RESULTS: The calculation and measurement results are presented in the diagram below (Fig. 3). One may notice that after this very simple experiment – filling bush with boiling water – the difference in water temperature inside as a function of time is significant.
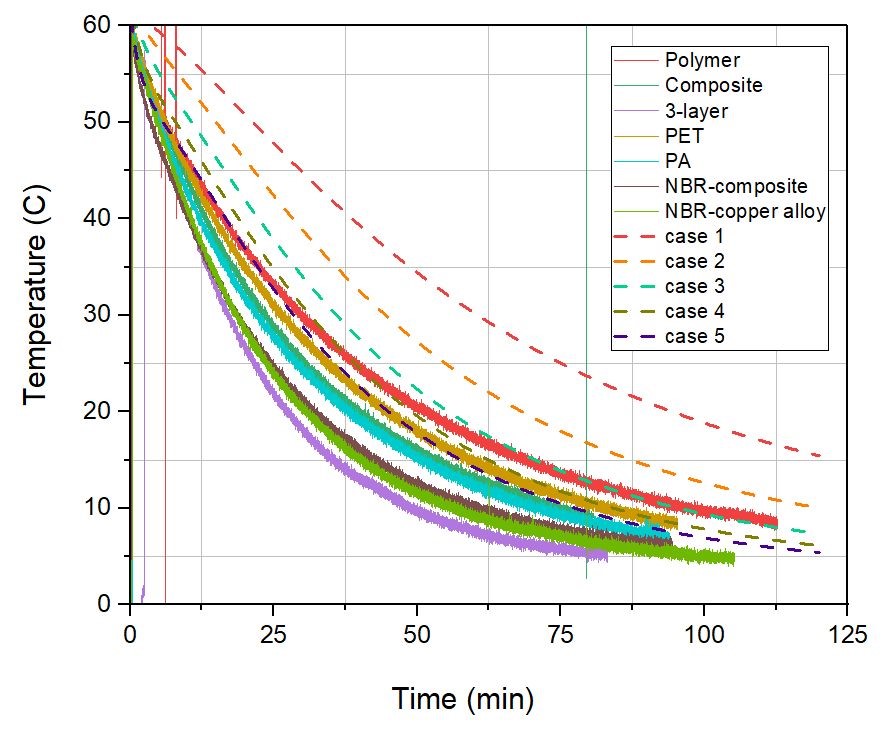
Figure 3 – Calculations and measurement results for selected bearing bushes
CONCLUSIONS: Bush thermal conductivity plays a significant role for bearing operation under critical conditions of lubricant flow absence. The conducted FEM calculation help to understand the impact of bush geometry on the problem of bearing overheating.
ACKNOWLEDGEMENTS:
This work was a part of a research grant no. 2016/23/B/ST8/03104 entitled “Research on water lubricated sliding couples in conditions of improper lubrication conditions” financed by the Polish National Science Centre.
REFERENCES:
1. Litwin, W. & Dymarski, C. Experimental research on water-lubricated marine stern tube bearings in conditions of improper lubrication and cooling causing rapid bush wear. Tribol. Int. (2016). doi:10.1016/j.triboint.2015.12.005
2. Litwin, W. Influence of bush wear in water lubricated marine stern tube bearings with shaft misalignment. in 5th World Tribology Congress, WTC 2013 4, (2013).
3. Barszczewska, A., Sadowski, J. & Litwin, W. Research on water lubricated main shaft bearings in conditions of improper lubrication and cooling conducted on high torque real-life scale bush test rig. in World Tribology Congress , Beijing, China, September 17 – 22, 2017 (2017).