Kill the buggers
Peter A. Oglevie | TLT Shop Floor October 2009
Total ruthlessness is needed when bacteria, mold and fungus contaminate your metalworking fluids.
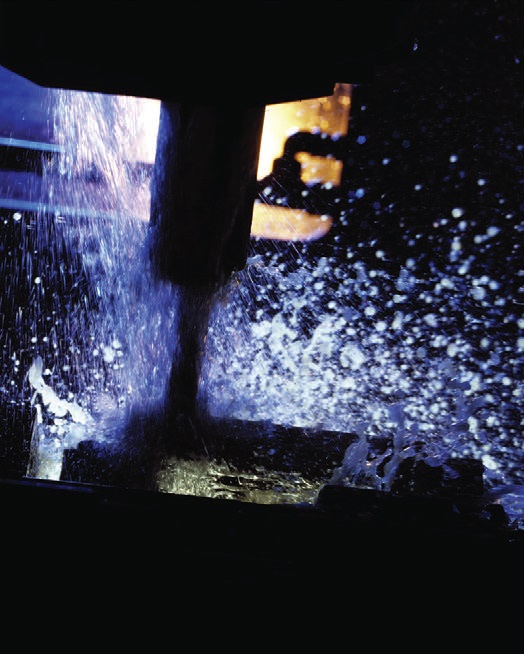
Treating the fluid does not necessarily mean you treated the system.
www.canstockphoto.com
As a sailor I hate the words “what if?” For example, what if the weather was better? What if our winds were lighter? What if the bottom of the boat is clean and friction is reduced to a minimum?
I crew on a sailing team and over the years the EPA has restricted the use of some paint additives that are effective in reducing the growth of algae on the wetted surfaces of the boat. These days, even while using the best-bottom paint available, we find moss growing on the bottom of the boat. We have to physically scrub the moss off before each race to reduce friction.
Much of what we learn carries from one aspect of our lives into another. In this case, I should have learned better from my shop floor experiences in dealing with coolants.
Biological contamination of metalworking fluids is often the limiting factor in determining the lifecycle of a coolant. If it becomes too contaminated with bacteria, mold or fungus, it is time to discard the fluid. It makes no sense to put clean coolant into an improperly prepared coolant system. The cleaner the system the better.
I have seen new coolants fail in the field not because they are bad but, rather, because some part of the system was not properly prepared before the coolant was put in. Just as our race finishes have improved after scrubbing the bottom of the boat, I have had more success with metal-removal fluids following a thorough cleaning of the system.
The biological attack on metalworking fluids is a lot like the algae that grows at or below the waterline of the boat. Mold in particular gets everywhere on the machine and just about anywhere around the machine that stays moist. It grows in places like the bottom of machine beds and tank covers where the fluid does not flow. Treating the fluid does not necessarily mean you treated the system. If you do not take the time to pull the cover off and physically remove the mold, it will just reinfest the system.
Following are recommendations for a three-step cleaning of the coolant system.
1.
Remove the filters, tank covers and auxiliary equipment from the machine. Shovel out the solids (metal fines) and remove the old coolant from the system. Install a detergent to wash down the machine, especially the undersides of the bed and tank lids. Drain the system of the detergent and make sure to remove all residues from the tank and lines.
2.
Add a sterilizing agent (mixture of biological preservatives) to the system and circulate to kill any residual colonies and remove it from the system. Kill the buggers. If you do not, they will come back. When you think the system is clean, clean it some more.
3.
Reinstall clean filters, auxiliary equipment and fill the system with fresh coolant. Flush the machine with fresh coolant to prevent flash rust. Pull a sample immediately to establish your efforts have been effective. If there is any biological activity, treat immediately. No more “what if?”
Does it matter? When I scrubbed the bottom of the boat before our last race, I had a bad day in the water. The water was 60 F. I lost my kitchen mop when it sank to the bottom. My scrub brush floated away, so I did not get the propeller scrubbed. We ended up finishing the race in third place, six seconds out of second.
In our next race, I intend to have my cleaning equipment in order, including backup scrub brushes. I will get my kitchen mop back and clean that propeller.
No more “what if” for me this season. I plan to mop the kitchen floor, too.
Pete Oglevie is president of International Production Technologies in Port Washington, Wis. You can reach him at poglevie@intprotec.com.