Lubrication behavior and mechanism of mica–organic hybrid solid lubricants synthesized via intercalation reaction
Kenichiro Oshita1,2, Shinobu Komiyama1, Shinya Sasaki2
1Nihon Parkerizing Co., Ltd., 2Mechanical Engineering, Tokyo University of Science, Tokyo, Japan
INTRODUCTION: Solid lubricants have been widely used to improve lubricity, to prevent seizure and to reduce wear loss in applications such as lubrication coatings for cold forming products and oil additives for sliding parts. Under these friction environments, the solid lubricant materials are required to cleave and extend on a metal substrate to prevent direct contact between the substrate and its opponent material. Among various kinds of solid lubricants, MoS2 is generally much more suitable due to its low friction coefficient facilitated by its easy cleavage. The problem with using MoS2, however, is that its black appearance can severely contaminate the working environment. For this reason, researchers have been eagerly seeking a non-black solid lubricant with properties similar to MoS2.
We have focused on an intercalation technique, in which an alkyl ammonium cation is inserted into mica’s interlayer region by an ion-exchange reaction, and revealed that it drastically promoted the cleavage ability under cold forming condition.1
In this study, we investigated the basic tribological properties of mica–organic cation hybrid solid lubricants under reciprocating sliding condition, and discussed the lubrication mechanisms in terms of electrostatic interaction between the mica’s silicate layer and the intercalated organic cation using FTIR spectroscopy.
METHODS: We used a mica (Cation exchange capacity; 1.2 mol/kg, particle size; 6.4 µm, exchangeable cation; Na+) as a host material. Three alkyl ammonium cations are prepared as an intercalating agent: DTA (C12H15N(CH3)3-), OTA (C18H37N(CH3)3-) and DODA (C18H37)2N(CH3)2-). The mica and the organic cation were reacted in deionized water at 70 °C for 1 h. After the reaction, the treated mica was separated by filtration, washed with deionized water, and then dried at 110 °C. Figure 1 shows the formations of cations in mica’s interlayer region estimated from d-spacings analyzed by XRD. The mica is formed on a cold rolled steel sheet with cellulose binder by a bar coating with a thickness of 5–7 μm. Lubrication performance was evaluated using a reciprocation-type cylinder on disk tribotester (SUJ2 cylinder; φ5.0 mm×10 mm, vertical load; 50 N, RT).
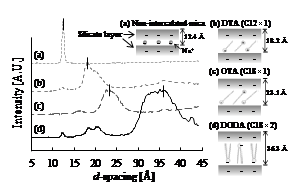
Figure 1 – Formations of cations in mica’s interlayer region estimated from d-spacings analyzed by XRD.
RESULTS: Figure 2 shows the changes in the dynamic friction coefficient of non-intercalated and intercalated micas in comparison with MoS2. Non-intercalated mica exhibited a friction coefficient of around 0.5, while intercalated micas showed a lower dynamic friction coefficient of below 0.3.
The effect of intercalation on decreasing friction coefficient varied with the chemical structure of organic cation, ie the length and number of alkyl chains. DODA having two C18 alkyl chains showed the lowest friction coefficient of around 0.12, approaching a level close to MoS2.
Figure 2. Friction behavior of non-intercalated and intercalated micas in comparison with MoS2 measured by cylinder-on-disk tribotester.
DISCUSSION: It is well known in clay science that the interlayer cations (Na, K, Mg etc.) have an electrostatic interaction with positively charged silicate layers and affect the cleavage properties.2 That is, when the positive charge density in the interlayer region becomes lower, the adhesion strength with the silicate layers becomes weaker, which contributes to easy cleavage.
Considering from the viewpoint of the electrostatic interaction, replacing Na+ with organic cation by intercalation technique should reduce the electrostatic interaction between the cation and silicate layers, resulting in the change in ionic bonding of Si–O of the silicate layer. Figure 3 shows the Si–O stretching absorption wavenumber using FTIR spectroscopy. It was found that the wavenumber shifted to higher with the length and number of alkyl chains (Na+ < DTA < OTA < DODA). This order of IR shift is considered to be caused by the degree of weakness of interaction between silicate layer and alkyl chain. This result correlated well with the friction behavior shown in Figure 2.
The weakened interaction by organic cation causes the increases in negative charge density on oxygen of Si–O in silicate layer. So that the ionic bond strength of Si–O becomes greater, resulting in the IR shift to higher wavenumber. Thus, the degree of IR shift is a reliable indicator for evaluating mica’s cleavage ability.
Figure 3 – IR spectra and cleavage ability of a non-intercalated and an intercalated micas considered from the viewpoint of the interlayer adhesion strength: (a) Non-intercalated mica, (b) DTA, (c) OTA, (d) DODA.
REFERENCES: 1. Oshita, K. Surf. Coatings Technol. 325, 738–745 (2017), 2. Zhang, J. Appl. Clay Sci. 80, 267–280 (2013)
Figure 1 - A) Typical cartilage deformations during highlighted portions of the experiment. B) Deformation in a representative sample during 3 different activity cycles.