What’s the point?
Jack Poley | TLT On Condition Monitoring September 2009
The right experience can help solve tough problems in evaluating oil analysis data.
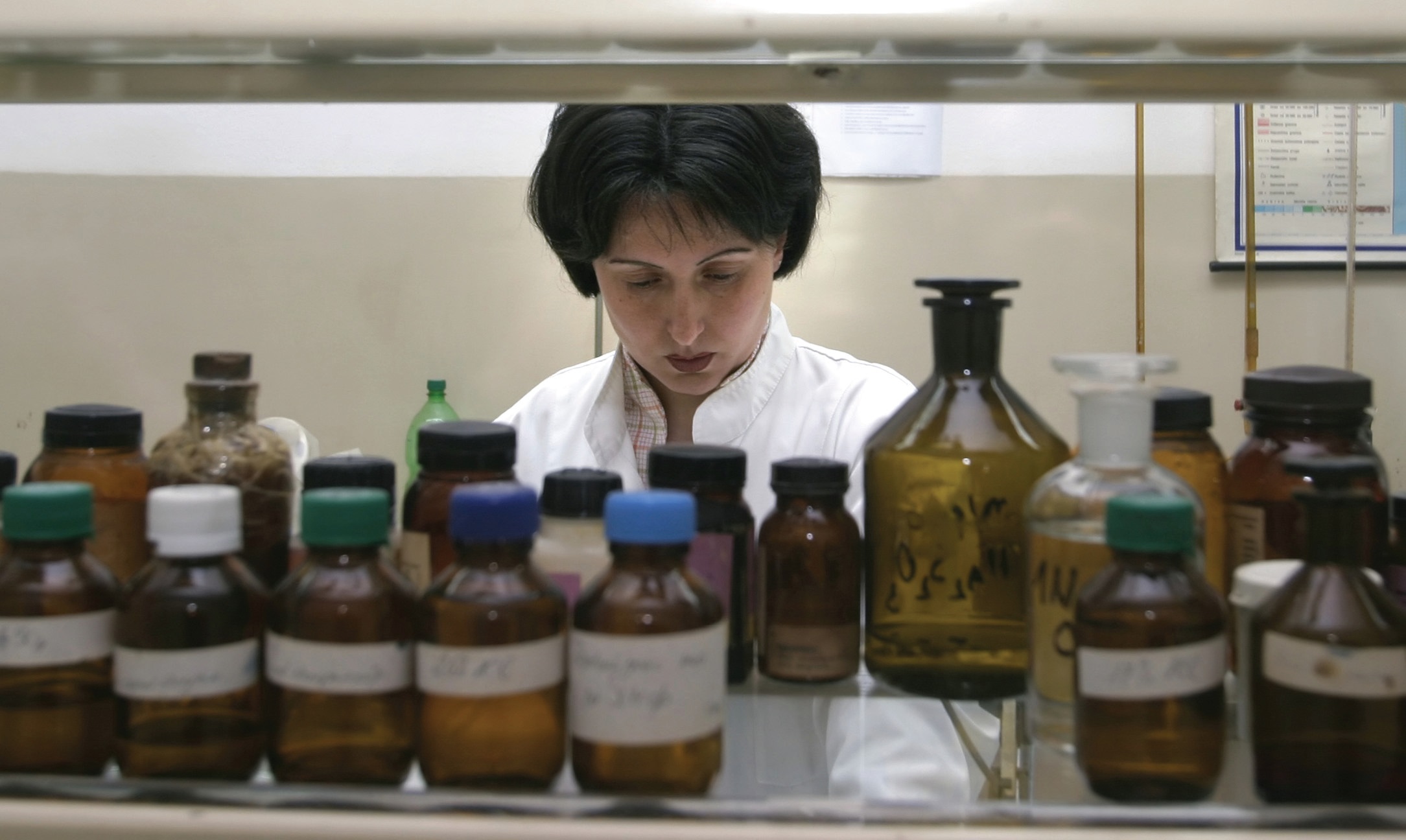
Evaluating oil or vibration analysis is like detective work.
www.canstockphoto.com
We call it “oil analysis” and, as I’ve often noted, it’s a bit of a misnomer—actually, more than a bit to me. Following is a short quiz for which (suggested) answers have appeared in previous columns:
The purpose of oil analysis is to:
a. Garner pertinent data
b. Make, preserve or conserve money
c. Extend lube drains with minimal risk
d. Make timely, useful maintenance and equipment utilization decisions.
The answer is “all the above,” but if one adds the word: “primary” before “purpose,” the answer is (b.) To make or preserve money.
Making money has to do with keeping production at maximum levels. Preserving or conserving money has to do with extending lube drains prudently or taking equipment offline for service (so it can quickly return to making money) before a major failure, thwarting our conservation plan (and squelching the equipment’s ability to make money).
So oil analysis is about money. Everything else is secondary (for altruists concerned with safety, money also applies, does it not?). And the question is rhetorical. Everyone already knows the answer, but it is puzzling to see so many unwilling or unable to avail all the potential benefits of oil analysis. As I’ve also noted, the monetary benefits from oil analysis are so great that it is relatively easy to be satisfied with the low-hanging fruit aspect, i.e., so long as a modicum of savings is deemed realized, the program is deemed justified, case closed, ROI calculations obviated.
One can and should do better than this.
What do we expect or want from an oil analysis?
a. Accurate data
b. Commentary to help us understand the data
c. Commentary to advise us “what to do or not do”
d. A timely report, fast turnaround.
Again, “all the above” works nicely, but if one rephrases this question to: “What must the analysis lead to in order to make or save money?” Answer: (c.) A decision to act or not act that is ultimately proved correct.
One might ask the question, “What prompts this decision?” Answer: An informed evaluation of the data in the context of past testing history and the machine involved.
So we come to the point: oil analysis, i.e., the garnering of data via testing, is a means to an end. And
the end of the process is an evaluation that will be used to make a decision designed to make or conserve money.
Who’s going to perform this evaluation? Hopefully some highly qualified people, preferably armed with software to assist them, lest they miss something. Sometimes the data speak rather directly, and most report recipients with little experience could easily form their own conclusions in such instances. For example, say a gearbox is supposed to have ISO 68 viscosity product in it, but the viscosity tests at ISO 32. It is highly likely the wrong product was used to fill the gearbox. There is the possibility that someone topped off the sump with a solvent out of ignorance or maliciousness, however, that’s a rare event.
In either case, draining the out-of-spec product and refilling with the correct product is the short-term answer, with the hope that excessive film penetration didn’t occur from the thinner product, causing abnormal wear. Subsequent testing, or perhaps some precautionary diagnostics, will answer that question.
The Evaluation Quotient (EQ) gets a tad trickier if a diesel engine oil is being tested and found to have a significantly low viscosity. Here is another candidate for such an occurrence: a fuel leak into the crankcase, thereby thinning the oil. To rule this out (or in) one would want a fuel dilution test of some sort. There is yet another possibility for the diesel engine vs. the gearbox using a straight-grade product: the viscosity index improver that is almost always a component in a diesel engine oil. Perhaps that additive’s molecular structure was attacked by way of molecular shearing, resulting in viscosity loss.
Even with all these possibilities, the exercise of sorting out the actual problem is not difficult (again, ruling out the possibility of sabotage). While we’ve listed three possible causes for low viscosity: fuel, shearing and wrong oil added, experience should tell us that fuel dilution is the most likely problem, particularly if the viscosity has dropped precipitously. If we have fuel dilution by volume in our testing package, we’ll know if fuel is the problem. If so, we’ll ask the mechanic to drain the lube, change the filter and diagnose and repair the fuel problem.
Now it’s the mechanic’s turn to evaluate. If he’s been informed that a fuel leak is likely, he knows, from experience, where the most likely root cause is for that occurrence in the particular manufacturer and model under review. He will start there first, moving on to the next likely candidate: perhaps he starts with fuel delivery jumper lines, then injector seals and moves to the fuel pump.
If the mechanic comes short of finding a problem, he may move to the next most likely cause for low viscosity: shearing or wrong oil added. If none of those is found to be at issue, he may very well contact the lab and ask if the viscosity could be retested, lest it might have been misreported. The lab likely will be lucky in this case because low viscosity and high fuel dilution are partners to a commonly occurring problem, and it’s not too likely the lab messed up on two unrelated tests, which means the mechanic will probably need to comb the possibilities yet one more time.
When I first entered the oil analysis realm decades ago, this kind of collective, systematic reasoning was rare (and it’s not always employed today, necessarily). A brand new industry was upon us, and we needed to get some comfort level with the test results as to what was reasonable and what wasn’t. Often recipients of reports showing high fuel dilution would diligently change the oil but not take any action to prevent the problem’s recurrence. Besides, oil was cheap, and draining for almost any reason or finding was rather common. It took awhile for report recipients to understand the wealth of information that the report potentially contained, even though the data were in plain sight. Evaluation skills were missing or incomplete.
The scenario regarding the diesel engine above is a process I call primary and secondary (or tertiary) evaluation. The evaluator employed by the lab (whether on premises or by a specialist-for-hire) has identified the possibilities and probably speculated reasonably that a fuel leak was the root cause of the low viscosity. The mechanic knew precisely where to go to achieve the best chance of locating the problem, i.e., he applied his experience.
Evaluation of condition monitoring data (oil or vibration analysis) is every bit akin to detective work. Data are the primary clues, and the evaluation is the detecting or reasoning and deductive work to render an opinion and recommended action plan. It’s the subjective side of oil analysis, if you will, and it is best served via a systematic approach. I like to call that approach
spherical, i.e., from all directions.
In my next column, we’ll investigate some tougher, trickier examples.
Jack Poley is managing partner of Condition Monitoring International (CMI), Miami, consultants in fluid analysis. You can reach him at jpoley@conditionmonitoringintl.com.
For more information about CMI, visit www.conditionmonitoringintl.com.