Table I. Experimental conditions
|
|
Disk
|
Pin
|
Ambient
|
Temp (oC)
|
Normal Force (N)
|
Sliding vel. (m/s)
|
Inc 617
|
Inc 617
|
Air, He
|
25, 500, 950
|
5, 10, 20
|
0.04, 0.1, 0.15
|
800HT
|
800HT
|
25, 500, 750
|
Results and DISCUSSION: Fig. 2a represents the in-situ COF of Inconel 617 at room and high temperatures in air as well as in helium environments. At high temperature in air, the COF of both alloys drops significantly (about 60% reduction) after few cycles and it is stabilized at lower values. However, the COF at room temperature in air and high temperature in helium shows high and stable values for both samples. The COF at higher temperature in air remains constant with sliding time after the initial run-in period of about 200s for Inconel 617 and 400s for alloy 800HT at low loads.
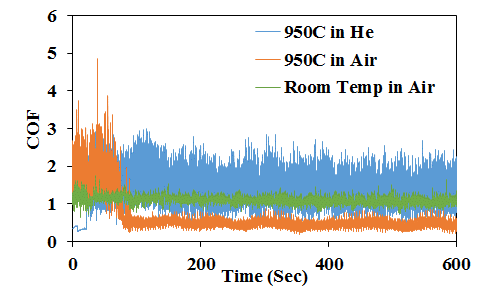
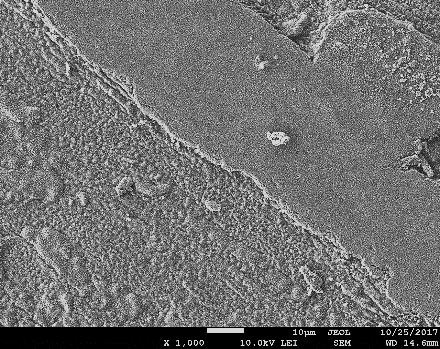
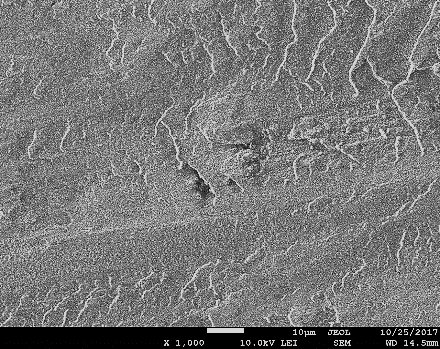
Fig. 2. (a) In situ COF experiments: Inconel 617 pin on Inconel 617 disk. SEM images of 20N Inconel 617 (b) 950oC in air, (c) 950oC in He.
Further observation by SEM in Fig. 2b reveal the formation of the glazed surface of the oxides at HT air which is not present on the samples at HT in helium environment, as shown in Fig. 2c. The observed lower COF at HT in air is attributed to the compact glazed oxide layers separating the two metallic surfaces.3,4 Fig. 3 shows the average COF and wear rate for different loads. As seen in Fig. 3a, for Inconel 617, in He environment, the COF is minimum at an intermediate temperature and highest at 950oC for all loads. Alloy 800HT behaves similarly in He environment, showing very high friction at 750oC for all loads and lowest COF at the intermediate temperature.
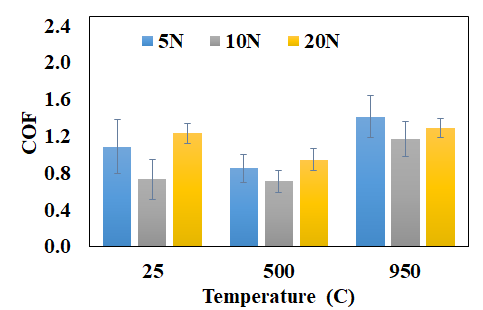
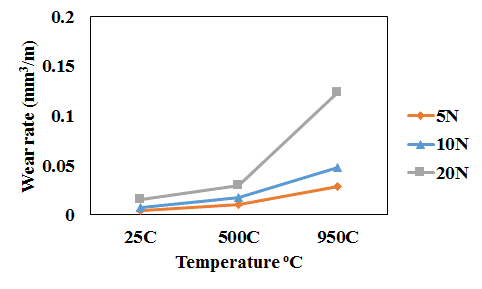
Fig. 3. The influence of temperature and load on Inconel 617 (a) COF and (b) Wear rate.
Cross section SEM and EDS analysis of the alloys show that the surface oxide is mostly Cr-rich. Microhardness test reveals that although both alloys have fairly same hardness value outside of the wear track, the hardness of Inconel 617 is more than that of alloy 800HT after sliding showing more hardening effect on Inconel 617 leading to better wear resistant property.
REFERENCES: 1. Cabet C, Mater Corros (2006), 2. Wright RN., INL/EXT-06-11494 (2006), 3. Birol Y, Wear (2010), 4. D. Y. Li, Wear (2005).