation.
Figure 2. Differential scan between a used and new engine oil. (Courtesy of Condition Monitoring International and WearCheck Africa)
Some species of antioxidants are difficult to identify with FTIR, suggesting that an overlapping technology is necessary. Enter LSV (Linear Sweep Voltammetry).
LSV analysis (ASTM D6971) can be performed either at the plant site or in the laboratory. With the LSV method, a sample is placed in an electrolytic cell with an electrolyte and solvent. Voltage is passed through the cell at increasing levels, and an electrical current “potential” curve is produced.
During the test phase, the electro-active species oxidize and increase the current potential. This potential is measured, plotted and can be use to indicate remaining oxidation inhibitor levels. The instrument used to provide this result, as shown in Figure 3, is called RULER.® The expressed purpose of the RULER measurement is to help the program manager grade for the concentration of oxidation-limiting chemicals left in the lubricant for the purpose of projecting either lubricant change schedules or other activities to manage the remaining lubricant lifecycle.
Figure 3. The RULER instrument depicts the concentration of healthy antioxidants in the oil vs. the reference. (Courtesy of Fluitec International)
Measuring for the effect: Oxidation/Degradation By-products. As lubricants age they become more acidic. Even lubricants that are highly alkali in nature (engine oils) age toward an acidic condition. Additionally, sludge and varnish deposits are an expected outgrowth of degradation from specific types of oxidation inhibitors and degradation of the base oil itself. The growth of strong and weak acids are routinely measured through a neutralization technique. The various oxidation byproducts that fall under the umbrella description of varnish and sludge can be, but are not routinely, measured by Acid Buildup (AN or TAN), Ultra-Centrifuge (UC) and Varnish Potential (MPC) techniques.
Acid Number (ASTM D974, D644) measures acidic constituents in the lubricant. The measurement of growth of acids in the lubricant is a widely utilized approach for checking for the signs of lubricant degradation and is applied to nearly all industrial oil analysis test methods. The constituents may be from proper concentration of healthy additives or from a variety of other challenges, including acids created by degradation, mixture with other lubricants, process chemical contamination, etc. This method is insensitive to weak organic acids routinely produced with lubricant degradation. Also, AN measurement can only represent a condition that has already occurred. Consequently, while popular, it does not present a fully accurate picture of lubricant health.
Ultra-centrifuge (UC—No ASTM Method) for sediment and sludge concentration has been used extensively but is a subjective test method. In this method, a 40-ml sample is spun to 34.8 Kg forces to accelerate the separation of insoluble compounds. The sediment is compared to a visual rating scale ranging from 1 to 8, where 1 represents no to low insoluble levels, and 8 represents high levels. A second step may include the measure of the residue with FTIR to differentiate between insoluble atmospheric and degradation contaminants and further characterize the oxidation species present.
Membrane Patch Colorimetry (MPC–ASTM–Draft) is a generic, in-plant test that is used to measure the color bodies of insoluble contaminants in lubricants, primarily circulation oils. This test uses solvent extraction to capture varnish and oxide insoluble contents from a fluid sample on a .4 micron filter-membrane. The color spectra of the insolubles collected can be correlated to the amount of oxidation byproducts in the oil. The insolubles are analyzed with a spectrophotometer and with the total amount of color expressed in the CIE LAB scale as ÄE. The hue of the patch is correlated to the varnishing tendencies of in-service turbine oils, which are directly related to the lubricant’s declining oxidation resistance. A rating of 40 or greater suggests that the varnish concentration is growing and a response is warranted, as shown in Figure 4.
Figure 4. Example patches and values from the Membrane Patch Colorimetry (MPC) test. A value of 50 would be cause for concern in any servo-valve application and suggests that the lubrication system may already be coated in varnish. A result of 9 would be considered normal. (Courtesy of Fluitec International)
MINIMIZING THE FALLOUT
Controlling the consequences of oxidation degradation (deposits, varnish and residue formation) begins with controlling the oxidative processes within the system.
The pro-oxidants are well known: heat, water, air, metals and soluble gases. Eliminating any of these root cause contributors adds appreciably to the long-term health of the lubricant. For hot machines, such as combustion and gas turbine engine applications, heat is often the primary pro-oxidant. Where heat-removal options are limited, given system design, flow and sump size, short lubricant change intervals are expected.
Where the sumps are large enough to justify the cost vs. frequent oil changes, electrophoresis and electrophysical (via ion exchange) separation techniques allow the machine owner to remove oil waste and extend lubricant lifecycles without risk to production machinery.
Electrophoresis is an approach that uses charge attractions to trap high molecular weight insoluble compounds. Plates with a given charge contact the oil stream carrying insolubles holding the opposite charge and, as shown in Figures 5(a), 5(b) and 5(c), the charged waste particles are attracted and fix to the surfaces with the opposite charge. The charged waste residue becomes trapped at the surface of the charged plate.
Figure 5. Charged waste particles attracted and fixed to surfaces with opposite charge. (Courtesy of Fluitec International)
Electrophysical separation incorporates the use of specially treated resins designed to attract charged soft particles. Figure 6(a) shows the effect of degradation byproducts in contact with an individual resin, and Figure 6(b) implies the cumulative impact of resin bed scrubbing.
Figure 6. (a) Individual charged particles bond to treated resin beads, (b) The resin bed scavenges degradation byproducts from the flowing oil. (Courtesy of Fluitec International)
SUMMARY
Oxidation is the process through which lubricants chemically change by incorporating oxygen. Oxidation is a general term used to denote chemical degradation of lubricants. Oxidation accelerators include air, moisture, catalytic metals and heat.
Additives are selected for the chosen basestocks to help stop, or at least postpone, oxidation. Once antioxidant additives are consumed, oxidation can continue unabated. FTIR and LSV methods can be used to identify additive depletion. Ultra-Centrifuge and Membrane Patch Colorimetry (MPC) can be used to measure for the evidence of oxidation and chemical degradation. The degradation compounds may be removed with specially designed electrophoresis and electrophysical filtration systems.
REFERENCES
1.
Wooton, D., “The Lubricant’s Nemesis—Oxidation,”
Practicing Oil Analysis, March 2007.
2.
Kramer, D.C., Lok, B.K. and Krug, R.R., “The Evolution of Base Oil Technology,” Turbine Lubrication in the 21st Century, ASTM STP#1407, W.R. Herguth and T.M. Warne, Eds., American Society of Testing and Materials, West Conshohocken, Pa.
3.
IBID.
4.
Schwager, B., Hardy, B.J. and Aguilar, G.A., “Improved Response of Turbine Oils Based on Group II Hydrocracked Base Oils Compared with those Based on Solvent Refined Base Oils,” Published for the Turbine Lubrication in the 21st Century—reference document for the ASTM D02.CO Turbine Oil Symposium, Seattle, Wash., June 26, 2000.
5.
Deckman, D.E., Lohuis, J.R. and Murphy, W.R. (1997), “HDP Base Stocks for Industrial Lubricants,”
Lubricants World, pp. 20-26.
6.
IBID.
7.
Gatto, V.J., Moehle, W.E., Cobb, T.W. and Schneller, E.R., “Oxidation Fundamentals and Its Application to Turbine Oil Testing,”
Journal of ASTM International, 3 (4), April 2006.
8.
IBID.
9.
Livingstone, G.J., Thompson, B.T. and Okazaki, M.E., “Physical Performance and Chemical Changes in Turbine Oils from Oxidation,”
Journal of ASTM International, 4 (1), January 2007.
Mike Johnson, CLS, CMRP, MLT, is the principal consultant for Advanced Machine Reliability Resources, in Franklin, Tenn. You can reach him at mike.johnson@precisionlubrication.com.
Matt Spurlock, CMRP, MLA II, MLT I, LLA I, is the machine lubricant subject matter expert at Allied Reliability, Inc., in Indianapolis, Ind. You reach him at spurlockm@alliedreliability.com.