The secret is in the formulation
Dr. Roger Melley | TLT Lessons Learned September 2009
Be sure to check all—and we do mean all—substances entering your chemical batch.
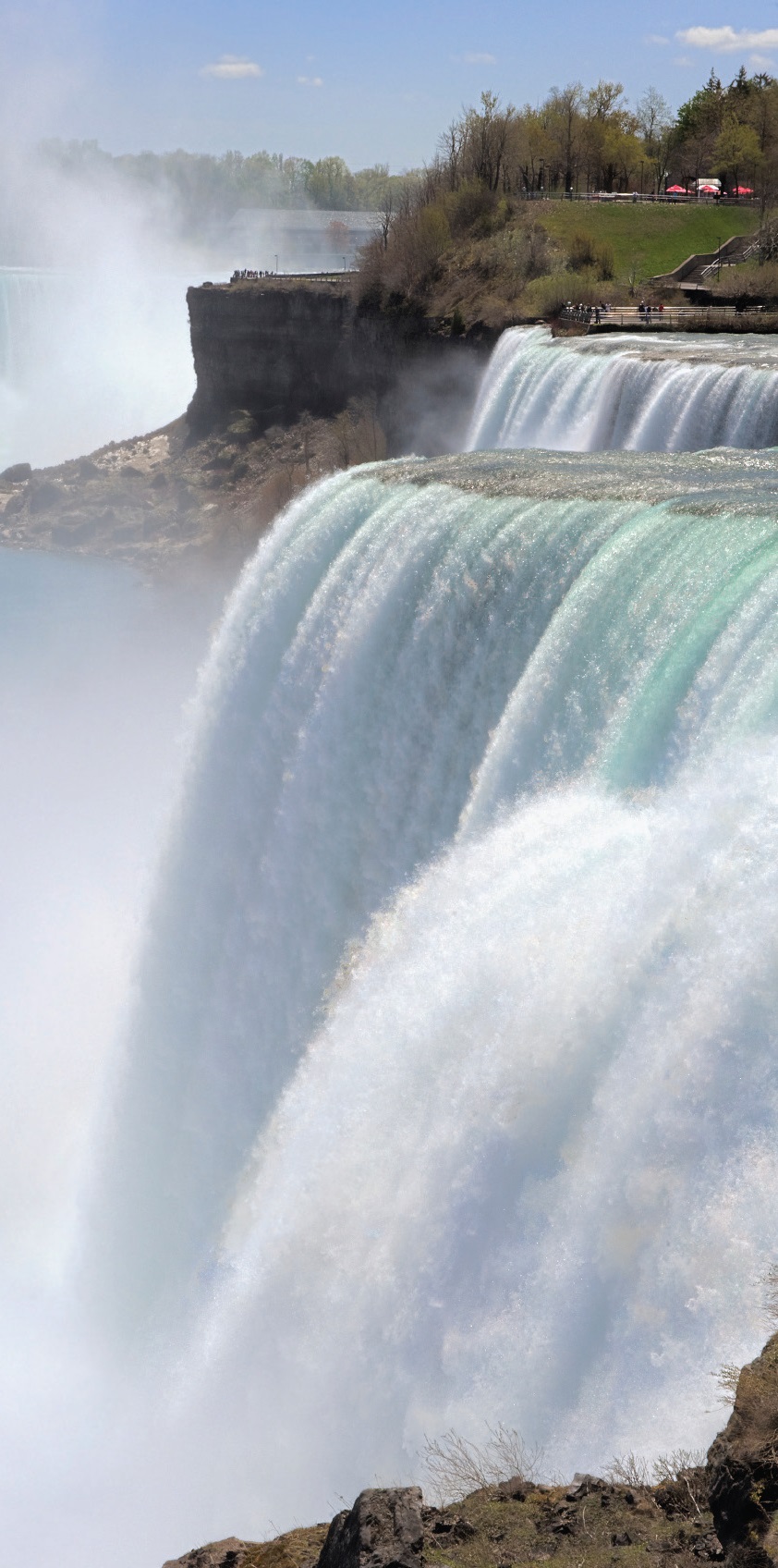
www.canstockphoto.com
Back in the early 1970s I was working with the research department in the chemical division of a multinational rubber company. In addition to running R&D programs, I provided technical service to our plants around the United Kingdom. I remember receiving a call from the technical manager of one of our plants in Scotland requesting help with a particular formulation. It seems that batches mixed on day shift had a tendency to just fail the technical specs, while those mixed overnight were always perfect. They had monitored operations and, as far as they could determine, there were no differences at all in the procedures.
I headed north and spent a few days at the plant checking all of the obvious areas—Banbury mixer charge sheets confirmed that all of the ingredients were added in the correct proportions, and the specified mixing cycles were used. A day in the QC Lab confirmed that all equipment was properly calibrated and that the QC technologists knew what they were doing. I double-checked sampling procedure, and there was nothing there that gave any cause for concern.
In the end, still totally bewildered, I decided to spend time with both crews to see if anything jumped out at me. The day shift taught me nothing, but the night shift was quite educational. A major rubber plant can be a lonely and dark place, particularly at night. I wandered around the mixing floor looking for clues and eventually found the answer.
The walk to the restroom was a significant one, so the night shift operators, when they felt the urge to urinate, used the copious mixing chamber of the Banbury rather than take a long dark walk. It didn’t happen often, they said, only three or four times a night. The ventilation over the unit was excellent, so there was no problem with odor and they probably didn’t see the bit of steam in the dark. I called the crew together and told them that this practice had to stop as it was having an effect on the rubber—I didn’t tell them that it was a beneficial effect.
The next morning I adjusted the formulation by upping the loading of staining antioxidant (amine based, of course) and told the plant management that I felt that change would eliminate their problem. The operation was closely monitored for a few weeks, and the problem did not reoccur.
My boss got a call and was told that for a youngster only a year or two out of the university, I sure knew how to formulate. My boss replied, “Well, his doctorate is in the field of elastomer chemistry.” Needless to say, I never told anyone the real reason why I made the formulation change that I did.
The lesson I learned from this exercise is that you should never assume anything in the real world. Many things can happen that you may be unaware of but which, if you did know about, you could monitor and/or control. So keep looking. I have to go for a walk now…
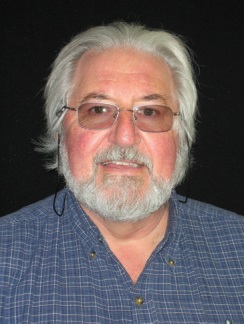
Roger Melley is phase separation section manager, Canadian Technical Services & Development, with Champion Technologies in Calgary, Alberta, Canada. You can reach him at roger.melley@champ-tech.com.