with little change to 16 m/s. With decreasing sliding speed, the COF remains steady from 16 m/s, then increases smoothly below 9 m/s. In Fig. 1B, reciprocal motion shows a significant change in the appearance and size of the Si3N4 ball wear scar from 22 to 1000 °C with COF of 0.82, 0.73 and 0.44 from B1 to B3. A comparison between the films on the Si3N4 balls after high speed sliding (Fig. 1C) and high temperature (Fig. 1D) reveal cracking patterns in the surface films remaining on the Si3N4 balls.
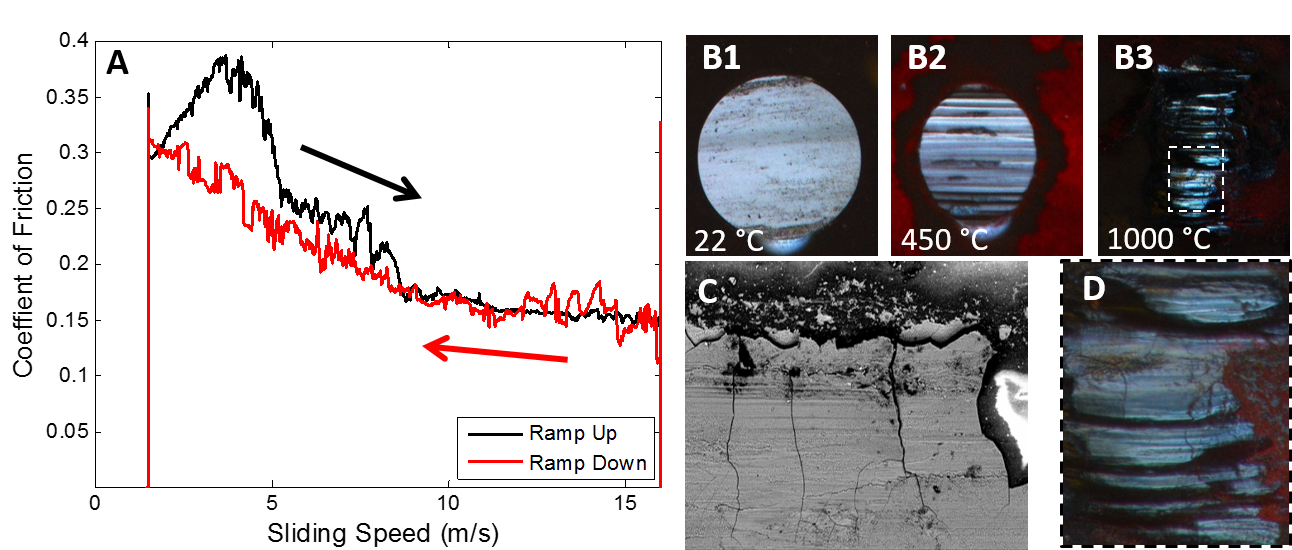
Figure 1 – A) COF of sliding-rolling contact vs. sliding speed over 210 s. Average ball and disk speed maintained at 16 m/s. B) Optical images (1 mm wide) of Si3N4 ball wear scars of low speed at three temperatures. C) SEM image (150 µm wide) of Si3N4 ball after high sliding speed. D) Close-up of B3 (280 µm wide).
DISCUSSION: For high speed contacts, the transition in friction and tribochemical wear mode depends on immediate contact history, both during smooth variation of sliding speed (Fig 1A) and when changing between static sliding speeds (based on additional experiments). At static sliding speeds, the COF remains steady when coming from a higher speed/lower COF, but is less stable from a lower speed/higher COF. Such behavior indicates that the highly lubricious tribofilm can be maintained once formed to varying extent, but takes time to form in the first place from a higher friction state.
High speed specimen characterization reveals that the film on the steel surface is more homogenous and contains areas of Si/Fe/O, while the film on the Si3N4 surface has intermixed areas of Fe/O and Si/N. However, both steel and Si3N4 surfaces display significant plastic deformation in the surface film and fracture indicative of thermal stress upon cooling, both also visible on the high temperature specimens. Diffusion of Si into Fe oxide starts around 500 to 700 °C with the release of N2 and formation of SiO2 and Fe2SiO4 at 1000 °C.15 These temperatures can easily be met through flash heating at high sliding and explain the presence of Si, but not N on the steel surface film. The melting point of Fe2SiO4 is 1200 °C, several hundred °C below that of steel or other Fe oxides, which may provide a lower friction layer for sliding, however, no clear evidence of a particular ferrosilicate has yet been found.
REFERENCES: 1. Ashby, Materials selection in mechanical design (2005). 2. Wang, Wear (2000). 3. Silva, Wear (1991). 4. Gautier, Wear (1993). 5. Childs, Wear (1993). 6. Ravikiran, J. Amer. Cer. Soc. (1995). 7. Kalin, Mat. Sci. and Eng.: A (1996). 8. Kalin, Wear (1997). 9. Novak, Wear (1999). 10. Gomes, J. Amer. Cer. Soc. (1999). 11. Gomes, Wear (2001). 12. Carrasquero, Int. J. of Refr. Met. and Hard Mat. (2005). 13. Sutor, 8th Ann. Conf. on Comp. and Adv. Cer. Mat. (2008) 14. Berkebile, Trib. Front. (2015). 15. Kalin, Mat. Sci. and Eng.: A (2000).
Research was sponsored by the Army Research Laboratory and was accomplished under Cooperative Agreement Number W911NF-16-2-0214. The views and conclusions contained in this document are those of the authors and should not be interpreted as representing the official policies, either expressed or implied, of the Army Research Laboratory or the U.S. Government. The U.S. Government is authorized to reproduce and distribute reprints for Government purposes notwithstanding any copyright notation herein.