Wear of PTFE /PEEK Composite: Theory and Experiments
Shuren Qu, King H. Lo, Su-Su Wang
Composites Engineering & Applications Center (CEAC), University of Houston, Houston, Texas
INTRODUCTION: Polyetheretherketone (PEEK) is an engineering thermoplastic polymer known for its outstanding thermal stability, chemical resistance and wear resistance. Despite its outstanding properties, high friction of neat PEEK is a concern in tribological applications. The addition of solid-state lubricants, such as PTFE, to PEEK polymer significantly improves its friction and wear performance.1-3 In PTFE/PEEK composite the development of transfer films at the sliding-contact interface attributes to the improvement of its wear resistance.4 It is recognized that in the Archard abrasive model the wear is inversely proportional to hardness.5 However, PTFE/PEEK composite violates the Archard wear law with low hardness but also low wear rate. While a substantial amount of research has been conducted to investigate friction and wear of PTFE/PEEK composite,1-3, 6, 7 rigorous theories do not exist to predict friction and wear performance of the PTFE/PEEK composite.
The objective of this paper is to establish a relationship between frictions and wear and develop a rigorous wear theory for PTFE/PEEK composite by considering composite microstructure, transfer film lubrication and individual phase materials characteristics. A series of experiments were conducted to provide a micromechanics wear model for the theory development and for its subsequent validation. In order to reach this goal, an effort is made first to relate the wear of PTFE/PEEK composite to friction and wear of its constituent phases. Power-law relationships are established between friction and wear of individual constituents and the composite. A composite-mechanics-based wear theory is developed to determine the specific wear rate of the PTFE/PEEK composite. Good agreements between theoretical predictions and experimental results for the PTFE/PEEK composite with up to 20% (by volume) PTFE. Further validation of the wear model and theory is also carried out with the reported friction and wear of PTFE/PEEK composite in the literature.
THEORY AND MODELING: The specific wear rate of PTFE/PEEK composite is found to relate to friction coefficient by a power law relationship (Figure 1A). The specific wear rate and the friction coefficient of the PTFE in the composite remain the same as those of neat PTFE, due to the presence of transfer films (Figure 1B) at the interface. Also the specific wear rate of PEEK in the composite is considered to follow the same power law relationship as that of neat PEEK. The friction coefficient of the composite is constructed with the rule of mixtures of PEEK and PTFE. The friction coefficient and the wear rate of PEEK in the composite can be determined with measured friction coefficient of composite and neat PEEK wear rate, respectively. A rigorous wear theory is then established for the composite, based on friction and wear of the constituent phases. The predicted specific wear rates of the PTFE/PEEK composite are shown in Figure 2 (solid lines).
.
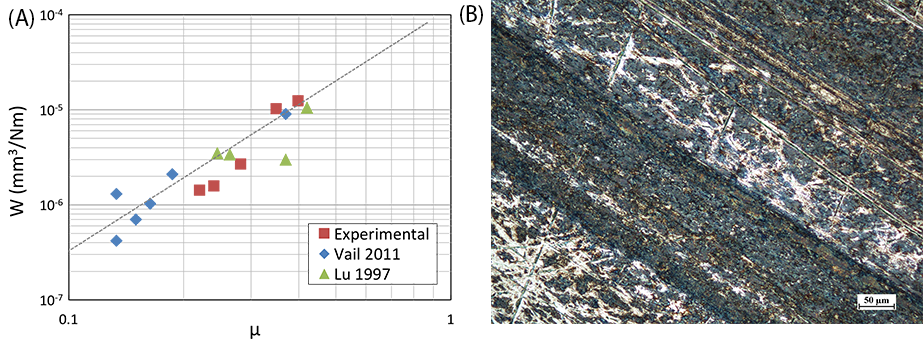
Figure 1 – (A) specific wear rate and friction coefficient of PTFE/PEEK from current experiments and literature2, 3. (B)Transfer films on steel counterface tested on PTFE/PEEK composite with 15% PTFE (by volume).
EXPERIMENTS AND RESULTS: Wear tests were performed on a pin-on-disk tribo-tester at room temperature. Cubic PTFE/PEEK composite pins were slided against a carbon steel counterface with surface roughness (Ra) of 0.1 μm. (The sliding speed was 1 m/s and the applied normal pressure was 0.5 MPa). Neat PEEK, neat PTFE and PTFE/PEEK composite with 0-20% (by volume) PTFE were tested. Total test duration was 48 hours. The first 24 hours were the “running-in” period. Test data were collected during the second 24-hour period.
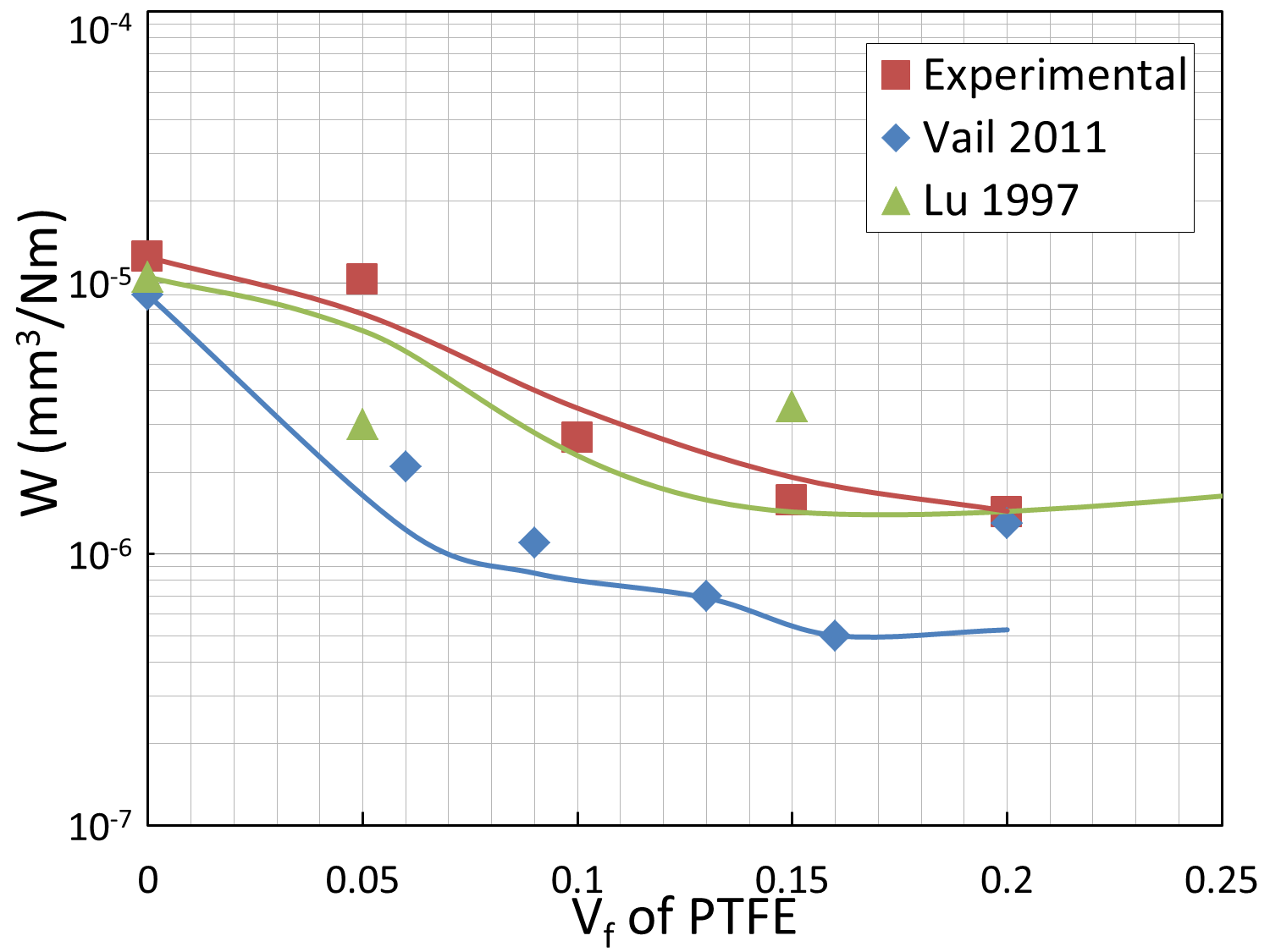
Figure 2 - In-house test results (square), literature data (triangle and diamond) and theoretical predictions (solid lines) of specific wear rate plotted against volume fraction of PTFE.
In Figure 2, the specific wear rate of PTFE/PEEK composite decreases with increasing PTFE volume fraction. Corresponding measured coefficient of friction of the PTFE/PEEK composite, used in predicting the composite specific wear rate is shown in Figure 1B.
REMARKS ON TRANSFER FILM: During sliding of PTFE/PEEK composite on the steel counterface, transfer films were formed from the PTFE coming out of the composite and modify the contact interface (the steel counterface). Hence, the specific wear rate of neat PEEK sliding against the steel counterface will be different from that of the PEEK phase in composite. To account for the change of the contact interface with the PTFE film, the specific wear rate of the PEEK constituent in the composite is determined with inclusion of PTFE. Friction of PEEK in the composite is also determined with the friction coefficient of the composite and its relation to those of the PEEK and PTFE phases. We note that the current wear theory is based on microstructure model and is valid for a low concentration of the PTFE phase. In the composite, PTFE serves as a solid-state lubricant and introduces the transfer films. The PEEK material in the composite slides on the transfer film is different from sliding on the metal counterface. The extent of the interface coverage by the transfer film affects the sliding interface conditions (surface roughness and adhesion).
REFERENCES: 1. Burris. Wear (2006), 2. Vail. Wear (2011), 3. Lu. Wear (1995), 4. Lee. Wear (2002), 5. Archard. Proc. R. Soc. Lond. A (1956), 6. Briscoe. Wear (1986), 7. Bijwe. Wear (2005)