of the tangential force experienced by the surface of the deformed body (not shown).
Figure 4 shows the evolution of the tangential force. It is typically the fretting loop for the initial cycles as indicated by Courtney-Pratt and Eisner5.
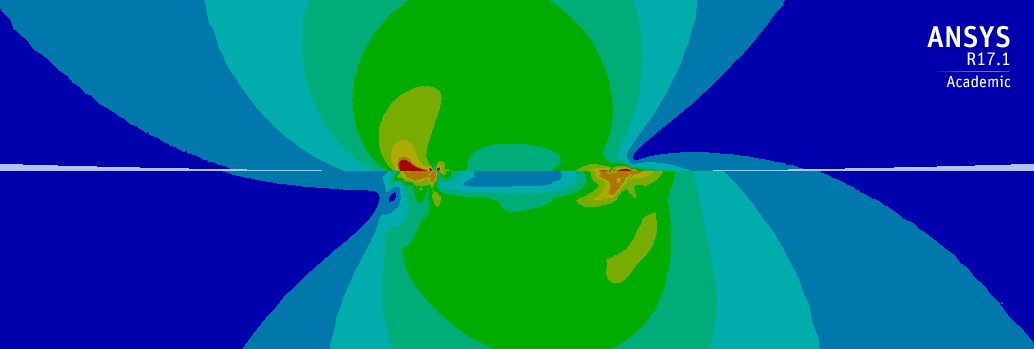
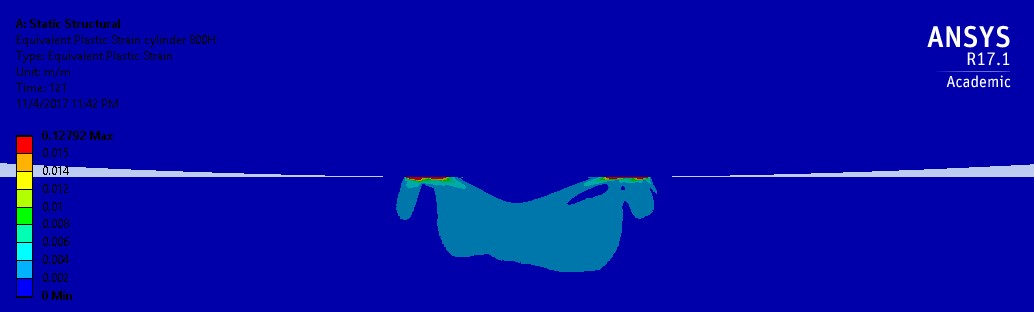
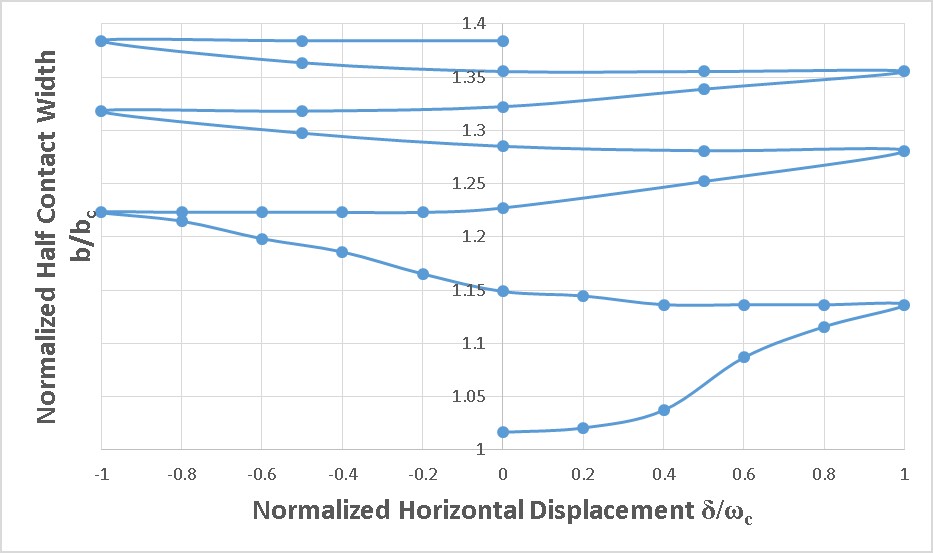
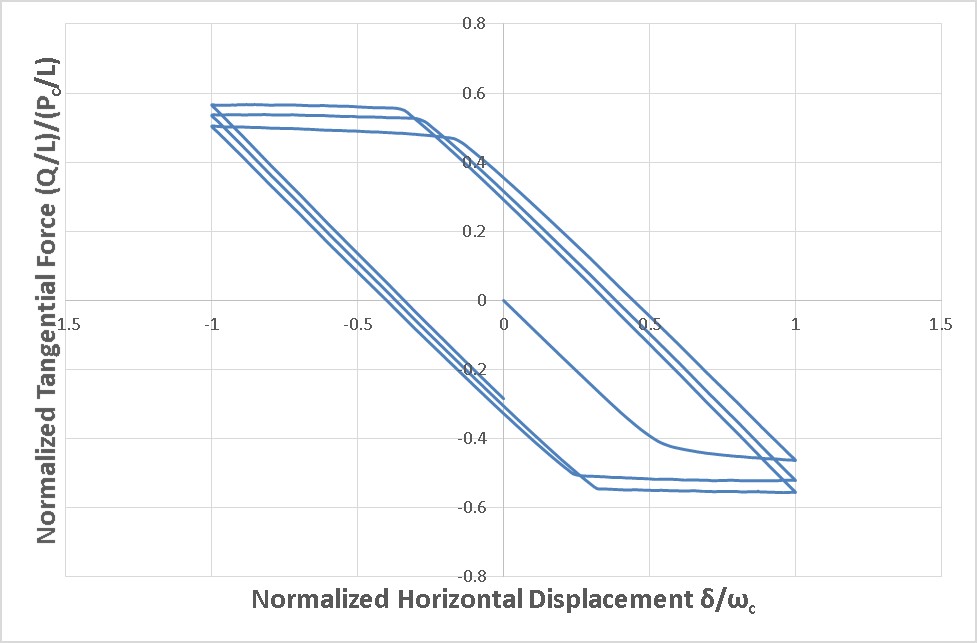
Figure 2 - A) The distribution of von-Mises stress after three cycles of fretting motion B) The distribution of plastic strain after three cycles of fretting motion C)The junction growth during three cycles of fretting motion D)The evolution of tangential load
DISCUSSION: During the oscillatory tangential loading, the two contact edges tend to experience the largest von-Mises stress. It is, therefore, postulated that cracks and fatigue are most likely to initiate and propagate at the contact edges. During the fretting between INCOLOY 800H and INCONEL 617, INCONEL 617 is hard to yield. The explanation could be that as the INCOLOY starts to yield, its resistance to the increasing load does not change much, which leads to the elastic behavior of INCONEL.
The junction growth is found during the fretting motion. The more pronounced growth on the two edges is in the same direction of the tangential force experienced by the surface of the deformed body. The conclusion agrees with the results of Brizmer6 whose model is the contact between a deformable sphere and a rigid flat under full stick condition. It is indicated that the junction growth is caused by the plastic deformation on the contacting surfaces.
There are abrupt changes of the curvature at the edges of the indentation on the surface after the fretting motion (not shown). When the COF is large enough to reach the fully stick condition, pileup will appear at the position of the abrupt change. In the case with the appearance of pileup, the plastic strain at the edges of the contact is correspondingly larger.
The temperature elevation (from 20C to 800C) causes the increase of the plastic strain and the decrease of the tangential force, normal force, and the maximum von-Mises in INCONEL 800H. Therefore, the fretting between the alloys will bear more damages in the elevated temperature under the same load input.
REFERENCES: 1.Slack, Tribology Transaction (2013), 2.Mei, Proc. Advanced Materials Research (2013), 3.Johnson, Contact Mechanics (1987), 4.Green, Applied Mechanics and Engineering (2005), 5. Courtney-Pratt and Eisner, Proceedings of the royal society of London A: Mathematical, Physical and engineering Sciences (1959), 6.Brizmer, Journal of Tribology (2007).