A blue moon for tribology
Dr. Christopher DellaCorte | TLT Guest Editorial July 2009
Nitinol 60 represents a rarity for lubrication purposes—a truly new bearing material.
Blue moons aren’t really blue, nor are they unexpected. A blue moon is simply a catchy way to describe events that don’t happen too often but are welcome nonetheless, like three-paycheck months, bank errors in your favor and leap years.
Since the length of the lunar and calendar months are slightly unequal, every two or three years we encounter a month with two full moons, hence the phrase “once in a blue moon.” In old days people used to joke that the moon was made of green cheese, and when cheese goes bad it turns blue.
In tribology, truly new bearing materials surface even less frequently than a blue moon. Decades typically pass between the emergence of new bearing materials. Silicon nitride was our last one, first emerging in the 1960s and ’70s and only recently realizing full commercialization. Sure, there have been others, like some high-performance stainless steels, but these are variations on earlier themes.
Now I am happy to report a recent occurrence of a tribological blue moon. Since 2004 my colleagues and I at NASA have been nurturing the development of a new alloy brought forth by the bearing industry that holds the promise for real improvements in tribological and mechanical systems.
This mystery alloy is immune to ferrous corrosion (rust), 20% lighter than steel, non-magnetic, electrically conductive, polishes to a Grade 5 or better finish and is readily machined before final hardening to Rockwell C60 or higher. No other bearing material known possesses all these attributes. Further, the industrial base needed to support its application already exists.
What’s most surprising, however, is that these alloys, named Nitinol, have been around since the late 1950s!
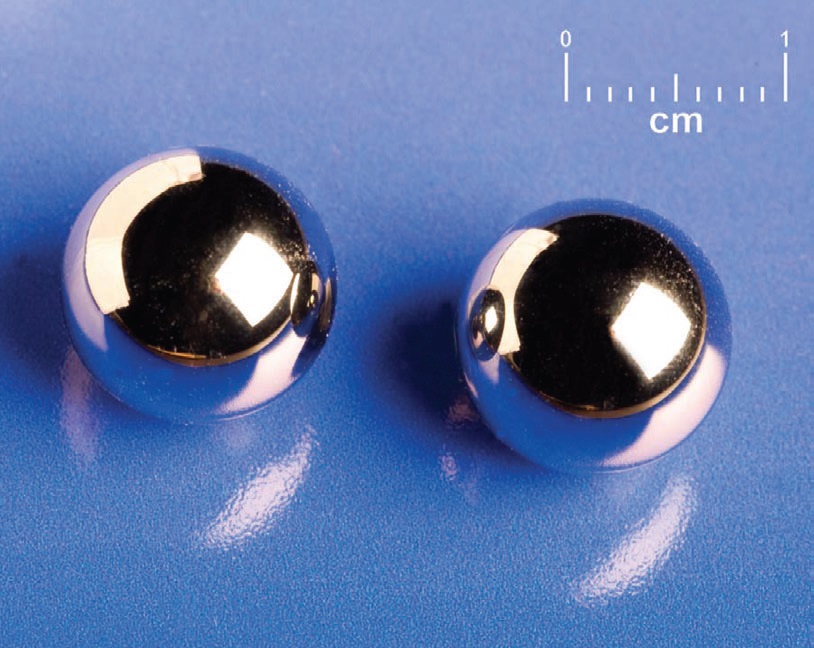
Two polished, half-inch diameter, Grade 5 Nitinol 60 balls.
Nitinol alloys, which typically contain equal amounts of nickel and titanium, are widely known for their superelastic and shape-memory effects. When plastically deformed and then heated, they snap back to their original shape—great for dental wires and arterial stents but not exactly the attribute one wants in a bearing or gear.
However, I’ve been working with a little known Nitinol cousin—nickel-rich Nitinol 60—that was originally intended for hardened, non-sparking bomb-disposal tools. It was abandoned decades ago as being too difficult to machine and fashion into useful components. New processing and fabrication techniques have since led to aerospace-quality bearing materials that are exhibiting excellent performance under lubricated bench tests representative of bearings operating in severe service. A paper has been recently published that describes this “new” alloy in detail (NASA TM-2009-215646, published March 2009).
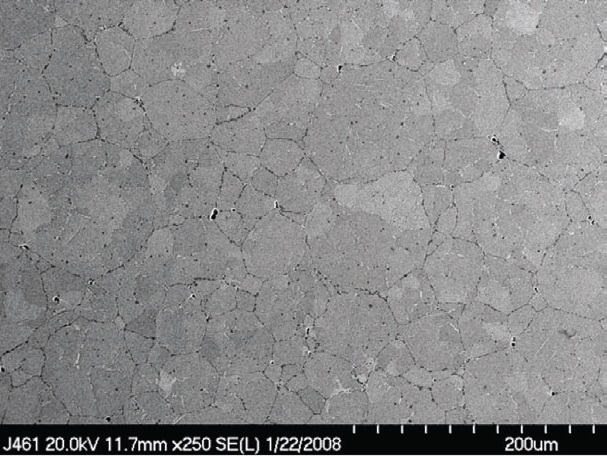
Cross section microstructure of Nitinol 60 ball.
With any luck, we’ll be seeing Nitinol 60 or its descendents added to our tribology toolbox for numerous applications in the years to come.
Please join me in taking a moment to enjoy the glow of this tribological blue moon.
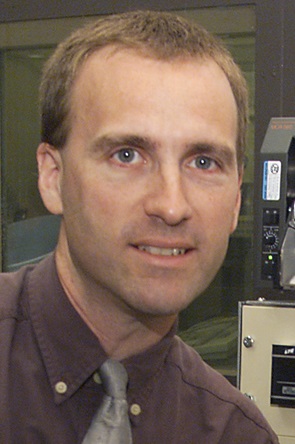
Chris DellaCorte is a research engineer with NASA Glenn Research Center in Cleveland. He is a member of STLE’s board of directors and was TLT editor from 2003 to 2007. You can reach him at christopher.dellacorte@nasa.gov.