in the bottom of the lower bound is the particle-to-surface two-body contact.
Fig. 2(B) shows variation of contact load ratio with speed parameter at various particle density. As shown in the Fig. 2(B), the percentage of solid load decreases with increasing velocity parameters, and increases with increasing particle density at the same velocity parameter. When the particle density is between 7 10-11 and 10-12, when the velocity parameter is less than 1 x 10-11, the solid load percentage is greater than 90 %, the contact condition has entered the boundary lubrication. It indicates that under this condition wear and friction force will increase rapidly.
In the past studies have shown that the greater the sliding speed, the smaller the film thickness between the contact interfaces in two-body contact condition. However, the lubrication film thickness under three-body contact condition are shown in Fig. 3, When the particle size is smaller, the predictive value have same trend with the film thickness theoretical of Masjedi and Khonsari , the dimensionless film thickness increases as the speed parameter and particle diameter increases; however at the speed parameter smaller, such as U = 10-11, the dimensionless film thickness Hc = 4.2 x 10-5 (hc = 0.85 μm) when the particle diameter is as large as 700 nm, and that is about 2.1 times when xa = 0 nm, and about 1.8 times when xa =500 nm. It indicates that the wear debris have a considerable deviation on the film thickness at the interface.
Table 1. Material properties of S45C
Property
|
Value
|
Hardness, H (GPa)
|
2.0, 5.0
|
Young's modulus, E (GPa)
|
205, 409
|
Poisson ratio, u
|
0.29
|
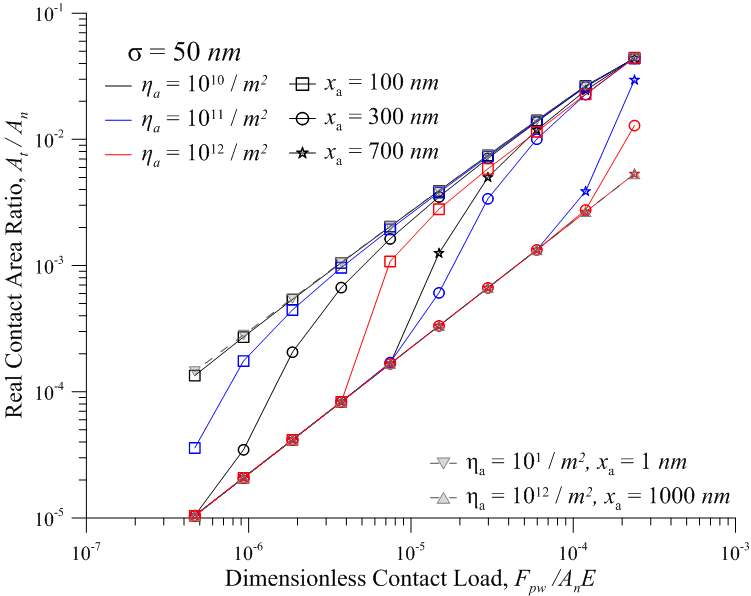
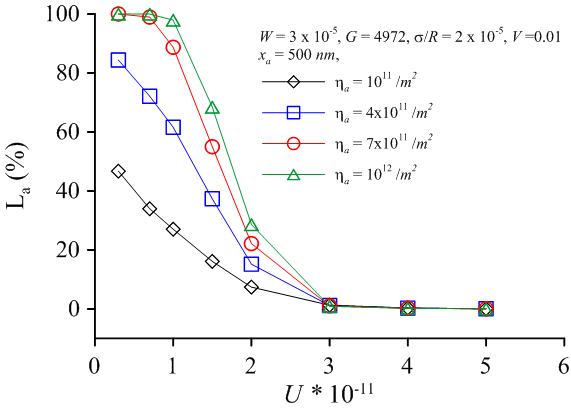
Figure 2 - A) Total real contact area ratio vs. dimensionless contact load at various particles diameters and particles densities. B) Variation of contact load ratio with speed parameter at various particle densities.
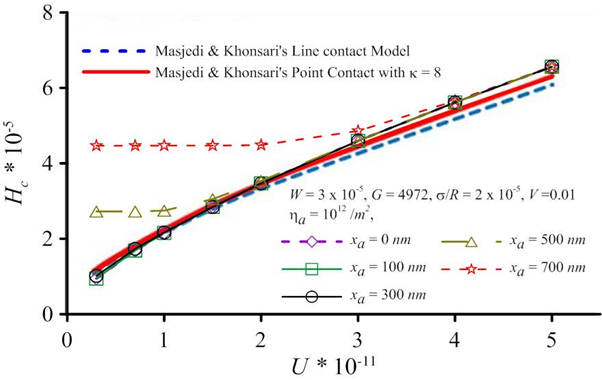
Figure 3 - Variation of dimensionless film thickness with speed parameter at various particle diameter.
REFERENCES: 1. Horng-Wen, Wear. (2015), 2. Horng-Wen, Micromachines (2017), 3. Jeng-Haur, Ind. Lubr. Tribol. (2017), 4. Masjedi, Tribol. Int. (2015)