The approval of seals
R. David Whitby | TLT Worldwide May 2009
You have many choices on how to keep the lubricant in the seal and dirt, dust and water out.
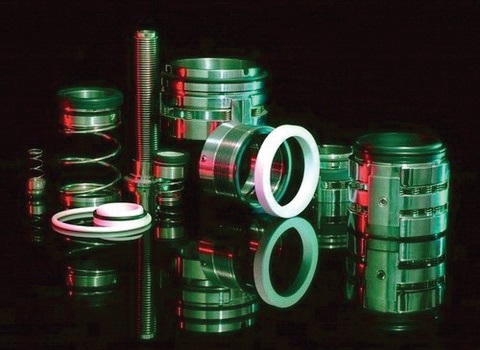
To function properly, seals must be of the right type, installed correctly, clean and free of defects.
www.canstockphoto.com
Seals are vital to the maintenance of operating machinery because they are used to keep the lubricant in and dust, dirt and water out. To function properly, seals must be of the right type, installed correctly, clean and free of defects.
Seals are classified as either static or dynamic. Gaskets and O-rings are examples of static seals. Dynamic seals such as lip, labyrinth and face seals are used between moving surfaces.
Lip seals are inexpensive but can be damaged easily, while labyrinth seals are expensive but long-lasting. For trouble-free operation and optimum service life of a lip seal, surfaces must have a satisfactory surface finish and correct geometry within recommended limits. Both correct design and material choice are critical if bearings and gears are to be sealed to prevent the leakage of lubricating oils and greases and the ingress of penetrating dust and dirt.
Mechanical face seals require a flushing system where abrasives may be present. Soft piston seals and O-rings may or may not operate under fluid film conditions. Additionally, material selection and seal life vary accordingly.
A labyrinth seal is composed of many straight grooves that press tightly inside a shaft so the fluid has to pass through a difficult path to escape. For rotating shafts, a very small clearance must exist between the tips of the labyrinth threads and the running surface. This provides a non-contact sealing action by controlling the passage of fluid through a variety of chambers by centrifugal motion, as well as by the formation of controlled fluid vortices.
With correctly designed labyrinth chambers, any liquid that escapes the main chamber becomes entrapped in a labyrinth chamber where it is forced into a vortex-like motion. This prevents its escape and acts to repel any other fluid. Because labyrinth seals are non-contact, they do not wear out.
Lip seals require lubrication—otherwise they will run hot, degrade and eventually fail. During rotation of a shaft, a hydrodynamic film of lubricant is produced beneath the sealing lip, the thickness of which depends on shaft speed, oil temperature, oil viscosity and the pressure or radial load exerted by the sealing lip on the shaft. Due to capillary forces and the surface topography of the shaft, the fluid being sealed forms a meniscus under the sealing lip and is prevented from leaking. The fluid, the seal material, the film thickness, the sealing lip geometry and the surface topography of the shaft are governing factors in realizing the capillary forces.
When lip seals operate with boundary lubrication, seal life is short. Temperature, relative velocity between seal and counterface, pressure, size, fluid compatibility and acceptable leakage rate influence the choice of seal. When lip seals are adjacent to bearings, the bearing lubricant will generally provide sufficient lubrication for the seal. However, in isolated locations, provision should be made for lubricant to reach the seal. Dual seals, where the space between the sealing edges can be prepacked with grease, allow sufficient lubrication, but the seals should be mounted so no pressure build-up occurs when adding grease.
Because the sealing principle of a lip seal relies on the friction between the sealing lip and shaft with a minimal fluid film, friction losses are inevitable. For a specific shaft diameter and speed of rotation, the friction coefficient depends on the friction of the seal with respect to the shaft. Factors that determine this include the seal’s characteristics, the shaft material and surface roughness, the presence and properties of the lubricant, the pressure of the medium to be sealed, the degree of interference of the sealing lip and the operating temperature.
Seal lubrication is important during assembly, as well as operation. A lip seal should never be assembled dry, as both the shaft and the seal need to be lubricated in advance. This eases assembly and ensures lubrication from the beginning.
Seals fail for numerous reasons, including poor lubrication, a topic I’ll discuss in my next column.
David Whitby is chief executive of Pathmaster Marketing Ltd. in Surrey, England. You can reach him at pathmaster@dial.pipex.com.