(higher % amorphous region) exhibited improved fatigue performance, suggesting that cracks preferentially travel through the amorphous region of PFA 6. Transmission IR spectra of PFA wear debris revealed the presence of free carboxylic acid endgroups that were not present in the bulk PFA surface. The presence of free carboxylic acids is due to the breaking of C-C bonds in the PFA backbone reacting with environment constituents. The formation of free-carboxylic acids endgroups is a critical intermediate step of the tribochemical reaction necessary to form robust transfer films and running films proposed for PTFE-alumina composites 7.
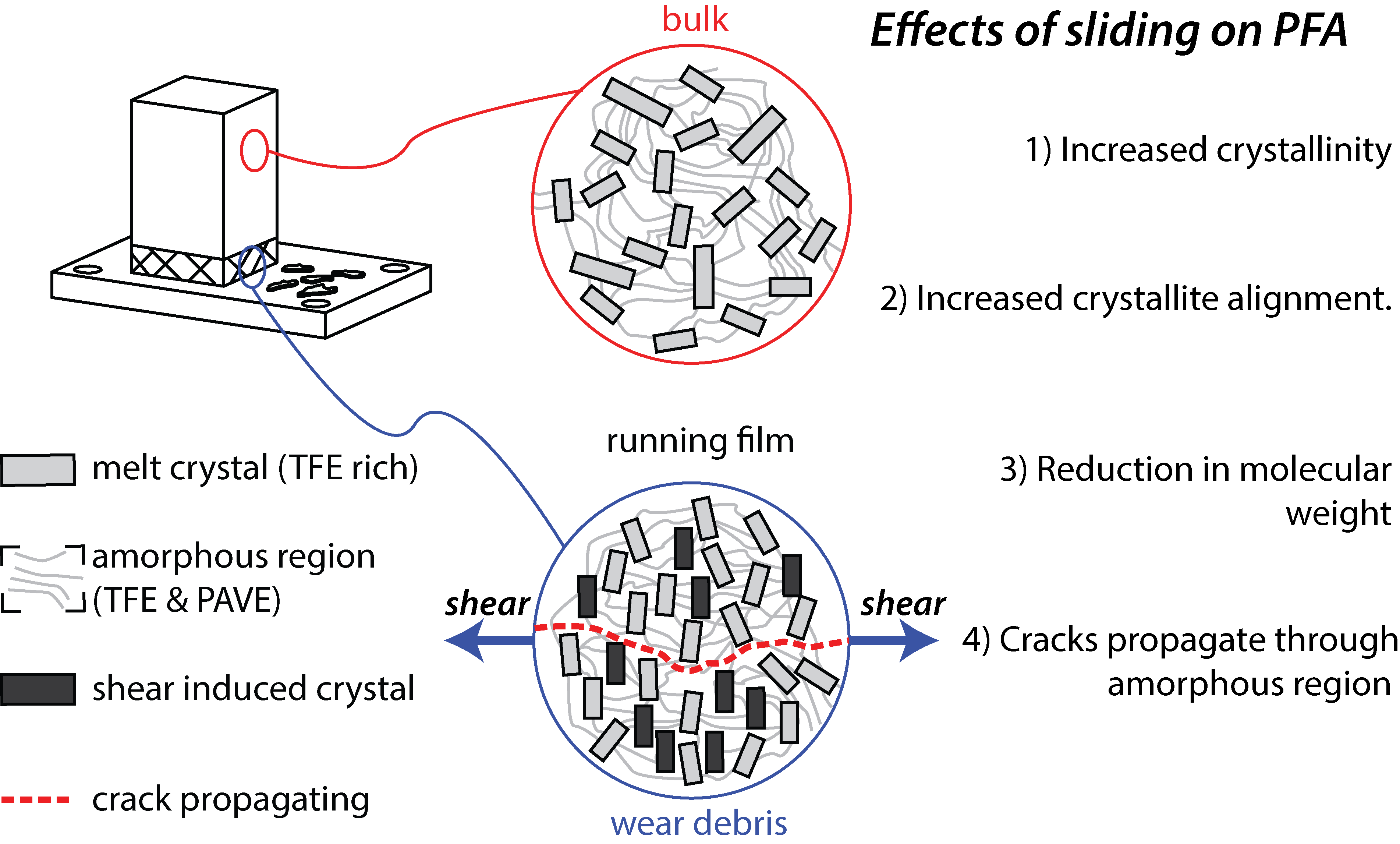
Figure 1 – Effects of sliding on unfilled PFA against a stainless steel substrate
REFERENCES:
1. Bowers, R. C. & Zisman, W. A. Frictional Properties of Tetrafluoroethylene-Perfluoro(propy1 vinyl ether) Copolymers. 13, 115–118 (1974).
2. Crosby, J. M., Theberge, J. E. & Talley, K. L. Melt Processible Fluropolymer Composites. J. Elastomers Plast. 13, 149–155 (1981).
3. Sidebottom, M. A. et al. Ultralow wear Perfluoroalkoxy (PFA) and alumina composites. Wear 362–363, 179–185 (2016).
4. Khedkar, J., Negulescu, I. & Meletis, E. I. Sliding wear behavior of PTFE composites. Wear 252, 361–369 (2002).
5. Fujimori, A. & Hayasaka, Y. Changes in arrangement of lamella and fine crystallite in fluorinated ‘crystalline’ transparent fibers with drawing. Macromolecules 41, 7607–7615 (2008).
6. Lee, J. C., Namura, S., Kondo, S. & Abe, A. Miscibility and cocrystallization behavior of two melt-processable random copolymers of tetrafluoroethylene and perfluoroalkylvinylether. Polymer (Guildf). 42, 5453–5461 (2001).
7. Harris, K. L. et al. PTFE Tribology and the Role of Mechanochemistry in the Development of Protective Surface Films. Macromolecules 150526153713007 (2015). doi:10.1021/acs.macromol.5b00452