Organic Liquid Generated from DLC during Laser Heating
Hiroshi Tani1, Yuta Shibahara 2, Yuki Uesaraie2, Renguo Lu1, Shinji Koganezawa1, Norio Tagawa1
1Mechanical Engineering, 2Graduate School, Kansai University, Osaka, JAPAN
INTRODUCTION: Diamondlike carbon (DLC) films have attracted interest over the years as scientifically intriguing and practically effective tribological materials for various industrial applications. Erdemir suggested that DLC films may contain large amounts of hydrogen in their structures and offer superlubricity under dry and inert tribological conditions when they are synthesized in hydrogen-containing environments1. Depending on the nature and extent of bulk, surface, and tribochemistry, they can provide superlow friction coefficients, down to a level of 0.001. High hydrogen concentration within their bulk, on their surfaces, or at their sliding contact interfaces can lead to superlubricity. Zeng reported high-temperature superlubricity achieved from a DLC film friction system2. Their superlubricity was approximately 0.008 for more than 100,000 s at steady state at a temperature of 600°C due to the formation of self-generated lubricious composite oxides of g-Fe2O3 and SiO2 at the contact surfaces through a tribochemistry reaction during the running-in process. Tokoroyama found that the nitrogen atoms desorbed from the top layers of the coating, and that the layers changed to a graphitelike structure without nitrogen during a friction coefficient decrease to lower than 0.01. The graphitization of the topmost layers was attributed to the low friction coefficient in N2 gas3. Nosaka reported that spherical ZrO2 pins sliding on DLC films under an H2 gas environment showed an exceptionally low friction coefficient4. They termed that behavior “friction fade-out” (FFO), and the friction coefficient was estimated to be approximately 0.0001. They suggested the possibility of an elastohydrostatic gas bearing as the mechanism of the superlow friction coefficient, where gas is not supplied from outside of the contact area but evolved from the contact surface5.
In this study, we report that the organic liquid was generated from DLC film by the heating of laser irradiation and that organic liquid greatly reduced the friction coefficient.
EXPERIMENT: The experimental setup of the noncontact pin-on-disk test developed in our previous study6 is illustrated in Figure 1(A). As seen, a magnetic disk without lubricant film was placed on a spindle motor rotating at 6 rpm (relative velocity of 14.8 mm/s). A semispherical glass lens was used with a curvature radius of 1.82 mm. The distance between the pin and disk surfaces was controlled to 5 μm by moving the piezo control stage from the contact height of the pin and the upper position of the disk run-out. The laser beam was irradiated through the glass pin to the disk surface, and the heating temperature was changed from 300°C to 700°C by adjusting the laser power. The laser spot diameter was approximately 100 mm. After laser heating for 5 min, we observed that the liquid adhered on the glass pin surface, and the adhered liquid was transferred onto a silicon wafer surface by the pin–disk contact to analyze its chemical structure using time-of-flight secondary ion mass spectroscopy (TOF-SIMS), as illustrated in Figure 2(B). However, we compared the friction coefficients for the cases of the contact pin-on-disk friction tests with and without laser heating. The magnetic disks used in this study had DLC film with approximately 3-nm thickness. The DLC film was deposited by chemical vapor deposition (CVD) and had an amorphous carbon structure with nitrogen and hydrogen atoms.
RESULTS: The observed liquid meniscus formation between the glass pin and silicon surfaces and the positive ion mass spectrum of transferred liquid onto silicon wafer surface measured using TOF-SIMS are shown in Figure 2. The liquid meniscus was observed in the case of a noncontact pin-on-disk test performed in a helium gas

A. Organic liquid condensed on glass pin surface by laser heating
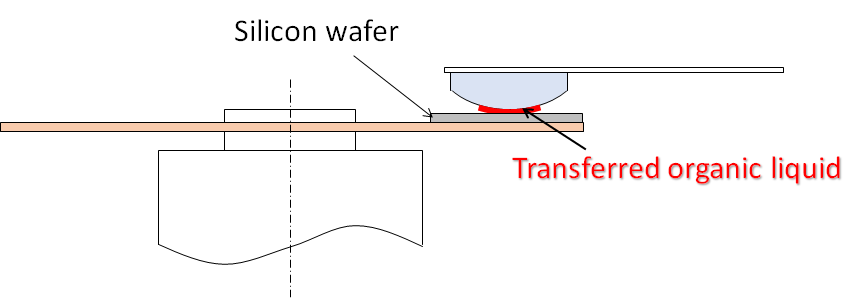
B.Transferring the organic liquid onto a nsilicon wafer
Figure 1. Previously developed noncontact pin-on-disk tester to correct organic liquid condensed on the glass pin surface from the DLC surface following laser heating
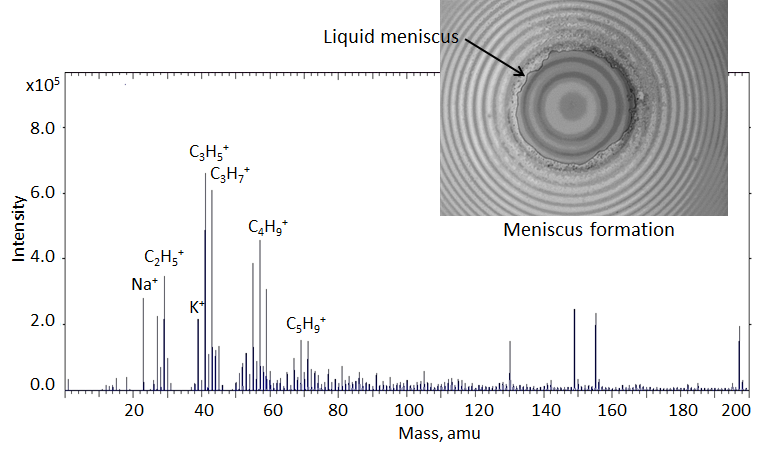
Figure 2. Liquid meniscus formation between a glass pin and silicon surfaces and positive ion mass spectrum of organic liquid transferred onto silicon surface obtained from TOF-SIMS measurement
environment with laser heating of 300–500°C. However, that could not be observed on the case of an air environment. The measured TOF-SIMS spectrum indicated that the liquid material condensed on the glass pin surface might be organic hydrocarbon.
DISCUSSION: Because the liquid meniscus could not be observed on the noncontact pin-on-disk test in an atmospheric environment and could be observed in a helium gas environment at laser heating of more than 300°C, it is estimated that the DLC film decomposes to hydrocarbon and condenses as organic hydrocarbon liquid on the pin surface, when it is heated in an inert gas environment at a high temperature of over 300°C. Organic hydrocarbon liquid generated from the DLC film by laser heating should reduce the friction coefficient in the role of lubricant oil.
REFERENCES: 1. Erdemir, Friction (2014), 2. Zeng, RSC Adv., (2015), 3. Tokoroyama, Tribol. Lett. (2006), 4. Nosaka. Proc MechE, Part J: J Engineering Tribology (2015), 5. Kato, Proc IMechE Part J: J Engineering Tribology (2017), 6. Tani, Proc. ISPS2017 (2017)