Extending lubricant life
R. David Whitby | TLT Worldwide November 2009
Controlling operating temperature of the lubricant is important to minimizing oil oxidation.
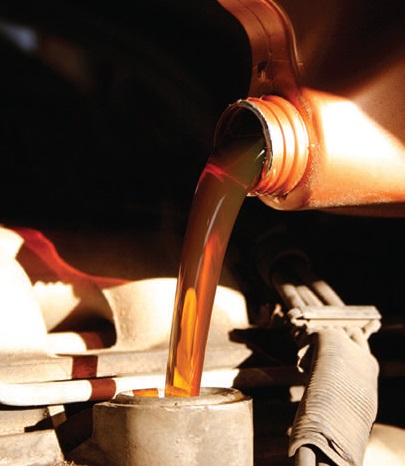
As oil oxidizes in service, there is a tendency for it to become more acidic.
www.canstockphoto.com
The nature of lubrication is that lubricants deteriorate in service. This can be either planned and controlled or uncontrolled. Good lubrication practice is strongly focused on the former.
Following are several factors that affect the useful life of a lubricant:
•
Oxidation
•
Thermal degradation
•
Contamination
•
Foaming
•
Air-release
•
Demulsibility.
By far the most important of these is oxidation, which happens because oils and greases are in contact with and, in fact, can contain up to 10% of air (except when they are used in space). Oxidation cannot be eliminated; it can only be minimized. It depends on the degree and duration of exposure to air, temperature, the presence of catalysts (iron, copper, lead), the rate of oil top-up and the type of base oil and oxidation inhibitor(s).
Temperature has the biggest effect on oxidation, which is a chemical reaction that follows the Arrhenius effect. Oxidation reaction rates double or treble for every 10 C increase in temperature. Thus, a reaction rate of unity at 70 C will increase between 2 and 3 at 80 C, between 4 and 9 at 90 C and between 8 and 27 at 100 C and so on.
This has very important implications for lubricant lifetimes. For example, if a hydraulic oil has an operating lifetime of four years if the bulk oil temperature averages 70 C, the lifetime will be only two years (or less) if the temperature averages 80 C, one year if it is 90 C and only six months (or much less) if it reaches 100 C.
Controlling the operating temperature of a lubricant is, therefore, particularly important. Occasional spikes in temperature are less important than average temperature of the bulk of the oil. Because oils contain air dissolved or entrapped within them, the mechanical movement of the lubricant—as flow, agitation or foaming—will maintain the air/oxygen concentration in the oil and increase the oxidation rate.
An oil’s natural oxidation stability is determined in part by the crude oil from which it is made and the refining process to which it is subjected. API Group I base oils have some natural stability toward oxidation due to the small amounts of sulphur compounds they contain. Group II and III base oils and synthetic hydrocarbons (such as polyalphaolefins) have less inherent oxidation stability, although they are much more responsive to oxidation inhibitors (antioxidant additives).
The rate of oxidation of a lubricant can be slowed dramatically with oxidation inhibitors, so almost all lubricants now contain them. The reserve concentration of unused, effective antioxidant in the lubricant during its service life is a crucial factor. Exhaustion of the antioxidant rapidly leads to the mechanical deterioration of the equipment.
As oil oxidizes in service, there is a tendency for it to become more acidic. Hence, measuring an oil’s acidity at regular intervals and plotting the results can be used to follow the progress of oxidation. However, neutralization number determinations may have little significance for some oils containing additives, which either contain weak acids or weak bases or which react with products of oxidation.
Slight oxidation is not harmful, but if the oil has poor resistance, oxidation may become excessive. If this occurs, substantial amounts of both soluble and insoluble oxidation products are formed, and the oil gradually increases in viscosity. Some variation of viscosity within a range that has proved satisfactory in service is not necessarily harmful. However, viscosity higher than necessary is accompanied by higher fluid friction and more heating. Obviously, this can lead to higher rates of oxidation.
Modern lubricants must withstand higher operating temperatures using smaller volumes for longer service intervals. Advanced lubricant formulations are required, which can operate at consistently higher temperatures to prevent their deterioration below levels that protect operating equipment.
Minimizing oxidation by reducing operating temperatures, avoiding excess exposure to air, filtering out metallic particles and using high quality base oils and additives is probably the most effective way of extending lubricant life.
David Whitby is chief executive of Pathmaster Marketing Ltd. in Surrey, England. You can contact him at pathmaster@dial.pipex.com.