the specific pivoting angle of the bearing. The tests were performed with grease.
RESULTS AND DISCUSSION: It could be shown that the surface structuring has a major influence on the achieved frictional properties of the bearings. The micro-texture allowed to reduce the frictional torque by half. The measured frictional torque over the pivoting angle for a standard bearing in comparison to a textured bearing is shown in Fig. 1. The low frictional torque resulted in less wear on the bearing surfaces. Especially in this field, a friction reduction results in significant energy saving. For the textured surface the wear on the surface could be drastically reduced. Subsequently, the findings are transferred to the production of constant velocity joint shaft prototypes.
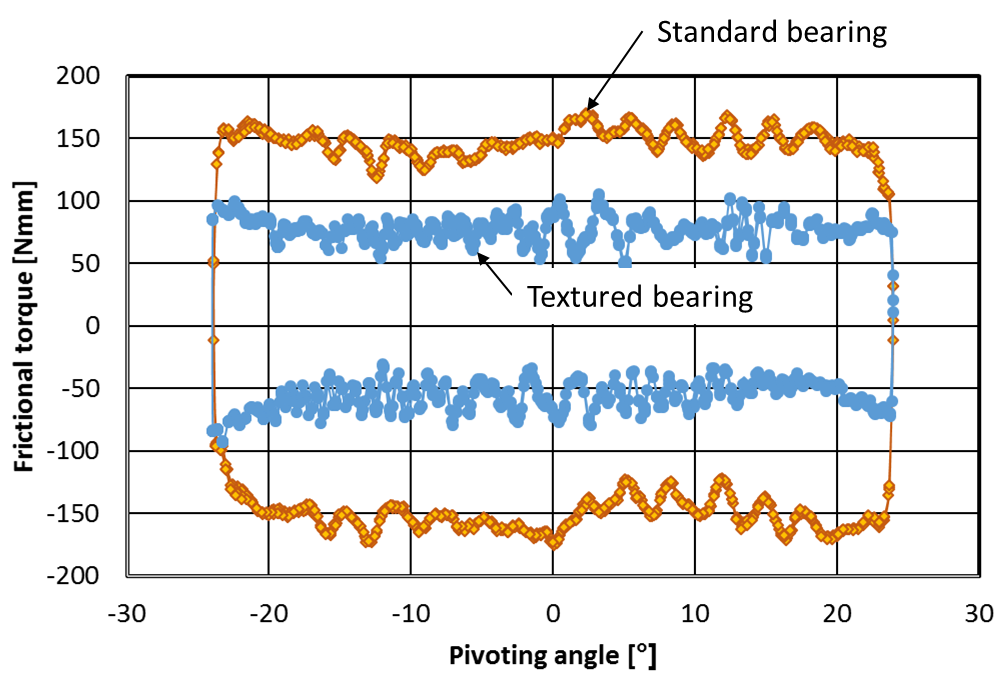
Figure 1 - Frictional torque over the pivoting angle.
CONCLUSION: The surface structuring with small cavities resulted in a reduction of frictional torque and wear at the reversal points of the bearings. It can be concluded that the cavities provide the tribological contact with lubricant at the reversal points. Thus, structured surfaces enhance the functionality of oscillating bearings. The requirement of higher ressource efficiency could be fulfilled. To save ressources due to lower wear and reduced friction the surface structuring with a one tooth chamfer is a feasible option for bearings oscillating under small pivoting angles. It is expected that in case of constant velocity joint shafts such structures will improve the tribological contact conditions.
REFERENCES: 1. Wakuda, M., Yamauchi, Y., Kanzaki, S., Yasuda, Y., Effect of surface texturing on friction reduction between ceramic and steel materials under lubrication sliding contact, Wear, Vol. 254, 356-363, (2003), 2. Kästner, J., Methode zur spanenden Herstellung reibungsminimierender Mikroschmiertaschen, Thesis, Hanover, (2013). 3. Denkena, B., Böß, V., Nespor, D., Samp, A., Kinematic and stochastic surface topography of machined TiAl6V4-parts by means of ball nose end milling, Proceedia Engineering, Vol. 19, p. 81 – 87, (2011), 4. Pape, F., Neubauer, T., Maiss, O., Denkena, B., Poll, G., Tribological Investigations of Angular Contact Ball Bearings Operated under Small Pivoting Angles for Production Process Analysis, Proceedings, 7th International Conference on Tribology in Manufacturing Processes, Phuket, Thailand, pp 190-199, (2016), 5. Ulmer, H., Dinkelacker, F., Engelke, F., Reithmeier, E., Denkena, B., Göttsching, T., Hübsch, C., Bach, F.-W., Fast, H., Rienäcker, A., Microstructuring of Thermo-Mechanically Highly Stressed Surfaces for Application in Internal Combustion Engines, WTC 2013, 5th World Tribology Congress, Torino, Italy, (2013)