RESULTS: As given in Figure 1, wear rates of all materials investigated increase with rising temperatures. Starting with diverging wear rates at 20 °C, at 500 °C results are most divergent and finally reaching almost identical values at 700 °C for the cast materials investigated.
Figure 2 shows surface and cross-sectional analyses at 20 ° and 700 °C for Material 1 and 4, indicating, that ferritic cast irons tend to form mechanically mixed layers more easily than austenites. Statistically, the surface of the ferrites is covered with more particles, which can act as wear protection.
The wear rates are strongly dependent on hot hardness, elasto-plastic material’s behaviour and the in-situ formation of mechanically mixed layers 4-9, as explained in the discussion and in the full paper of this study.
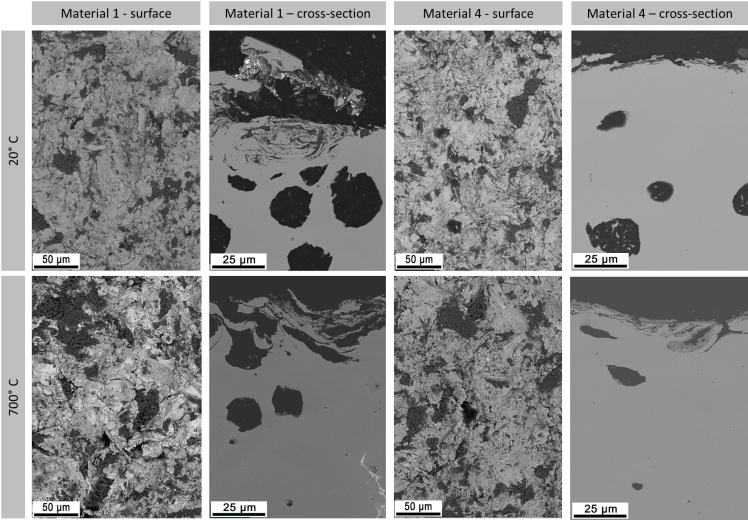
Figure 2 – Surface and cross-sectional analyses via SEM.
DISCUSSION: As given in the results, wear rates increase with temperature due to the increased plasticity and loss of hardness at elevated temperatures. This also promotes the formation of mechanically mixed layers and particle sticking to the surface.
A statistical analysis on the influence of hardness, toughness (apparent Young’s modulus) and temperature on wear behaviour and mechanically mixed layer formation was undertaken. It indicates that ferritic nodular cast irons form these protective mechanically mixed layers easier, while austenites tend to be abraded at a higher level due to less pronounced wear protective layers.
REFERENCES: 1. Osarenjen, CRC Press (2015), 2. Rojacz, Tribol. Int. (2017), 3. Varga, Wear (2017), 4. Zum Gahr, Elsevier (1987), 5. Varga, Tribol. Int. (2013), 6. Fischer, Wiley VCH. (2008) 7. Varga, J. Eng. Trib. (2006), 8. Antonov Wear (2007), 9. Rynio, Wear (2014).
ACKNOWLEDGEMENTS: This work was funded by the Austrian COMET Program (Project K2 XTribology, no. 849109) and carried out at the “Excellence Centre of Tribology”.