Effect of temperature on tribology of PBI/PEEK blend
Annelise Jean-Fulcrand1, Marc Masen1, and J. S. S. Wong1*
*j.wong@imperial.ac.uk
1Department of Mechanical Engineering, Imperial College London, London SW7 2AZ, UK.
INTRODUCTION: High performance polymers (HPPs) are polymers that have properties that allow them to be used in conditions that tradition polymers are deemed unsuitable. These properties, such as very good chemical resistance, good mechanical properties even at relatively high temperature, and good tribological properties, make them attractive alternatives to components that are commonly made of metal. When HPPs are used as tribological components, they often rub against metal counterparts. Thus it is important to understand how HPPs interact with metal in tribological contacts to guide our material selection decision. This is especially important in situations when lubricants cannot be used.
Polyetheretherketone (PEEK) is one of the most studied HPPs. While it has attractive attributes, its major weakness is its relatively low glass transition temperature (Tg) of about 150°C. This limits the operating temperature PEEK can be used. One way to overcome this limitation is by blending PEEK with another polymer that has higher Tg. Polybenzimidazole (PBI) is a good candidate to add into PEEK. PBI has a very high Tg of about 340°C. It also possess excellent mechanical properties. Thus intuitively adding PBI into PEEK would result in a blend with better mechanical properties and higher operation temperature (see Table 2). There are two questions that require clarifications:
- Does the addition of PBI alter tribological performance of PEEK. especially at high temperature?
- How does the addition of PBI change the interaction between PEEK and metal counterface during rubbing?
To address question (1), we conducted tribological testing with PEEK, PBI/PEEK (TU60), and PBI at various temperatures. For question (2), chemical and topographical characterizations were carried out on both the polymer and metal rubbed surfaces.
METHODS: Tribological tests were carried out with High Temperature Tribometer (Anton- Paar) [1]. A ball-on-flat geometry was adopted with a stationary steel ball, made of AISI52100 steel, pressed and rubbed against a rotating polymer disc. Three types of polymer discs were used, PEEK, PBI/PEEK blend (called TU 60 with PBI:PEEK = 50:50 by weight) and PBI. Materials properties of polymer discs and steel samples are in Table 2. The test conditions are in Table 1. All tests were conducted in ambient air and in non-lubricated condition, i.e. no lubricant was used.
Table 1 – Test Conditions.
Test temperature (°C)
|
100, 200, 280
|
Applied Normal Load (N)
|
10
|
Sliding speed (m/s)
|
0.1 – 2
|
Rubbing distance (m)
|
3600
|
Table 2 – Material properties of test samples. Note properties of polymers provided by materials suppliers.
|
Tg (°C)
|
Tm (°C)
|
Heat Deflection
Temp (°C)
|
Hard-ness (Shore D)
|
Young’s modulus (GPa)
|
Compressive
yield strength (MPa)
|
PEEK
|
143
|
343
|
152
|
85
|
3.5
|
125
|
PEEK/PBI
|
143
|
343
|
262
|
90
|
4.9
|
207
|
PBI
|
427
|
N/A
|
435
|
95
|
5.9
|
400
|
Steel
|
N/A
|
1424
|
N/A
|
700HV
|
200
|
2500
|
Surface topography of steel balls and polymer discs was observed with white light interferometry. Surface chemistry of worn surfaces was examined with energy dispersive X-ray analysis (EDX) with scanning electron microscopy (SEM), X-ray Photoelectron Spectroscopy (XPS) and Fourier transform infrared Spectroscopy (FTIR).
RESULTS AND DISCUSSION: The effects of test temperature and sliding speed on friction coefficients obtained between our polymer discs and steel balls are shown in Figure 1.
Figure 1 – How friction coefficients (COF) between polymer discs against steel balls are affected by test temperatures and sliding speed.
At 100 and 200°C, PBI/PEEK blend and PEEK discs have very similar friction coefficients at all speeds while PBI has lower friction. This suggests that friction property of PBI/PEEK blend is controlled by PEEK. This is likely to be a temperature-controlled phenomenon. As PEEK has a lower Tg, the rubbing interface of PBI/PEEK-steel contact is likely be controlled by PEEK if a critical temperature is reached.
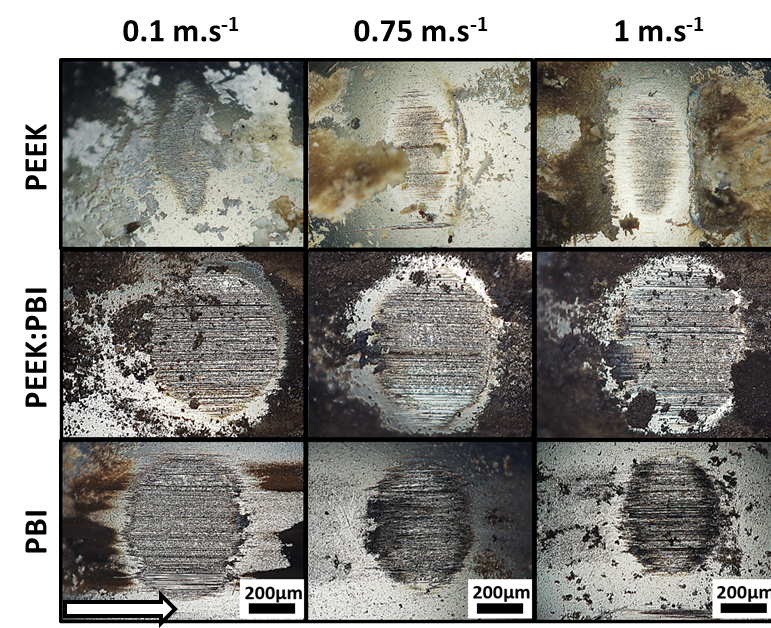
Figure 2 – wear scars on steel balls. Test temperature is 100°C
While rubbing PEEK and PBI/PEEK against steel give similar coefficient frictions, the amount of wear on steel ball is very different with the blend results in much higher wear. Surface chemical analysis are being carried out and will be discussed.
REFERENCES: 1. Jean-Fulcrand, Polymer. (2017).
ACKNOWLEDGEMENT: AJF is funded by EPSRC and Hoerbiger Corporation of America, Inc., Houston