What was your most ‘extreme’ lubrication job?
TLT Sounding Board January 2009
In this issue NASA engineer Chris DellaCorte describes what has been called the most extreme lube job in history—greasing balky mechanisms on the International Space Station. The work was done last November by spacewalking astronauts 250 miles above earth while traveling at 17,400 miles per hour. While the majority of TLT readers aren’t involved in jobs with environments that severe, they have conquered some rather challenging lubrication problems in their own right. STLE members describe their most extreme lube jobs below. By the way, NASA doesn’t have to worry about finding volunteers for future missions. Nearly three-quarters of the 123 surveyed readers said that, if asked, they would happily pack up their grease guns the next time parts on the space station start squeaking.
The extreme conditions of the Arctic presents difficulty in selecting greases that will handle 90 F in the summer and -50 F in the winter.
Making hypodermic needles out of flat sheet of steel.
The most extreme lube job I’ve participated in was coming up with a successful deep-drawn part (complex shape, roughly 18 x 32 x 8 inches deep) in stainless steel. This involved a dry lube on selective areas of the blank in combination with a traditional high-pressure draw lube, also on selective areas of the blank, with some areas of the blank having no lube whatsoever—all of this combined with using particular materials for tooling based on their coefficient of friction.
The most technically challenging jobs involve racing applications. Torque reduction is paramount, so you are working with minimal lube quantities, minimal seals, high temperature (from brake heat soaking back) and extreme (very extreme) shock loading.
Open pit mine excavator, which is extreme due to the complexity and size.
I work in a rock bit company. The rock bit is used to drill the oil/gas well. I think the challenge is extreme for lubrication. You have limited amount of grease (5 ounces or so), extreme load (0.1 Gpa level pressure on bearing) and high temperature (300 F). This requires a best-in-class grease in terms of load capacity, thermal instability and friction performance.
Greasing a Cat D10 at a landfill.
Grease recommendations for applications that are exposed to significant radiation.
In the automotive business our toughest challenge is deciding where the economic pressure of cost crosses the quality line. In that regard our “extreme” job happens every time we launch a new product—will it be successful in the market?
A hot melt shop in a steel mill.
I had to prepare a forklift from our factory to go into a nuclear facility. The oil could not be hydrocarbon-based or else we risked another Three Mile Island scenario (if the oil mixed with the nuclear waste). We used a $500/gallon, silicon-based oil.
Nothing major—a fan over an oven at a foundry. They told me my grease was no good because the fan bearings were failing every couple of months. It apparently had nothing to do with the missing fan blades, which caused the shaft to wobble.
Changing the oil in my 2003 Corvette without jacking it up.
Mine ore crushers inside the cavernous LKAB mines in northern Sweden. This qualifies for extreme for size, bone-jarring power and raw beauty.
As lubricants become more technically advanced, do you think the job of a lubrication engineer is getting easier or harder?
Easier because we have better lubricants and machinery 19%
Harder because there is more to know than ever before 81%
Based on results from 123 respondents.
To maximize tool life by optimizing the lubricity and cooling properties of different chemical coolants (soluble oils, semisynthetics or synthetics) for various metal machining operations.
Lower bearing under oven fan at 2,100 F.
A heavily worn gearbox was producing such an amount of particulates that the filters got clogged with abrasive metals. We applied successive charges of coating in the lube until the situation stabilized in 3-4 weeks. The gearbox is still running, and it proved the advanced possibilities in tribology.
Planetary gearboxes for the rudder speed brake on the Space Shuttle.
The most extreme lube job I was even associated with was on a deep space communication antenna located at the Goldstone Deep Space Communications Complex at the Fort Irwin military reservation in Southern California. The largest antenna measures 70 meters in diameter and uses a hydrostatic lift mechanism. To point the antenna, a series of gearboxes are used in conjunction with other gearboxes trying to drive the antenna in the opposite direction. This solution removed much of the backlash inherent in gear systems and allowed for a dramatic improvement in pointing accuracy. I was called to troubleshoot a gearbox foaming issue that was plaguing the rebuild schedule of one of the antenna.
Fan motors that were inaccessible for about two years. They operated at 3,600 rpm in ambient temps near 200 F. We were lucky if the bearings lasted three years.
I live in Manitoba, Canada, where temperatures fluctuate between -40 C and 40 C within 12 months. Until you work in this environment, you cannot appreciate the difficulties regarding workplace lubrication.
Evaporation of base oil in a vacuum. Radiation caused degradation of the grease.
Lubrication of the equipment used to mine the tar sands in northern Alberta. Extreme cold, dirt, sand, snow, etc., make it a challenging lubrication application.
The most difficult lube job I performed was changing the oil on cooling tower fans, where the fan gearbox is 30 feet above the cell floor. Scheduling was mandatory. I had a crane lift two barrels on to the fan deck, one with new oil and one for waste oil.
A bearing housing that has powder dust on one side and high pressure water on the other. We’ve had to grease spillway gate chain links 50 feet underwater with divers in heated dry suits. With water around 35 F, we also had to warm the grease.
Lubricating cruise missile bearings for a one-hour lifetime.
Changing the oil in a main strut bearing on an SL-7 fast sealift ship.
Starting a cold-soaked aircraft auxiliary power unit (cold-soaked -40 F) without skidding the bearings or running too long without adequate lubrication.
Shortly after beginning our oil analysis program we discovered, through RULER analysis, that the life of the oil used in a vertical motor application was much less than had been anticipated. We had been routinely changing the oil once per year, but after the first test using voltammetry we found that the oil had a life span of only two months due to the severe operating environment. A change to a PAO synthetic oil has now increased the oil change interval to three years.
A “lubricant-less” bearing used in a military application that allowed no out-gassing of traditional lubricants.
Pin and bushings on large excavator shovels with bucket size around 25 yards and in temperatures down to -40 F in Alaska and up to 90-plus F in others. One shovel has an extension to give it approximately a 135-foot reach for a dredge on a dam and lock project on the Ohio River.
Lubrication of a thrust bearing supporting one million pounds of load in a diffuser rotating at 5 rpm. Impossible!
If NASA asked you to volunteer for a spacewalking mission where you would grease parts on the International Space Station, would you go?
Yes 72%
No 28%
Based on results from 123 respondents.
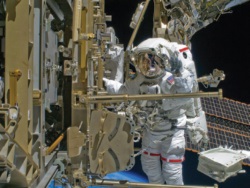
Editor’s Note: Sounding Board is based on an e-mail survey of 7,200 TLT readers. Views expressed are those of the respondents and do not reflect the opinions of the Society of Tribologists and Lubrication Engineers. STLE does not vouch for the technical accuracy of opinions expressed in Sounding Board, nor does inclusion of a comment represent an endorsement of the technology by STLE.