When alligators bite
Peter A. Oglevie | TLT Shop Floor December 2009
Advance planning can go a long way toward keeping lubrication beasts at bay.
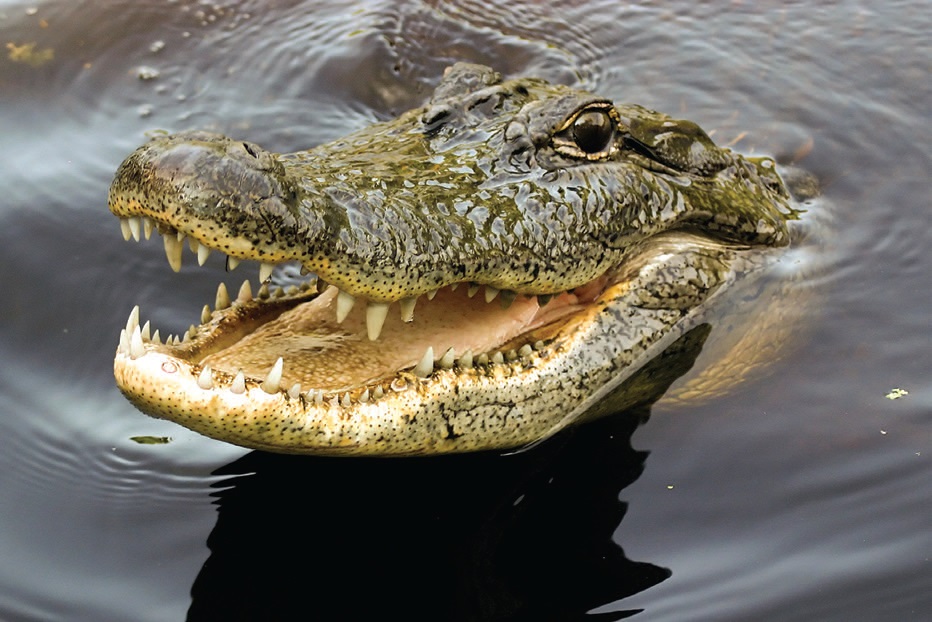
Unless your customer recognizes and accepts that he has a problem, you can’t eliminate or reduce it.
www.canstockphoto.com
The other day I was working on a major project at my house when I was reminded of the old adage: “When you’re up to your elbows in alligators, it is hard to remember that your original intent was to drain the swamp.”
My swamp is my side yard where I am putting in a driveway/patio that also will drain the side yard year round. Winter is approaching, and the job must be finished soon. If not, I have to pay $15 a month and walk a block to a parking lot while Swamp Oglevie forms in the spring.
I did my homework. The drainage is engineered, the base compacted and the sand is ready. All I have to do is lay the pavers. Rain is my only (and persistent) issue, which reminds me of a major problem I encountered on the shop floor.
I worked in two plants that produced severe metal-forming parts and battled rust every year from mid-April until mid-September. Specifically when the temperature reached 90 F and humidity 85%, their parts would rust.
The two plants shared some common issues. Both used heavily chlorinated products and operated in high-humidity, 90 F environments.
At the first plant I worked with the engineer, Don, who recognized he had a rust problem and wanted to eliminate a pickling operation from the process. He asked me, “What can we do?”
Don modified his tools and process and even considered finding a company to supply an air conditioning system in the press room to control the climate in the building. He recognized the problem and did something about it. We did not eliminate the chlorinated product but were able to cut his use of it by 50%, which reduced his summertime rust significantly and also his process cost by eliminating the pickling step from many of his product lines.
Jim, a nice man, ran the second plant, but I could never get him to work with me. I would ask questions like, “How do you form your parts? What do you do after you form them? Do you paint? Do you encounter rust?” Jim kept telling me he did not have any problems.
One night I attended a Precision Metalforming Association dinner meeting and had an opportunity to talk to one of Jim’s co-workers, Ray. We talked about processes and how one part of the process can affect the next. Ray told me about his rust problems. He had a warehouse full of parts that needed to be pickled to remove rust before painting.
I stopped to see Jim again and brought up the conversation with Ray about rust in the warehouse. He told me, “It is not my problem. I made the parts and they weren’t rusty when they went into the warehouse, so the problem is the warehouse.”
Two years later, after Jim’s retirement, I stopped by and, as expected, Ray asked what could we do to reduce his pickling cost. We reduced the use of chlorinated product and adjusted the process by adding a wash and inhibiting step to eliminate the need for pickling. The cost per part dropped dramatically. This plant could have saved $30,000 a year if Jim had recognized the rust problem as curable.
My point is that unless you recognize and accept that you have a problem, you can’t eliminate or reduce it. Start working on next summer’s rust problems this winter.
If I had started the driveway project in the spring I would have eliminated my problems in the fall. I would not be up to my elbows in alligators now.
Pete Oglevie is president of International Production Technologies in Port Washington, Wis. You can reach him at poglevie@intprotec.com.