main influencing factor of wear resistance (not shown). Fig. 1B shows the oblique section through worn surface under 35N load of high boron high speed steel with 3.0wt% B. It is seen that there are only ploughings on the worn surface. Besides, no cracks or other defects are observed on the oblique section.
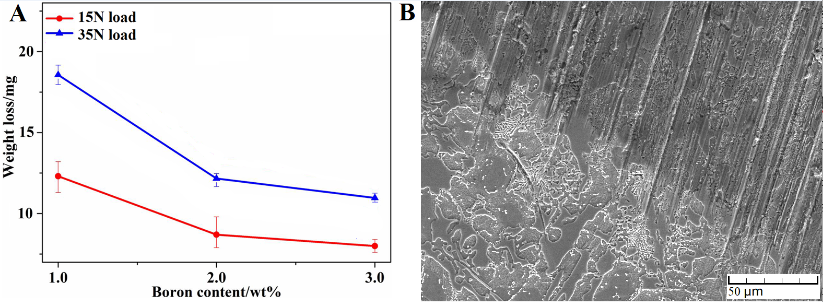
Figure 1 - A) Weight loss of high boron high speed steel with different boron contents and loads. B) Oblique section through worn surface under 35N load of high boron high speed steel with 3.0wt% B.
DISCUSSION: As is known to us, borocarbide acts as hard phase to resist abrasive particles, protecting matrix from being damaged directly, while matrix supports borocarbides. The synergistic reaction has a positive effect on wear resistance of high boron high speed steel.7 According to the theory of Ref. 48, the ratio of hardness of abrasive SiC (HV2600) and eutectic borocarbide (HV1400-1800)8 is below 0.8, which means that SiC can be regarded as hard abrasive. In alloy with 1.0wt% B, only small-size borocarbides exist, which are easy to be fractured by moving abrasives. Consequently, ploughings, pits and scratches caused by abrasive and broken borocarbides appear on its worn surface. When boron content increases to 2 or 3 wt%, only ploughings are observed because the size of borocarbide becomes larger, it is difficult to be broken by abrasives.
By observing the oblique sections together with worn surface morphologies, it is proved that the wear mechanism of alloy with 1.0wt% B is micro cutting accompanied with spalling of borocarbides. Rest of the alloys are single micro cutting From Ref.7, borocarbides with Cr, Mo, and V addition have excellent toughness, so no cracks are observed on borocarbides.
REFERENCES: 1. Z. Lv, J. Alloys Compd. (2016), 2. J. Gu, Foundry Technol. (2011), 3. S. Ma Acta Mater. (2012), 4. S. Ma, Mater. Sci. Eng. A (2010), 5. H. Asahi, ISIJ Int. (2002), 6. X. Li, Materialwiss Werkstofftech (2015), 7. Y. Jian, Tribo. Int. (2016), 8. H. Fu, Mod. Cast Iro. (2005)