Figure 1 – Abaqus/Explicit model with the ball on flat configuration.
Quadratic elements were used for the flat and tetrahedral elements were used for the ball. The mesh is refined at the contact.
When the ball impacts the sample, it can bounce back or bend the foils that connect the ball holder to the electromagnetic shaker. This should be avoided because it could disrupt the vertical ball displacement.
The ball is modeled with a dynamic high velocity law, known as the Hallomon’s law7. The tungsten carbide samples are defined with an elastic perfectly brittle behavior.
RESULTS and DISCUSSION: The observation of the wear scars on the ball and the tungsten carbide sample shows that the main wear phenomenon is abrasion. Adhesion also occurs very rapidly and tends to dampen the wear process. Scars are covered with oxides from the ball material. On top of that, some particular wear features are clearly seen at high impact energy8. For the tungsten carbide sample with the lowest fracture toughness, cracks can be observed on the outer part of the contact area.
By comparing the results obtained in numerical modeling and in experimental tests, it was possible to get more knowledge in the sliding distance (about 100 µm for impact energy of 4 mJ), contact area and rebounds, and stresses and strains, which helped us to better understand the tribological behavior of the different couples of materials and analyze the effect of mechanical properties of materials and friction coefficient, in impact-sliding conditions.
The simulation shows that the stress distribution at the contact is linked with fracture occurring on the tungsten carbide with the lowest toughness. Besides, the plastic deformation of the ball plays a role in the contact surface between the two antagonist materials. This influences the size of wear scars on the flat as well as on the ball. Fatigue features observed on the tungsten carbide could be correlated with specific strain localizations (Figure 2).
Concerning quantitative analysis of wear, the model shows that only 10% of the impact energy is converted into friction dissipation. Moreover, wear rate is correlated with the sum of energy dissipated by friction and by plastic deformation, but not with frictional energy.
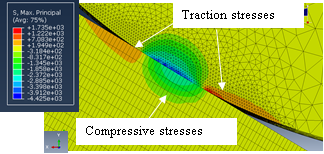
Figure 2 - Abaqus/Explicit stresses (ball on flat configuration).
CONCLUSIONS: This study emphasizes on the damage mechanisms involved in the ball on flat contact during impact-sliding conditions. Stresses and strains involved in the contact during the “impact-sliding” are in great correlation with wear features observed on wear scars. The numerical simulation could help us in explaining the experimental wear features and wear mechanisms.
REFERENCES: 1. Zhang, Mater. Sci. Eng. A (2011), 2. Beste, Int. J. Refract. Met. Hard Mater. (2006), 3. Antonov, Wear (2015), 4. Bailey, Wear (1974), 5. Marou Alzouma, Wear (2016), 6. Messaadi, Wear (2013), 7. Messaadi, Wear (2015), 8. Fall, Wear (2017)