Describe your greatest triumph or happiest day as a lubrication engineer or tribology researcher.
TLT Sounding Board October 2009
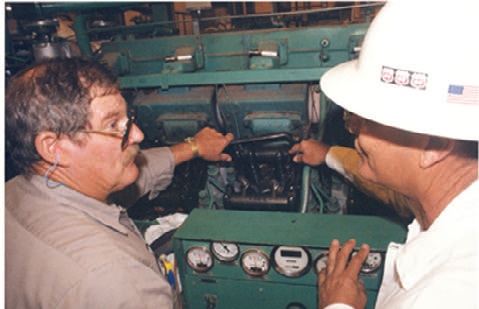
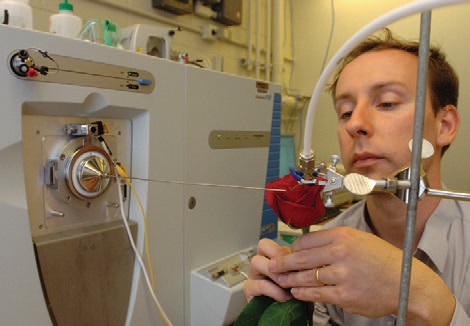
TLT readers tend to come in two varieties—those involved in the manufacturing and marketing of lubricants and those involved in tribology research. The No. 1 answer for those involved in the practical applications of lubricants, by far the larger of the two groups, was obtaining their CLS certification from STLE, many of them especially proud that they passed the test on the first try. The No. 2 answer from this group was solving tough lubrication problems for their customers. In some cases respondents said they prevented a plant closure or saved millions of dollars for their customers. Researchers cited the acceptance and respect they received from having their work accepted and published. Survey respondents presented an overall sense of satisfaction and optimism in their work, perhaps best expressed by the reader who said, “Most days are happy days, as they often bring excitement of new discoveries and applications.”
One of the greatest challenges when implementing our lubrication program was changing the culture of the workforce and management. When the program was first implemented there was resistance to change. However, as the program components became more visible and the site was rewarded with the benefits, acceptance came more easily. It’s gratifying to see that acceptance on a plant-wide basis.
Attaining my CLS accreditation.
The day I landed a multimillion dollar customer with a newly developed lubricant.
My happiest day was the one in which I was offered a research position with my current employer.
I have had quite a few. Landing certain customers by solving their problem and retaining them for many years.
Any day I can solve a customer’s tribology problem.
Beating a competitor’s material by a wide margin!
Finally convincing a plant engineer that his foam issue was a worn out pump and not the lubricant.
Obtaining my CLS.
I received the PM Ku Award in 2009 at the Annual Meeting with my wife present.
My first patent.
Solving problems with sticking of governor proportional valves of the hydropower equipment.
I have had many wonderful moments meeting fellow tribologists from around the world, sharing and delighting in our special secrets—a great community with wonderful people!
My first hire date.
Getting a call from a customer who thanked me for providing information that solved a major problem on the production line.
Obtaining my first patent.
The day I helped my first customer solve his lubrication dilemma.
My very first presentation to a customer where I, although I was younger than most everyone in the room, was the expert.
I was extremely satisfied to ship a custom-ordered forklift with $500 per gallon silicon-based hydraulic fluid. This oil has the best viscometrics available in a hydraulic fluid and was a requirement for the nuclear facility where it was installed.
This came in my past life when I was a nuclear propulsion mechanic on a submarine. I received a high-level award from a vice admiral (when I was the “oil king” on my boat) for a highly successful lube-loading operation. It also noted my cooperation with a Dutch sub in our port, so that they could perform a load as well (and they left with my special fitting... still bugs me to this day!).
Starting the program here at this facility.
The launch of new products and issuance of patents when I was the main inventor.
Passing the CLS exam on my first try. Passing the OMA exam on my first try.
Finding a chemical solution to a customer problem that resulted in new business for my company as well as a new market area.
When I had been working for two years to make a long sump life semisynthetic additive base package and got the results I had been looking for.
Refitting pressure dam journal bearings to a 500-mw steam turbine that solved bearing wear and vibrations problems. Likely saved over $4 million.
When I got my job here at Georgia Tech.
Making a positive impact on the company through the application of better lubrication practices.
Seeing sales people develop into professional lubricant problem solvers.
Completing the lubrication survey in a large paper mill that was conducted during construction over a period of two years and then implementing a lubrication scheduling program utilizing the information from the survey.
Recommending to a cement plant that they convert the plant’s lubrication storage and handling to a world-class system. They did, and it’s paying dividends.
Watching a new bearing operate successfully.
Starting an oil analysis program at a cement plant in the ’80s and going back 20 years later to see what it had developed into.
I’m brand new to the field. The greatest triumph was attending a seminar on optical profiling where a guest speaker discussed the connection between surface morphology and friction. I had an “ah hah” moment, realizing we needed to learn more about friction between interfaces.
Any day we can solve a lubricant problem.
Solving major problems and developing new products that generate income for my company.
Selling a new account with a technical sale.
Finding the root cause for a pump failure that eluded many before me.
Saved a major auto plant from shutdown due to robot failure. Through a grease analysis, we solved the problem.
Developing and applying new technology to modern industry applications such as changing from Group I to Group II base oil in gas turbine applications.
The greatest triumph was earning my CLS certification.
Winning that first big account with a lot of work from a major competitor.
Seeing the expression of amazement when the teardown of a hydraulic system operating on a new synthetic fluid I developed revealed only the original grinding pattern on the swash plate. The non-believers became believers that day.
Getting my CMFS certification.
Being awarded the lube business at a copper wire plant after doing my first equipment survey. It was 18 years ago, and it is a fond memory—even if I barely knew what I was doing.
When I became an STLE Fellow.
The day that best practice oil sampling and action tracking of results came together with practical knowledge of equipment components. The realization that knowledge in one area was incomplete without the other was a triumph. If you don’t know what’s broke you do know how to fix it.
How long have you been involved with the lubricants industry or tribology research?
1-5 years
16%
6-10 years
13%
11-15 years
12%
16-20 years
16%
More than 20 years
43%
Based on results from 172 respondents.
Successfully convincing a large coolant user to go with coolant management.
Completion of the GF-4 synthetics program.
Every day selling lubricants is exciting!
The day we discovered a biobased additive and found it doing its function of reducing wear.
Troubleshooting and solving a lubrication flow system causing overheating, due to a collapsed oil filter.
Redesigning the support wheel bearings of a 250-ton steel-making vessel.
Developing an understanding of wax crystal effects on low-temperature engine oil testing.
Every day is a great day. Researching in tribology is a great experience.
When I passed the CLS exam.
The additive I developed helped in reducing friction and wear in a drawing application significantly!
Passing the CLS exam on the first try.
Changing the lube specs on a series of rotary furnace bearings that operated at about 260 F. We increased the bearing life from six months to more than 10 years at no change in maintenance cost and got a huge increase on stream time.
Having a technical paper of mine chosen as an Editor’s Choice paper in TLT.
Verification of life expectancy of a ball bearing lubricant.
Upon reflection, there have been many happy days due to very different events. A breakthrough on a tough lubrication problem, seeing former students go on to do great things and professional recognition by peers. Perhaps the reason this question is difficult to answer is cause for celebration in itself.
The day I passed the CLS exam.
Landing large accounts.
Working with a customer to develop a new basestock.
Converted a customer from old technology to my newer technology.
Every day that someone calls and thanks me for the advice I gave them.
When a product is finally launched after a long period of careful product development and testing.
Still looking forward to finding it. It may be when I land my biggest account.
The day the diester cleaned up the additive residue.
Research on lubrication fundamentals at NASA Lewis Research Center in Cleveland, Ohio.
Starting a new job at Company Y after Company X decided they no longer needed me.
Finding a surprisingly unusual way to study the general and molecular interactions of gases and fluids in the process of air entrainment.
When I invented Tango-class air bearings for hard disk drives.
Solving a truly perplexing lube problem.
Having my research work recognized by peers and implemented on applications.
Developing additives that are environmentally safe and high performance.
Please describe your academic credentials.
High school
12%
Bachelor’s degree
44%
Master’s degree
18%
Doctorate
26%
Based on results from 172 respondents.
My happiest days were after I switched my car from a 5W-30 (popular full-PAO base oil) to a 0W-30 (at the time only a synthetic blend) and realized a 10% increase in fuel economy, going from 30.5 mpg to 33.6 mpg per tank. This data was based on two years usage and tracking of 5W-30 and then five more years on 0W-30, supported by oil analysis done at each 4,000-mile oil change.
Solving a costly problem with metalworking fluids for my client.
Increased the useful life of internal combustion engines by 200% (fleet maintenance with oil analysis).
In 1993 we launched Australia’s first large-scale oil recycling company with the support of the Victorian government.
Finally developing a model that I could use to explain to others how fluids work at the point of cut.
Making a presentation during STLE’s 2009 Annual Meeting & Exhibition in Florida.
Avoiding replacement of a $2 million gearset by checking the viscosity with routine oil analysis.
Receiving the acceptance letters from
Tribology Letters or
Wear for papers written in these industry-specific journals. It gives us some real sense of worth.
Our presentation at a major customer went very well.
Passing the CLS exam.
Established lubricants programs in three different industries that I have worked for. Programs initiated in the oil, automotive and steel fabrication industries that formerly had no structured programs including oil analysis. In all cases they resulted in reliability improvements.
Solved a very perplexing problem for a customer.
Receiving the OMA certification from STLE.
Having the knowledge to overcome friction in sticking diesel injector needles by using long-chain fatty acids.
Coming up with an oil formulation which passed a difficult fuel economy engine test.
Successfully applying an ultrafine filtration system on a coal pulverizer lube oil system that produced economic benefits.
My happiest day is yet to come.