average weight loss and surface roughness were noted. To investigate the wear behavior, the morphologies of worn surface and cross-sections of wear samples were examined by using SEM and color 3D laser scanning microscope(VK-9710). After the wear test, the pin samples were prepared with the taper-section method to observe the morphologies of worn surface and subsurface [25-27]. Moreover, the pins after abrading were plated by nickel with about 50 um thickness, followed by cutting along vertical direction, and then the microstructure characterization of vertical sections against the worn surface was observed by SEM.
RESULTS: The abrasion resistance of Fe-B alloy is investigated as a function of the Vm/Vp, and an empirical relation is attempted to correlate the weight loss and surface roughness with the Vm/Vp as shown in Fig.1. Clearly, there’s sort of an approximate relationship between weight loss and Vm/Vp here: y=1.4553+1.5461exp (-0.4012x), and the Vm/Vp is related to the surface roughness with a relationship of y=1.666+0.58471exp (-0.5516x). It can be obviously seen that the weight loss and surface roughness decrease with the increase of Vm/Vp, especially for the stage of Vm/Vp less than 3.7. The specific reasons for this phenomenon are discussed in some detail hereinafter.
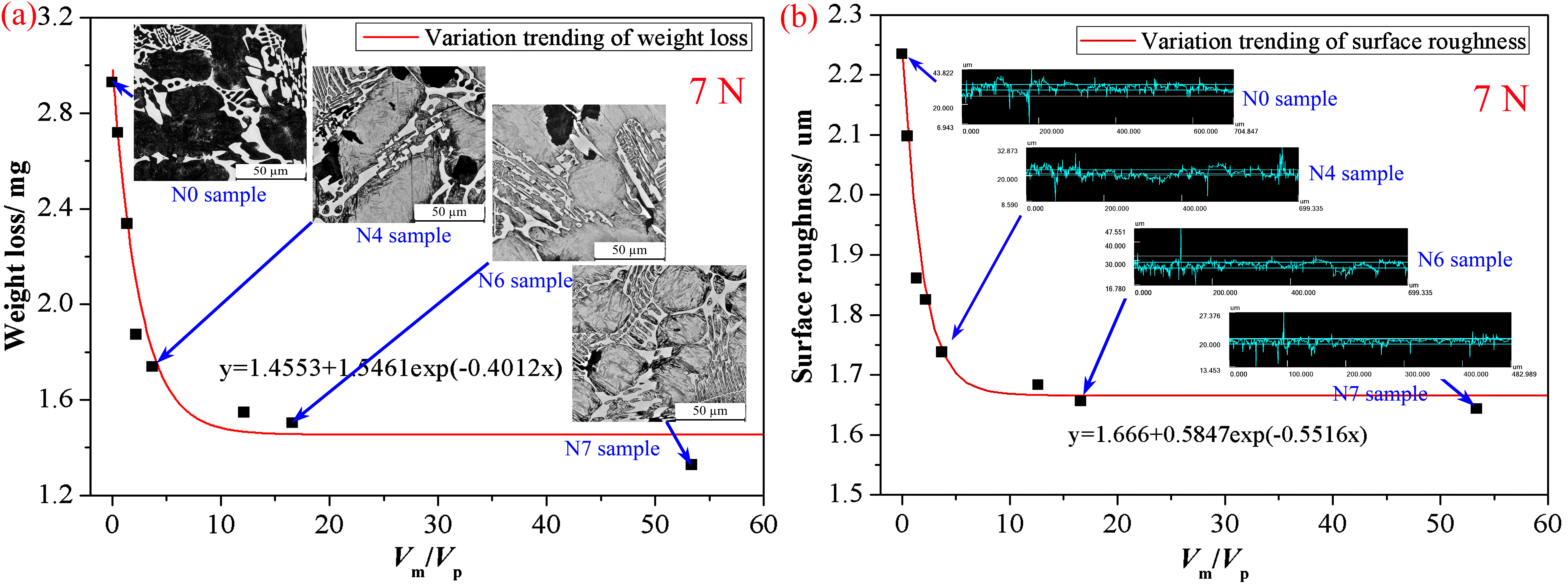
Figure 1 Wear weight loss and surface roughness as a function of the Vm/Vp under 7N normal load: (a) Weight loss; (b) Surface roughness.
DISCUSSION:
Under the constant contact stress, with the addition of Cu and Ni additions, the abrasion resistance of Fe-B alloy increases (especially for the stage of Vm/Vp exceeding 3.7 (where Vp and Vm show volume fraction of pearlite and martensite, respectively)), and the wear mechanism changes from microploughing to microcutting. The wear process can be described as follows: with the decrease of Vm/Vp or the increase of normal load, the neighboring M2B will be crushed by F⊥ owing to high degree of plastic deformation of matrix, and the broken M2B debris will be eradicated and dislodged by Al2O3 abrasive, so that the abrasion resistance of Fe-B alloy reduces greatly as a result. Accordingly, it was proven that the Fe-B alloy with martenste or high Vm/Vp matrix can be effectively subjected to severe abrasive wear in the low contact stress.
REFERENCES:
1.S. Aso, J. Jpn. I. Met. (1997), 2. A. Wiengmoon, Mater. Chem. Phys. (2011), 3. H.G. Fu, Mater. Sci. Eng. A (2007), 4. R.J. Chung, Wear. (2009), 5. C. Scandian, Wear. (2009), 6. R. Nieminen, Wear. (1994), 7. J. Liu, Wear. (1993), 8. C.Q. Guo, China. Foundry. (2008), 9. C.Q. Guo, J. Mater. Sci. (2004), 10. Y.L. Yi, Mater. Sci. Eng. A (2017), 11. J.J. Zhang, Tribol. Lett. (2011), 12. D.W. Yi, Tribol. Lett. (2012), 13. D.W. Yi, Tribol. Lett. (2015), 14. Z. Lv, Corros. Sci. (2016), 15. S.Q. Ma, Corros. Sci. (2014), 16.S.Q. Ma, Acta. Mater. (2016), 17. H.G. Fu, J. Mater. Eng. Perform. 22(2013), 18.
J. Gu, Mater. Test. (2015), 19. S. Sen, Surf. Coat. Tech. (2005), 20. C. Martini, Wear. (2004), 21. O. Ozdemir, Vacuum. (2006), 22. M.S. Li, Acta. Metall. Sin. (1995), 23. S.Q. Ma, Corros. Sci. (2011), 24. O. Ozdemir, Vacuum. (2006), 25. Y.X. Jian, Tribol. Int. (2016), 26. Y.X. Jian, Tribol. Int. (2016), 27. Y.X. Jian, Wear. (2016)